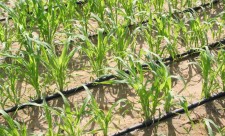
Alkyd varnish: features of application paints and varnishes
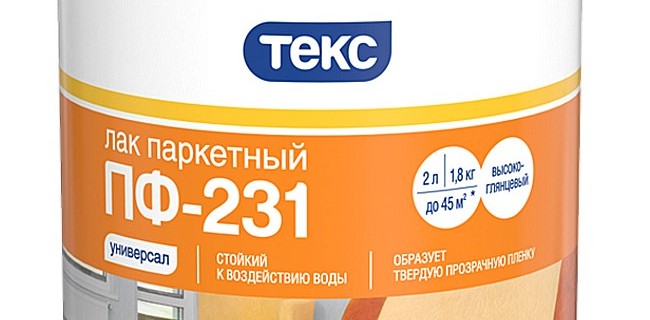
The floor lacquer today is a universal means: it not only provides wooden products and coatings high performance, but also gives them an attractive and colorful appearance. It consists of substances that reliably protect wood from the destructive effect of the acid and alkaline medium, with which the coating will be invariably in contact. Mushrooms and molds also do not spawn to natural material through a dense varnish layer.
Content
Pluses of lacquer for floors from natural wood are obvious, just can you say without unnecessary to say what kind of means to choose? In the article we will discuss one of the types of parquet - Alkyd varnish. Consider the physical characteristics of the means and its "behavior" after applying on a wooden coating.
Types of varnishing mixes
Lucky for gender Specialists are classified on 5 main species, which in a wide range offers a modern construction market. Among them:
- Water based mixtures.
- Soil compositions.
- Alkyd varnishes.
- Acrylic goods.
- Polyurethane mixtures.
In each form of products, we can note a number of undeniable "advantages" and strong operational parties. At the same time, it is impossible to leave without attention and the disadvantages of each type of mixture, because of which they cannot be applied everywhere. It turns out that the purchase of funds for the formation of flooring should be sent only after studying information on the product specifications.
Alkyd varnish and its features
Finally frozen, the alkyd varnish becomes a smooth glossy coating, which is distinguished by durability and water resistance. The material that was treated by alkyd composition is not terrible external stimuli. It is a pleasure to work with such a varnish: a thick remedy spreads well into a dense smooth film.
The composition of alkyd varnish, which covers pine, fir and oak floors, will certainly include alkyd resins. They are mined from natural raw materials - linen or wood oil. The secondary component of the means are organic solvents and fatty acids. Absupping into the porous structures of the tree, they reach the maximum depth and emphasize the natural beauty and uniqueness of the coating. Due to this, of course, the positive property of the alkyd varnish was widely used in working on internal and external finishes. Parquet alkyd varnish transforms wooden floors to unrecognizable: makes their shadowed range to a deeper, emphasizing the unique coverage texture. When the film is dried, it becomes matte and elastic.
Alkyd varnish does not know equal in resistance to sharp drops of temperature and change of humidity indoor. Not terrible tools and strong vibration loads. Moreover, lacquer properties absolutely alien properties: after applying too deeply in the floor slot, the agent does not penetrate, and therefore the screens and noise of the flooring are excluded. This is a water-soluble varnish. To process which coatings apply an alkyd varnish is most appropriate? Here is a list of suitable products:
- end parquet;
- parquet on the floor heated;
- "Floating" floors;
- parquet, the material for which was the capricious rocks of the tree, extremely persistently reacting to the change in the conditions of microcers in the room.
Speaking about the strengths of alkyd varnish, it would be unfair to teach about its shortcomings. The most comprehensive remedy has decreased due to prolonged frosted (at least 1 day), so after it is applied it is advisable to open the windows to air in the room - for the speedy frost, the lacquer will need a flow of fresh air. However, some manufacturers add special components to quickly unscrewed varnish. Another unpleasant moment - a varnish on an alkyd-based basis tends to wrinkle if it is not sucking and putting the means in the process of work and put on the coating. Ideally for 1 m 2 Coatings should be spent no more than 120 g.
