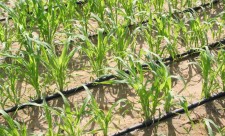
Characteristics and features of porcelain stoneware Building materials
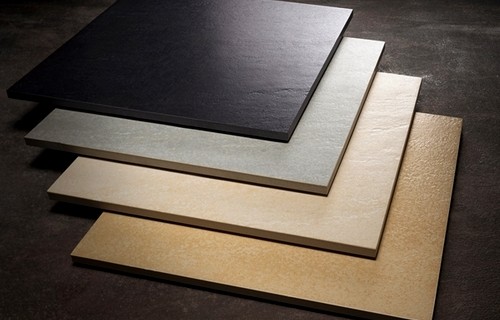
Tile porcelain tiles in his homeland, in Italy, is not known any other than Gres Porcellanato, which literally means "stone-porcelain ceramic". The characteristic most accurately reflects the essence of the material: it has similar features with porcelain, is identified by experts as a tile of single firing, and the appearance of the appearance is not inferior and even surpasses the beauty of natural stone.
Content
Features of production technology of porcelain
The mixture for the future "Gres of Porchelnato" includes several grades of clay, purified quartz sand, field spat and coloring pigments in the form of metal oxide, - components are extremely natural.
All components for the production of porcelain is mined in careers. The clay involved in the manufacture of material should be a strictly defined chemical composition: the main properties of the finished product depend on it. In the factory, each grade of clay is removed a separate container to mix with other components of the composition in a precisely calculated proportion. Then the mixture enters special mills, where it is crushed to the desired size. Mills are rotating large cone-shaped pipes, inside which are placed with spray mills from fastest stone rocks.
Next, the flashes are stored in special silos, each of which is intended only for its type of material. Future porcelain stored there before the next stage of production - pressing and firing.
When a computer system reports on the demand of one or another type of material, the raw materials are sent to the special process tower, where it is finally mixed with other types of kneading.
The resulting mixture is divided into strictly defined portions and sent to pressing. Before firing a tile, published from under the press, more than a nominal copy of several centimeters, as it remains up to 10% moisture. The working size of the product is formed during the firing.
Burn the tile in the oven at the highest temperature indicators that are only used in the production of ceramics - from 1200 to 1300 ° C. In the process of gradual injection of heat, the body of the tile is structured, forming a single homogeneous material, and it acquires those unique characteristics for which the porcelain stonewares value.
After the product is cooled, you can admire the result - a durable glazed tile that does not absorb moisture, ready!
Cerambulanite production technologies
Double loading - the method makes each tile unique, creating unusual divorce and unique shades on its surface.
Microtets - In the process of processing thoroughly crushed kneading, products decorated with drawings with small parts of the highest accuracy.
The method of "passing veins." The product that turns out as a result looks very effectively: the entire thickness of the porcelain is dressed with chaotic multicolored veins, which makes the material similar to the noble tile of natural marble.
Porcelain stoneware is a worthy alternative to the natural stone he is inferior in price, but at the same time surpasses it according to technical specifications.
Cerambar: Features for operation
- Strength.
In the thickness of the porcelain, there is practically no pore, which makes it phenomenally solid and durable material. The so-called concentrated load of the porcelain stoneware "holds" is 15-20 times better than cement, reinforced concrete and natural stone. However, if you do not comply with all the conditions of the correct laying, the porcelain stoneware can lose its wonderful strength. - Wear resistance.
Abrasion and porcelain stonewares are practically not compatible concepts. The color of the tile is identical throughout its thickness, so the mechanical deformation of the surface is not terrible, because they will not be seen. Porcelain stonewares are indispensable in public places with an intense flow of people. - Neatness.
Since clammograntitis is an unpaid material, it will never become a target for the eaten mud. Real ceramic granite is easy to wash - only its surface is polluted, it will not be able to penetrate deeply. - Frost resistance.
Water having a trend for freezing can become a catastrophe for porous tiles. The moisture falls into the pores, when cooling it freezes and pumps the tension inside the tile, making it more breaking. As a result, irreversible defects appear on the surface of the product: cracks and characteristic chips, which are only the first signs of complete destruction of the coating.
Cerambrants, as always, at the height. Moisture absorption indicators are impressive - just 0.05%! Even natural stone can not boast such a negligible low digurity. It is not surprising that the porrong tile is often used as an outdoor facing material - it will erase all the infancy of bad weather. - Fireproof and fire resistance.
Porcelain tile - a frequent "guest" in the furnaces and fireplaces. The material not only perfectly transfers the effect of heat, but also serves as a reliable protection against fire for the facing surface. This cerarmist of toxic substances during heating does not allocate. - Light resistance.
The scorching sunny rays have no destructive effect on the surface of the porcelain stoneware - even with a long service life, the material retains its original color. Do not spoil such a tile even "chemistry", since it is resistant to the action of acids and alkalis. The only substance, contact with which can end for porcelain stoneware, is hydrofluoric acid. - Antistaticity.
