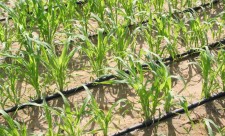
Arbolite blocks do it yourself Building materials
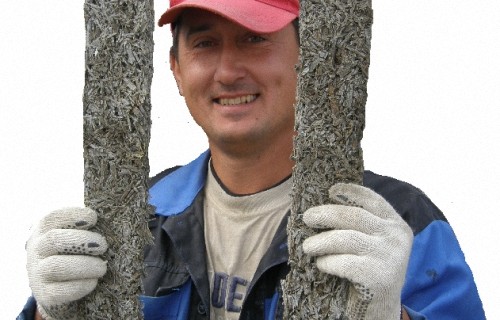
Arbolite blocks - lightweight building material for the walls of low-rise buildings. It is made of wood chips, sawdust, water, chemical reagents and cement.
Content
- Scope of application and classification of arbolite bricks
- Arbolite blocks, specifications
- Arbolite blocks, construction: advantages and disadvantages
- Equipment for the production of arbite blocks
- Production technology of arbite blocks and necessary materials
- Useful information about the process of manufacturing arbite blocks
Industrial Arbalite blocks have the form of parallelepipeds of the correct configuration. Made by pressing the mixture of chips and mortar using special equipment. This type of building materials is also known as a tree. Building material of this type is easily manufactured at home in the presence of necessary ingredients, equipment and performing technological requirements.
Scope of application and classification of arbolite bricks
Arbolite products refer to a group of light concrete. The scope of their application is determined by the density characteristic of this building material:
- For thermal insulance protection of the premises.
- For walls that do not experience a structural load.
- For the construction of utility buildings, economic attacks.
Arbolit is classified according to the density of dry material:
- On thermal insulation - with an indicator of density less than 500 kg / m 3.
- On the structural - with a density indicator of 500- 800 kg / m 3.
According to the mixtures used for filling, the arbolite from wood chips, rice straw, hemp, dried cotton, linen fiber is isolated.
Arbolite blocks, specifications
Technical indicators of the state of arbolite blocks and their dependence on other factors:
- Hardness - 0.35-3.5 MPA. This characteristic depends on the composition of the mixture, cement marks, the quality of sugar neutralization. It is defining to create a block of predetermined density and strength.
- Density - average value of 400-850 kg / m 3. The manufacture of arbite blocks assumes that this characteristic is regulated by a change in the proportions of cement and organic filler. The higher the average density rate, the stronger the product.
- Thermal conductivity - 0.07-0.17 W / (Mos). The larger the proportion of the binding materials used in the manufacture of the mixture, the higher this indicator. The low thermal conductivity indicator means the presence of high heat insulation properties in the product, and indicates the low strength of the blocks.
- Frost resistance - 25-50 cycles. This characteristic determines the maximum permissible reading of seasonal consecutive frost and thawing, which can withstand the building material, without being completely destroyed. Wall processing with plaster or other protective materials increases the indicator.
- Shrinkage - 4-5 mm / m or 0.4-0.5%. The indicator is directly dependent on the medium density of the material - the smaller the density, the higher the shrinkage.
- Water absorption - 45-80%. In comparison with the popular building materials - foam block, this indicator is higher, that is, the property of water repellence in arbolite is 3-4 times lower. Arbolite blocks need additional protective measures and processing with water-insulating drugs.
- Parry permeability - 0.19 mg / (m pa per). The high value of the indicator similar to the vapor permeability of natural wood.
- Sound permeability - 126-2000 Hz. The high value of the indicator, the arbum blocks practically do not need forced sound insulation.
- The maximum floors of the building from arbolite blocks is 2-3 floors with the corresponding weight of overlaps.
- The cost of this material is about 90 EUR per 1 m 3.
Arbolite blocks, construction: advantages and disadvantages
Arbolite blocks are a unique material that optimally combines a large spectrum of positive, useful characteristics with a small amount of deficiencies. The advantages of this building material are as follows:
- High resistance to bending loads, thanks to used in the manufacture of fillers. The main quality of the building material - protection of surfaces from cracking during oscillations and shrinkage.
- High aerobic and anaerobic properties. The material is not subject to rotting, does not create conditions for the development of fungus and mold.
- The process of manufacturing arbite blocks is environmentally friendly. The composition does not use carcinogenic organic ingredients. The finished brick during the period of operation does not emit harmful substances, not dust, does not cause allergic reactions.
- Fireproof material does not support combustion, has high resistance to high temperatures.
- Resistant to mechanical effects, shock strength, abrasion.
- High variability. Arbolite blocks, the size and shape of which are determined exclusively for fantasy, allow the production of building bricks according to individual parameters and specified dimensions for an exclusive structure.
