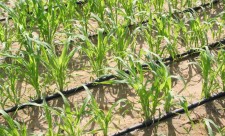
We warm the basement at home with your own hands. Heat insulation basement - Tips from specialists Insulation,Useful advice
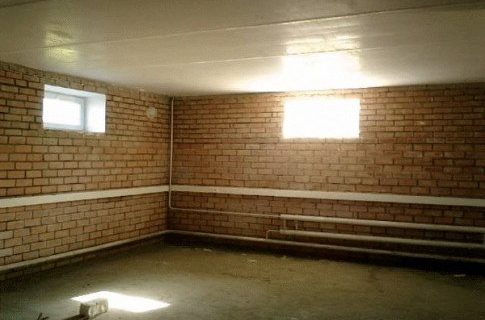
The cellars of modern cottages are not like a vegetable store. Spacious premises can be used as workshops, gyms, billiards. This is possible subject to the creation of the necessary microclimatic conditions. Therefore, even before the start of construction, it is necessary to decide how to protect the basement from the frost. This is also important because a quarter of total heat losses occurs due to poor insulation of basement rooms.
Content
Methods of thermal insulation basement: outside or from the inside?
We suggest to consider the main schemes of the basement insulation (see below).
The insulation of the basement outside is more efficient for the following reasons:
- guaranteed lack of condensate on the walls;
- warming materials do not occupy useful volume;
- it requires less materials (cost-effective);
- creaters are eliminated.
IMPORTANT: Before proceeding with insulation, you must apply on the walls below the ground level, waterproofing material. Pre-Walls are aligned and processed by an antiseptic.
Outdoor insulation technology basement: the main stages
For insulation of the walls of the basement from the outside, tile materials are used, resistant to moisture. Installation is performed using mastic in compliance with the following rules.
- Mastic is applied to the entire surface of the wall with a uniform layer, as well as to the surface of the insulation. This allows you to make them connect reliable.
- After applying mastic, the insulation should be pressed against the wall for 30-40 seconds.
- Installation of plates is made from below-up with a dense adjoining. The gaps are filled with polyurethane foam mounting foam.
- When performing reverse swelling of the walls of the foundation, the soil must be monitored so that the insulation plates do not shift.
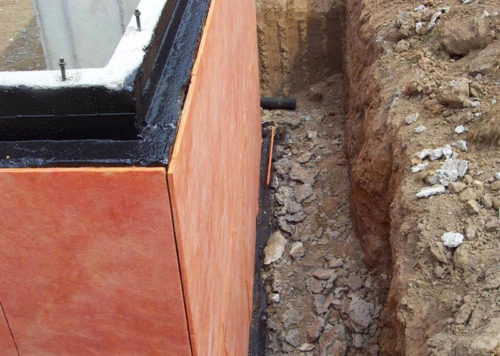
Plates of extruded polystyrene foam plates are pasted on bitumen mastic
In addition to bitumen mastic, liquid rubber or water-based polymer-bitumen mastic can be used. For applying on the walls, a spatula, brush or roller.
Floor insulation in the basement
Through the floor and the overlap of the basement, if they are not insulated, the larger amount of thermal energy is lost than through the walls. Floor insulation should be carried out so that its surface can withstand high mechanical loads.
Thinking on how to choose a heater for the basement, it should be borne in mind that the material should be resistant to moisture. Mineral wool, glass gamble and other similar insulation do not use.
Types of thermal insulation materials for the basement:
- extruded polystyrene foam;
- styrofoam;
- sand;
- ceramzit;
- coal slag;
- charcoal wood;
- peat.
Fractions of ceramisite for floor insulation:
- sand (mixed in concrete);
- crushed stone (coarse particles of irregular shape);
- gravel (particles of 10 mm and more, rounded form).
Tip: All three clamzite fractions should be used to fill the entire volume of the insulation layer. It is desirable that all the granules are integer without chips.
There are two ways of floor insulation in the basement:
- on the soil with the subsequent device of the concrete screed;
- filling the voids between the lags of the boarded floor.
The insulation of the basement clamzite on the soil is performed in the following order.
- The top layer of the soil is removed (approximately 250 mm).
- Foundation is prepared: aligned and trambed.
- A drainage layer is poured (about 150 mm thick) rubble of a large fraction (more than 50 mm) or broken bricks. Mound trambed.
- Drainage is impregnated with molten bitumen.
- We warm the basement with sand: the layer is poured (up to 100 mm), which will also be trambed. Sand should be used coarse-grained.
