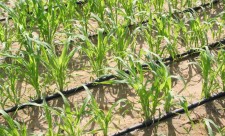
Metal workbenches - how to make with your own hands Instruments
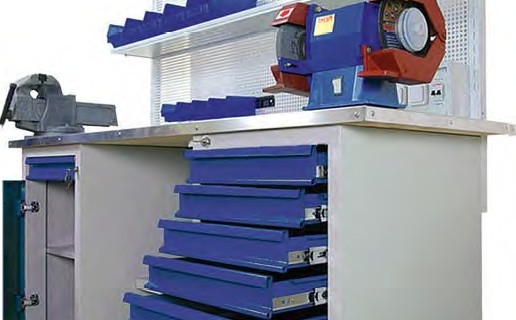
In the garage or in the workshop, it is necessary to store various tools, and the workplace must be convenient. To do this, it is necessary to buy a metal workbench, the most adapted to the nature of the activity. It is a stronger wooden, its service life is almost unlimited. The information set forth in the article will help to determine how the workbench should be.
Content
Varstakov varieties
All workbenches are classified as follows.
- Metal locksmith workshop: It is the basis of a hard frame of metal corners and a lid on which vice is attached. The margin of the strength of such a workbench should be such that the design sustain a strong punch with a sledgehammer. This is necessary for processing metal parts.
- The workbench is a carpentry metallic: in its structure, it is not significantly different from the plumbing. For convenience, it can have a height-adjustable cover and a special focus for planing of boards.
- Carpenter: It has great dimensions, which is necessary for assembling door blocks and window frames. It can be equipped with a circular saw.
Any of these workbenches can be universal, adapted for different types of work. In addition, the design of metal workbenches can be divided into the following types.
- One- or multi-dimensional. The length of the first does not exceed 2 m and they are designed to work one person. Multipity is used in large shops of industrial enterprises, their length is selected depending on the number of jobs located in one row. Width of the workbenches - in the range of 0.7-0.8 m, height is 0.9 m.
- By the number of Tumb Vistaks are one-, two- and flirting. The latter are not equipped with shelves and storage boxes tools. Other options are distinguished by the number of Tumb spaces located on the left and (or) to the right of the workplace.
- According to strength, they are divided into ordinary (their countertop is made of sheet metal with a thickness of 3 and 5 mm) and reinforced. The latter are equipped with a tabletop of a steel plate with a thickness of 10-30 mm. A screen in the form of a height of about 150 mm is attached to the back of a height of about 150 mm, which is made of perforated metal. In addition to welded connections, reinforced workbenches have bolted parts of parts.
How to make a workbench yourself
Metal workbenches, the price of which can be several hundreds of C.E., do not hurry to get acquired. If there is a necessary tool and skills to work with them, you can make a metal workbench with your own hands. For work, you will need such materials, fixtures and tools:
- steel sheet (thickness is regulated by the purpose of the workbench);
- metal corners (50 × 50 mm) and pipes with a diameter of 40-50 mm for the manufacture of legs and frame;
- bulgarian;
- welding machine;
- electric drill with a set of drills;
- file;
- roulette;
- screws, nuts;
- hammer;
- metal paint, brush.
Ten rules manufacturer of workbench
- Planning the installation location follows closer to the electrical outlet: many tools require connecting to electricity. It is important to take into account if there should be a circular saw or sharpened on the workbench cover. It is recommended to provide a block of electrical outlets above the table top.
- For manufacture, it is necessary to use materials with a margin of strength.
- In order not to emerge unexpected complications, a drawing of a metal workbench is needed. Initially, a sketch is performed, which indicates the main dimensions, and then the drawing of each part.
- It is recommended to provide for the presence of shelves and boxes for storing tools.
- The table of the workbench should be made of a thick sheet with a perfectly smooth surface. The width of the workbench is not more than 600 mm: it is necessary to get free to tools from the distant edge.
- The height of the workbench is determined by this: the hands are pressed to the body along the body, and the palms must be parallel to the floor. The distance from the floor to the palm and will be the height of the workbench, selected individually for the wizard.
- To work with the cutting tool on one of the lateral parts, there must be a protruding part of about 250 mm long.
- In order for the workbench to be stable, the "pyataks" with a diameter of 90-100 mm are welded to the legs. The legs may have holes for screw mounting to the base. To reduce the noise level, pads from felt should be placed under the legs. Between the legs should be jumpers at the bottom. On top of the jumpers can be arranged a shelf for large tools.
- In the tabletop for clamps and stops make special holes. The workbench must be equipped with shelves and drawers, while their design should be such that the loss is impossible.
- The base (exposure) must be massive: this is the main condition for its stability.
These rules belong to the workbenches of any size, type and destination. They should correspond to both the industrial manufacturer's workshop, and their own collected.
Step-by-step manual manufacture of metal workbench
Using the drawing, you need to make all the details in accordance with the specified dimensions, and then connect them using welding. The whole process can be divided into the following steps.
- From the thick metal plate, the gas welding machine is cut out a worktop and an exposure. All irregularities are aligned with a hammer, warming up the edge of the part. A thick slab can be replaced with several sheets: metal up to 10 mm is better cut with a grinder. Sheets are connected by welding around the perimeter.
- Metal pipes or 50 × 50 mm corners are cut out parts for frame and combined with welding. The connection strength check the hammer to the welding seam by knocking down at the same time. If necessary, the joints of the joints boil several times.
- The table top and exposure put in their place and weld in several places around the perimeter.
- From the sheet metal, a thickness of 3 mm cut the parts for the screen and fasten it at the rear wall.
- Shelves and drawers are made of a sheet metal with a thickness of 3 mm. From the corner of 25 × 25 collect guides for drawers or shelves for shelves. Fasten the shelves to corners in any way (welding or with screws).
- All edges should be treated with a file so that there are no burrs. The surface of the vestica is covered with special paint for metal. It will prevent corrosion formation.
- Through the holes in the "Pyataks" under the legs make markers on the base and drill holes for anchor bolts. After that, the workbench can be fixed (without forgetting to put felt washers).
- Installed on the place intended for them, fasten them with screws. Under the nuts put engravers.
- The workplace should be well lit: the lamp is installed above the workshop so that the light from it is not directed into the eye.
How to operate the workbench
Metal workbench does not require special care. The life of its operation is almost unlimited. Just follow these rules:
- After work, all tools must be removed into place.
- Chips are sweeping into a scoop by a broom, after which the tabletop is wiped with a rag.
- The stains of oil and paints wipe with a rag moistened with gasoline.
- Tabletop, legs and drawers periodically color: it is necessary to protect against corrosion (especially if the operation is performed in a room with high humidity).
- At the end of the work, all power tools and devices are disconnected from the network.
Using the recommendations set out in the article, any master can choose a suitable special furniture in a workshop or make it yourself, saving not small tools.
In conclusion, the video of what should be a comfortable metalwork workbench should be.