The material does not conduct an electric current. Its confidence can be called one hundred percent protection against the discharge of statistical electricity. - Attractive appearance
From what kind of pigments are mixed with the material for the production of porcelain, the color and texture of the finished product depends.
Porcelain stoneware with the so-called coloring "salt-pepper" is the easiest and affordable option. The tile, represented in the "Monocolor" color, is more expensive, since it does not do without pigments with a high content of rare-earth metals in its production.
Gres Porcellanato, imitating the natural pattern of natural stone, today is the most expensive view of the porcelain stoneware. To create it in a complex processing process, several pigments are mixed. However, the price is really justified by the quality and external attractiveness of the product. Performed in such a technique of porcelain stoneware in the photo below is a real confirmation. By the way, on the tile you can reproduce not only the drawing of the wild stone: technologists can be copied by even the pattern of oak parquet with a detailed structure of wood.
Varieties of ceramographic
According to the composition
Homogenic (fully painted) porcelain stoneware is the most popular thanks to its diversity. The production process of this type of material is called classic. At the preparatory stage, the entire mass of the tile is pigmeed, so the pattern remains the same on its surface and thicker. Such a "trick" gives the product a large durability: even after many years of operation, the working surface of the porcelain stoneware continues to look decent. This is explained by the fact that the abrasion of the surface layer does not affect the quality of the tile pattern.
Partially painted porcelain stoneware. The product tile consists of two layers: substrates and pigmented coating. The substrate is usually standard - "salt-pepper", color only a few millimeters of the surface layer. So you can avoid large expenses on expensive pigments and, accordingly, reduce the cost of the product.
Glazed porcelain tiles. Outwardly, it strongly resembles the usual tile: the product has the same layer of glaze on the substrate. The main difference is that porcelain stonewares are located as a carrier base for glaze, significantly extended operational period of such tiles.
In appearance
For different types of ceramic porcelain stoneware, depending on which the texture is obtained the surface of the tile in the production process.
Matt porcelain stoned after firing is not additionally processed, so its texture remains as it turned out in the walls of the roasting furnace. And although the surface of such a tile does not glorify, the strength of the product is extremely high.
Matte not painted porcelain stoneware with a raw surface and a thickness of more than 8 mm is called technical. From decorative models, it is distinguished by several other parameters: with a relatively small size (20x20, 30x30 cm), the thickness of the tile is increased from 12 to 30 mm (the standard thickness of the porcelain stoneware is 8-14 mm). In strength, technical porcelain stoneware is not inferior to the bulk sex, but, unlike the latter, he has a more aesthetic appearance.
Semi-polished and polished porcelain stonewares are distinguished by a mirror surface due to the processing of abrasive substances. However, for the external appeal, it is necessary to pay a decrease in wear resistance. In addition, care for this type of porcelain book requires a lot of effort: the surface of the coating must be regularly treated with special mastic, which creates a protective barrier from adverse environmental factors.
The upper layer of laptic porcelain stoneware is polished in part, which allows you to combine different areas on one tile on the texture. The alternation of polished and matte spots looks unusual and effectively, with all the internal quality of the material remain at the height. In addition, the laptic porcelain tile does not slide under his feet.
Satinized porcelain stonewares are created as follows: the surface of the tile immediately before sending it to the firing furnace, cooped with a layer of mineral salts, which gives the product a pleasant soft glitter. At the same time, high quality and all data for long-term operation in the porcelain stoneware of this species are saved.
In the technology of the production of structured porcelain stoneware, a wide range of all sorts of molds is used. So, the texture of the finished product may look like rock, tree or sand. In addition, special notches that prevent sliding can be applied to the surface of the structured tile.
Rectified porcelain stoneware is characterized by a perfectly smooth edge of tiles, which after firing is cut into diamond circles. After laying such a product on the surface of the porcelain coating, there is no single seam!
The tile of glazed porcelain stoneware in front of the firing is covered with enamel - glaze. The technology is relevant when ceramic granite tend to give absolute similarity with marble, travertines, wood or any other material without using an expensive method of through staining. As a coating in crowded places, the glazed porcelain is better not to choose - the glaze sooner or later erased.
Scope of application of ceramographic
The porcelain stoneware has perfectly proven itself as a facing material for finishing public buildings: the tile can often be seen in offices, business centers, hospitals and at railway stations. Porcelain stoneware for the facade gives the whole building strict, "touched" species, and a rich variety of colors and the texture of the product embodies all sorts of architectural solutions, despite the degree of their complexity.
Recently, private country houses and cottages are increasingly decorated with porcelain tiles.
Porcelain mosaic is a stylish and unique element for indoor indoor decoration. With it, it is possible to create spectacular and, most importantly, the only compositions of the composition that will not leave anyone indifferent.
TECHNICAL CERAMBERIANT WIND POLICE OF COMMERCIAL AND INDUSTRIAL ENTERPRISES. It is also ideal for finishing garages, car dealers, large stores.