- Bitumen flooded over the sand over the sand.
- The rubberoid is placed on the walls on the walls - at least 100 mm.
- Equally applied with a layer of clay (150-200 mm).
- The reinforcing grid is stacked, "lighthouses" are established.
- A concrete screed with a thickness of at least 50 mm is satisfied.
- Decorative coating is stacked.
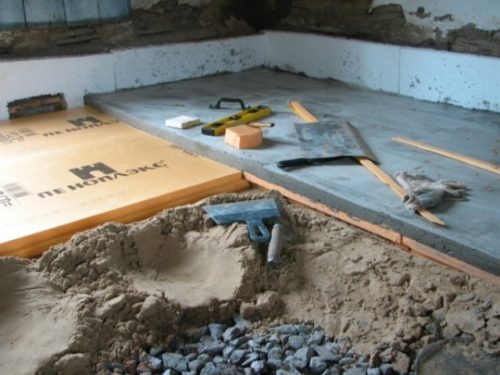
Multilayer pie from various materials allows you to warm up the floor in the basement
The insulation of the floor to fill the space between the lags of the board of the board is performed in compliance with certain rules.
- The ticks remove nails, remove the boardwalk.
- Between the lags, we laid the waterproofing material - polyethylene film or rubberoid. It is important that lags are also covered.
- Foams is poured or foam (expanded polystyrene foam).
- Parosolation film is stacked.
- Floor or plywood boards are laid and attached.
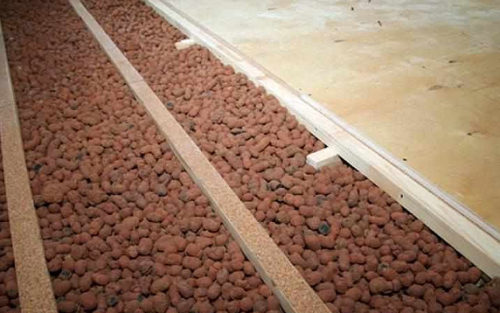
Between the lags of the floor falls asleep clamzit
There is another way of a warmed floor device - with the help of drying sheets (GVL).
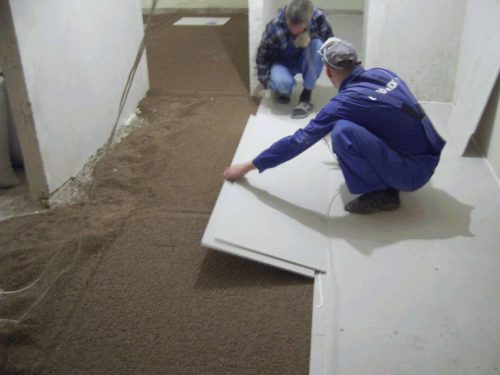
Laying of GWL over clamzite swelling
The technology lies in the laying of GVL "floating" in the way on top of the bulk insulation (usually clay), aligned by beacons. For better fastening and sealing the connection of the locks of the GWL to the place of the joints, glue sealant is applied. On top of the GWL, the finishing coating is stacked (for the basement it is recommended to use linoleum or ceramic tiles).
Important: To compensate for thermal expansion along the wall, the edge ribbon of foamed polyethylene is placed.
Methods for insulation of the walls of the basement
It is not always possible to perform outdoor insulation, and the only option becomes necessary to perform the necessary internal work.
The heat insulation material for walls in the basement can only be used tiled, low hygroscopicity (not absorbing moisture). These include foam and extruded polystyrene foam. The foam is recommended to use a 50 mm thickness of the PSB-25 brand. The work technology consists of the following steps.
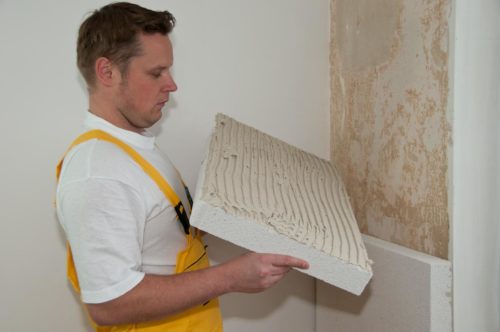
Sticking plates of foam on the wall
- The walls of the basement are cleaned of fungi and mold mechanically, after which they are processed by antiseptic and primer deep penetration.
- The surface of the walls is leveled with cement-sandy solution.
- The toothed spatula is applied and evenly distributed over the wall of frost-resistant glue.
