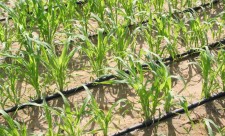
How to make a machine for cold forging Instruments
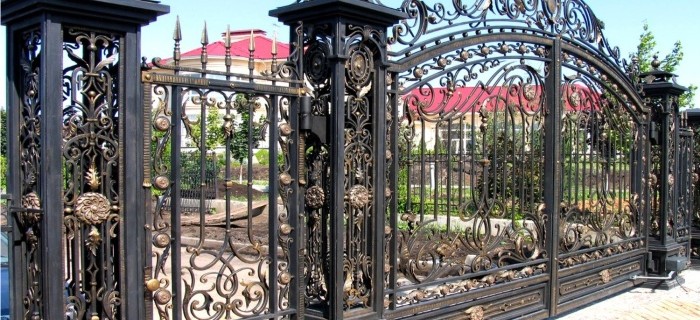
Metal structures are very popular with the arrangement of private houses and apartments. Curved products bring an extraordinary flavor to the interior and landscape design and allow you to create a very attractive artistic picture. Many owners of their own cottages seek to make them unique, and for this purpose, stamped details are not suitable. Universal and special tools from producers are quite expensive. Therefore, the appropriate question arises: how to make the machine for a cold forging with their own hands from the girlfriend.
Content
Why do you need a tool for cold forging?
The cold forging process is greater simplicity and safety than hot. First of all, due to the fact that metal inclusion is not required and strict adherence to the temperature regime throughout the work.
A homemade machine for cold forging can be universal or intended for the manufacture of details of a specific format. No matter how much the option is more suitable, with your own hands the tool will solve several tasks:
- obtaining ideal details geometry for a specific design idea;
- cost savings;
- creating a complete set of parts with a unique pattern;
- save on the choice of a suitable room - for cold forging does not require special conditions and large space, the machine can be installed even in the garage.
Important! Before you begin to develop a drawing, browse the photo of finished cold forging machines to know what the result you need.
What can be done on a cold forging machine?
For artistic cold forging, soft metals are most often used - this is:
- duralumin;
- copper;
- steel;
- brass;
- magnesium alloys;
- nickel-based alloys.
Important! The choice of a specific option depends on the color range and used materials for all surrounding items in the interior or at the local area.
The range of possible forged metal products does not have any restrictions - it all depends on your personal fantasy and opportunities. Most often use openwork details for:
- organization of stairs;
- assembling fences and fences;
- installations of mangals;
- decoration of fireplaces;
- creating separate decorative elements - coams for flowers, wall decoration, etc.
What are the cold forging machines?
The varieties of cold forging machines are a lot:
- Gnutic - a device for bending parts at a given angle or for arc bending.
- Snail - pattern (solo or with removable details of different sizes) to create spiral elements.
- Twister is a tool with which the start of the initial part is made along the axis.
- Wave - With this cold forging machine, create wave-like parts from the rod.
- Tool for molding rings.
- Press for a matrix imprint with pressing.
- Universal tools for cutting, giving volume, riveting.
Important! Functioning such machines can both with the use of manual strength and by means of an electric motor. The second option allows you to fulfill all the work a little faster, but also requires a certain effort and skills from an employee.
How to make a machine for cold forging with your own hands?
To date, there are many design solutions for the manufacture of homemade cold forging machine. Homemade craftsmen use the most unexpected tools and equipment for reworking the desired tool. In this article below you will find the drawings of the most popular instruments for manual metal forging and detailed assembly instructions.
Drawings of cold forged machines
How to make a whole snail machine at home?
Very often, when assembling any openwork metal structures, spiral elements are used. It is for the manufacture of such parts of one size that this machine is suitable.
Instruments
To perform work, prepare:
- sheet steel;
- steel stripes;
- rods;
- profile pipe;
- bulgarian;
- welding machine;
- emery;
- roulette;
- marker;
- pliers;
- paper and pencil.
Instructions for assembling solid machine
To get as a result of your work a reliable tool with suitable parameters, act like this:
- Make on paper Future spiral spiral on 3 turns.
- Remove the parameters so that the threads inserted the rod with a cross section of 10 mm inserted.
- Cut 2 plates from the sheet: one - 100 * 100 mm, the second is 130 * 130 mm.
- Make 3 sections of 7 cm long from the profile pipe.
- Prepare 3 strips of steel and 3 cm rod.
- All items pre-process on the edges of the sandpaper to remove burrs around the cut.
- Bend the steel strip on the template - it is easiest to make it pliers. As a result, you should have 3 spiral plates of different lengths.
- We weld all the details according to the scheme by setting the rod to the very short spiral - it will provide reliable fixation.
- The most recent weld in the center below the profile pipe.
Important! Perform all welding work very responsibly - the wear resistance of the tool directly depends on the quality of fixation.
Video
As a result of the work performed, you will have such a cold forging machine, as in the applied video. There you can visually view the sequence of your action when assembling.
How to make a set of a snail?
The basis of the design of the set snail is not much different from the previous machine. It will also be necessary to cut the base plate from the steel sheet to which the set details will be fastened. Next do the following:
- From the steel plate, form the pliers of the central (initial) element for the bend spiral.
- Apply the strips to the base and mark the marker on the layer seat substrate for drilling - you will then fix different sets of the set.
- Clean all sections on the billets of Eatak.
- We weld the central element to the base or fasten the retainers from the rods on this part and drill the hole at the installation site.
- We weld the profile tube and bar.
Important! Note that in the manufacture of this cold forging machine, it is very important to maximize all the parameters of the blanks and designate the places of their future fastening. Otherwise, you will not get an openwork item of the desired size.
Video
In the finished form, your snail will look like this.
How to make a torsion machine?
For such a tool of cold forging prepare:
- sheet steel;
- vice;
- bulgarian;
- fasters - nuts with bolts;
- lower reducer;
- electric motor;
- chain;
- welding machine;
- icline.
To quickly assemble the machine, follow the following sequence of actions:
- Take as the basis of the boutique.
- We weld on one side to it a steel sheet.
- To it, fasten the vice - weld and secure the bolts with nuts.
- Tisted the plate on top and bottom - it will exclude the slip of the metal during the tension.
- On the other hand, the heap will fasten the rollers, and install the platform on them.
- From above on this design, install and secure another vice, but with a moving central part.
- Make both the nodes on different sides of the height of the height.
- Again the handle from the steel rods - the rim, whose scrolling you will be flexing the metal.
- Connect an asynchronous engine with a lower reducer bolt.
- On the reverse side of the working unit - rim stewed, Torsion stretch the chain.
- Close it with steel casing.
Important! As a result of this work, you will have a machine with 2 blocks, one of which is fixed, the second - movable.
Video
In this video, the Torsion design is clearly shown to the collected form and the principle of operation on such a machine. Carefully read it to facilitate your work.
Conclusion
As you have already been convinced, in the presence of elementary skills of working with tools and clear development of the preliminary drawing of the machine, collect it easy. Put the target correctly, select the appropriate design type and mount the tool, acting sequentially. In this case, the quality result is guaranteed - you can easily make all openwork parts made of metal to decorate your home.