The wear resistance of alkyd varnish for wood is low, and the service life does not exceed 2 - 3 years. It is not surprising that this tool is most often used not to cover wooden floors, but for processing furniture.
Features of the production of the newest alkyd varnishes
The most popular on the global paint market received an alkyd modified varnish. The technology of their production is based on the synthesis of substances of the URALOV, during which the alkyd components are associated with polyurethanes. The effect, as mentioned, is evident: the performance characteristics of the goods increase, in particular, the process of drying varnish after application (up to 12 hours) is significantly reduced. At the same time, the cost of alkyd modified varnishes is almost no different from the price of ordinary varnishes on an alkyd basis.
Popular brands of varnishes on an alkyd basis
PF-231 is one of the first parquet alkyd varnishes that began to produce in Russia. The remedy is well applied, the film has a neat appearance - in this indisputable advantage of the goods. However, there is also disadvantages: the coating is not solid enough to serve for more than 2-3 years.
MCh-0163 is a two-component agent consists of a parquet lacquer solution, which includes urea formaldehyde and alkyd resins, and acid hardener. Compared to PF-231, this alkyd varnish has the best operational properties: it is more water consuming, is durable and resistant to abrasives. Among the disadvantages, the means it is worth mentioning the darkening of its film under direct solar rays, poor elasticity of the film, a sharp saturated smell, the appearance of bubbles on the working surface in the process of applying varnish.
EP-2146 is a single-component alkyd-epoxy with improved operational characteristics. The modifying component of this parquet alkyd varnish is epoxy resin. The goods have high performance of hardness, water resistance and abrasive resistance. Used to apply to parquet coating, as well as for processing different wooden materials, including veneer, fiberboard, chipboard, plywood and textural decorative paper. Abroad analogs of EP-2146 does not exist.
Specificity of alkyd varnish
The tool must be applied in 2 to 3 layers, and each subsequent layer is glued only after the complete drying of the previous one (after 1 to 2 days). The consumption of alkyd varnish when applied is 50 - 75 g / m 2. The use of a means in a volume exceeding the recommended, automatically increases the lacquer drying period and makes the coating less durable.
A solvent for alkyd varnish is the White spirit. After applying an alkyd varnish, the solvent immediately begins to evaporate. After completing this process, active varnish polymerization processes are activated. This reaction occurs on the basis of the dual nature of chemical bonds in the resins molecules, which are part of the alkyd varnish. At the beginning of the reaction, the molecule is located in close proximity to each other. After evaporation of the solvent, the air of the environment (if more precisely, the oxygen molecules) penetrate the lacquer coating and are located between the resin molecules. With the help of oxygen, they begin to interact with each other, which leads to an increase in their size.
At first, the consistency of the lacquer film resembles glue, it will finally freeze only after 9 - 12 hours at a temperature of 18 - 20 0With and air humidity not less than 50%. The thickness of the lacquer coating can ultimately decrease, which depends on which mass part of the White spirit evaporates in the drying process.
The solvent content in different alkyd varnishes is not equally. Naturally, the means with a smaller consistency of White Spirit is less toxic.
What you need to remember, choosing varnish
Planning to give an outdoor coating a more noble type of own forces, you naturally buy lacquer yourself. We want to remind you of several important criteria for choosing this fund.
Clearly decide for what purpose you will use the room in which you will cover the floors. How intense will be the mechanical impact on the floors? Provided that there will be no more than 2-3 people in the room, it is better to give preference to lacquer, the basis for which water acts.
For processing kitchen floors or coating in the corridor, it is impossible to suit the color composition for a wooden coating: it will not only serve as a reliable protection against loads, but also will protect the floors from dirt. Familiarize yourself with information about the anhydrous polyurethane mixtures, which in the minimum deadlines are absorbed by wood and do not require special care.
For processing the floor covering of the office, a restaurant or cafe, where the load on the floor is maximum, do not pick up better impregnation on an oil base or a mixture with a water-repellent effect. These compositions for many years will retain an attractive type of wood.