- The material is well processed and securely holds the fasteners.
- Arbolite blocks have a low proportion. The ability to build buildings with a light foundation. To decorate internal and external surfaces from arbolit, any types of finishing materials are suitable.
- The plasticity of the block is preserved even after its complete drying. Shockoffing additional loads, the block is compressed up to 10% without prejudice to its internal structure.
- Low thermal conductivity of the material saves on the heating of the building.
The lack of arbite blocks has only one - a high level of water absorption. The only drawback is easily removed by applying a special protective coating.
Equipment for the production of arbite blocks
The technology of manufacturing arbite blocks requires an organization of a small plant with specific accommodation. Production of arbolite blocks, equipment of paramount importance:
- Slobal trap.
- Capacity for the mixture.
- Vibrosito.
- Falling table.
- Table shock-shaking.
- Inserts in shape.
- Detachable form.
- Metal pallet form.
- Installing vibration.
At home, arbolit is prepared from a specific mixture. The required size is obtained in special homemade glands. The form is made of conventional wooden boxes, frown from the inside with linoleum. The laying of arbolit in the form produce layers in 2-3, each layer is thoroughly tamped. The latter layer is not smoothed, but leave uneven, the distance to the edge of the sides is withstanding about 2 cm, it is filled with plastering solution. The recommended time to keep the block in the form is at least 24 hours.
For mass production, the machine is used for arbite blocks. The performance of such equipment reaches 50 blocks per hour, the cost of 120 EUR.
Production technology of arbite blocks and necessary materials
The composition of arbolit contains cement M400 / M500. To give high strength products, it is possible to use another brand. Filler for concrete serves small wood chips, a homogeneous chip, sawdust. The deficiency of any of the listed ingredients of filling is replaced by infirred materials: cheese, foliage, bark. The mandatory percentage proportion of the added substitute is maintained, it should not exceed 5% of the total mass of the main filling material.
The fractional size of fillers is monitored. Limit in thickness up to 5 mm, in length not more than 25 mm. The organic is pre-passed through a shotmett, crushed to the established size. The prepared mixture is mixed with cement mortar.
In the factory conditions, organic sugars neutralizers are necessarily added to the organic matter and waste of organic origin. Measure required for binding and removing sugar, adversely affecting the strength of the finished Arbolit. Common inhibitor - aluminum sulfate and calcium chloride.
Arbolit production at home eliminates the use of chemical reagents due to their deficit in free sale. Without the reaction of the splitting of the sugars, the prepared mixture begins to "wander", the gases are swept away the surface, forming emptiness and defects in the amount.
The ability to exclude a negative process exists. Waste from wood dry in a ventilated room or in an open space of 3.5-4 months. Under the influence of heat and convection, natural dried and evaporation of dissolved substances dissolved in water, including sucrose and their derivatives occur. In a dry tree, only fibers with low, permissible cellulose content remain.
The process of kneading the solution:
- Wood mass, organic filler is loaded into the crusher, are crushed to acceptable consistency.
- For complete neutralization of sugar, a fine wood mass is stirred with a dry cement and immersed in a 5% -10% lime solution. Hold up to 3 hours.
- Throw off the mass on the roar. Give a drain of the liquid.
- The viscous mass is poured by the need for water, stirred to homogeneity so that the pasty thick cashem turned out.
- Make the mixture taking into account the proportions of the main materials: on 4 parts of the water, 3 parts of the cement, 3 parts of the filler.
- The finished mixture is centrifuged in the concrete mixer until the lumps of lumps and clots.
- Check the mass for readiness. High-quality mixture crumbly. When compressed in the hand, it saves the form, does not break and is not deformed.
- The mixture is loaded into molding to frozen.
- Finished arbolic blocks are removed.
Construction from affordable material is carried out as the homemade brick substitute arrives. Properly organized and debugged process allows you to get up to 100 pieces per day when manually kneaded.
Useful information about the process of manufacturing arbite blocks
- The solution of wood and concrete is stirred in a conciseaker for high-quality closure of lumps.
- If the ready mass turned out to be viscous, and not crumbly, it is dried by a natural way, a quarter of the cement standards and a quarter of the filler rate are added.
- When sawdust and chips are withstanding outdoors, they need to be mixed from time to time with shovels. If this is impossible to do it, the mass is treated with calcium oxide. On 1 M. 3 Cheese in this case requires a 200 l 1.5% solution. The chips and saw-treated with a solution are left for 96 hours, stirring every 6-8 hours.
- To speed up the process of solidification of the mixture, dry chloride of calcium is added to it.
How to make yourself Arbolite blocks, video plot will tell in detail and intelligibly.