- Foam plates are pressed against the wall and are additionally strengthened with plastic umbrella dowels. Plates are joined closely.
- The gaps between the plates are filled with assembly polyurethane foam. After frozen, the excess foam is cut.
- A vapor barrier film is pasted to prevent condensate formation.
- A plaster mesh is pasted on top of the wall and a plaster mix for internal works is applied. This is a necessary measure to protect (isolation) easily flammable material. Later the walls can be painted.

Additional strengthening of foam plates dowels with a wide hat
It should be borne in mind: the insulation of the basement foam is not recommended if the room is intended for a long stay in it in it.
Similarly, the walls are insulated with the plates of extruded polystyrene foam. Due to high density and low thermal conductivity, the use of plates with a thickness of 25-40 mm will be quite effective.
How to insulate the basement ceiling
The ceiling is possible the formation of condensate. To prevent this, thermal insulation material is fixed on its surface. It is recommended to use plates of polystyrene foam or foam. Work can be performed subject to the absence of moisture on the ceiling: first it is necessary to ventilate the basement. For ceiling insulation, you must do the following.
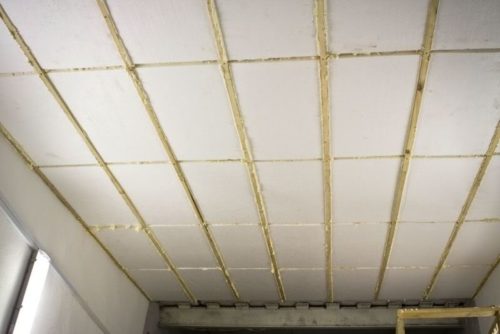
View of the ceiling insulated foam in the basement
- The plates are applied adhesive mixture and pressed to the base surface. For temporary fixation, it is necessary to provide backups from bars and boards.
- Using the perforator, drill holes for dowels. They must be placed with a density of 5-6 pieces / m².
- The holes are driven into the holes, dismantle temporary backups.
- The mounted foam fill the gaps between the plates, excess after the harvesting is cut off.
- Put the plaster grid, apply an aligning gypsum solution.
Also applies the technology for applying polyurethane foam by spraying. Such a heater completely covers the surface of the ceiling, filling all the cavities and microcracks. But to perform this work will require special equipment and skills.
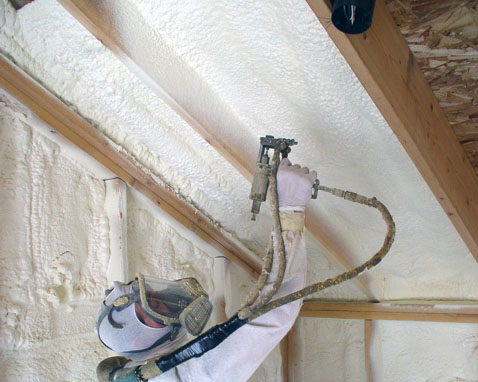
Ceiling insulation by spraying
Warm the door of the basement
For insulation of metal hollow doors, we use the following technology.
- Breeping in the cavity of the door leaf wooden rails. In the perimeter (from the end side), drill holes with a cencle to the countersunk hats of the screws. Reiki Krepim around the perimeter of the canvas and in several rows horizontally.
- Insulation, as we use foam or polystyrene foam plastic, is installed between the risks of the Muspiece.
- Clauses are filled with mounting foam.
- On top of the insulation to the slats with self-drawers, the leaf metal with a thickness of 0.5-1.0 mm.
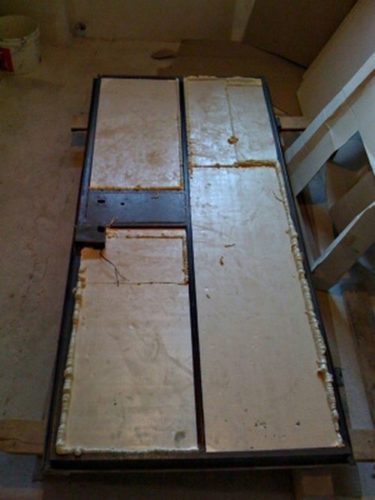
Foam-insulated doors
IMPORTANT: In order for the basement insulation measures to be effective, the installation of the drainage system and the concrete scene should be installed. This will avoid the freezing of soil and reduce the loss of thermal energy.
At the end of the article, we suggest familiarizing yourself with how the outer insulation of the basement is performed: video with explanations of a specialist.