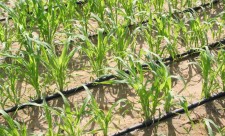
Ceramzite or Minvata, which is chosen as insulation Building materials
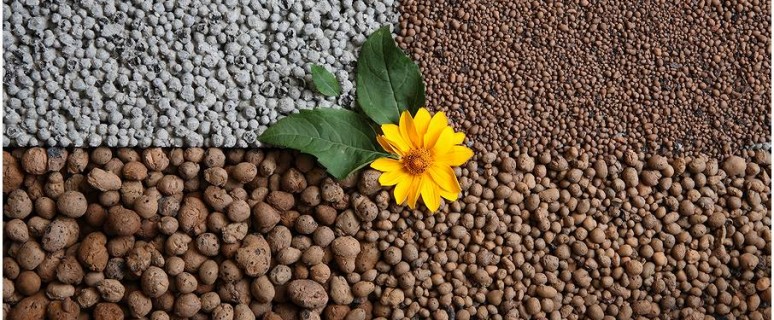
Whatever modern and powerful is the heating system, without high quality reliable thermal insulation, its effectiveness is minimized due to a large heat loss. Ceramzit and mineral wool are most often used for insulation of walls, roofs, gender or overlap of residential buildings. It is impossible to categorically assert which of the materials is better. Both heat-insulators have their own positive and negative sides. Their heat-freight function depends not only on the physico-technical indicators, but also on compliance with the rules of installation of thermal insulation.
Content
- General requirements for insulation
- What is a clay
- What are the types of clay
- Performance characteristics of ceramisita
- Physical and technical characteristics of clay
- Method for the production of ceramzit
- Where clamzit is used
- Floor insulation methods with clampsite
- Ceramzite floor insulation
- What is mineral wool
- Operational characteristics of Minvati
- Thermal insulation of the floor mineral wool on lags
- Insulation of the attic room of mineral wool
- Thermal insulation attic ceramzit
- So what is better: Minvata or Ceramzit?
General requirements for insulation
During the construction of buildings, the insulation of walls, overlappings and gender is carried out using insulation from special building materials - polystyrene foam, foam, ceramzite, mineral wool. They are distinguished by low thermal conductivity, light weight and low cost. The heat insulating materials also have a noise-protective effect. They must meet compulsory requirements: environmental safety and fire resistance.
What is a clay
Ceramzite - bulk, porous, fairly lightweight building material. The predominant difference in clamzit from other similar building materials is to use as the basis of special clay rocks with a container of about 30% of quartz.
Ceramzite is obtained by firing low-melting clay rocks that can quickly remove when heated to 1050-1300 ° C for 30-40 minutes. As a result of heat impact, rounded granules with a melted surface are formed.
It can be said that the ceramzite appeared due to the defective clay brick, when the sedimentary clay sediments are extended. The release of gas and the transition of the clay rock into the pyroplastic state during thermal processing and is taken as the basis of production of clay. Most often, the ceramzite is used to fill the concrete structures and thermal insulation of the foundation, overlap, roofing.
What are the types of clay
Depending on the magnitude and shape of the granules distinguish:
- Ceramzite gravel. The granules of the oblong form.
- Ceramzite crushed stone. Granules in the form of cubes with sharp corners.
- Ceramzite sand. Small granules, less than 5 mm.
The quality of the clamzite affects the size of the granules, bulk density, bulk weight, porosity, strength. The porosity of the ceramisite is of different structures, its insulation depends on it. The more pores, the higher the heat-saving function of the clay. Outside, the granules are usually brown, on the fault - black.
Depending on the magnitude of grains, the clamzite is divided into fractions. According to GOST 9757-90, the following clamp fractions are distinguished by: 5-10, 10-20 and 20-40 mm. Material with granules less than 5 mm refers to claying sand.
Performance characteristics of ceramisita
Thermal conductivity
High thermal insulation ability. The heat-saving properties of the material depend on the type of processing. Even a small claymzit layer under the floor significantly increases the level of thermal insulation. The heat shield of the ceramisitis layer is 100 mm thick is the same as 250 mm wooden.
The weight
Due to the lightness, the clay insulation is used at all stages of the building process. The weight of one cubic meter of the ceramisite reaches 250 kg.
Sound-proof
Ceramizite is characterized by a high degree of soundproof. The soundproof properties of the ceramisite are important in housing construction.
Strength and durability
Thanks to the "hardening", as a result of clay firing and the formation of a durable shell, the material becomes chemically inert, mechanically resistant to mechanical damage and temperature effects (frost resistance, at least 25 cycles).
It is not subject to rotting, damage to rodents and affecting the fungus, mold.
Fruit
Keramzite fill the spaces of any volume and geometric shapes.
Environmental Safety
Ceramzit is completely natural. Does not contain toxic impurities.
Water resistance
Ceramzit is not susceptible to moisture. Water absorption of material is 8-20%. Any insulation needs to protect against moisture and vaporizolation. But even when moisture gets into a claymzite layer, its granules act as drainage, thanks to ventilated gaps. And moisture gradually evaporates.
Affordable price
The material has a relatively inexpensive cost. For example, one cubic meter of ceramzite gravel (fraction 10-20) can be bought for 1450 rubles, delivery price is 1500 rubles. Ceramzite is sold on the scatter, and packaged in bags.
Physical and technical characteristics of clay
Bulk density
Cerazytite is assigned different stamps depending on the magnitude of the bulk mass. The total number of ceramic grades varies from 250 to 800, the number of brand indicates the bulk density of the material.
For example, clay gravel 250, has a bulk density of 250 kg / m3. Analysis on the determination of a bulk density of fractions is carried out by filling the clause in dimensional containers. The smaller the granules, the greater the bulk density.
Moisture absorption
This indicator expresses the percentage of the weight of the dry filler. Unlike other fillers, the ceramzite is protected from moisture penetration inward due to the presence of burnt crust. The correlation coefficient of high-quality ceramisite is not lower than 0.46. The defective material has a low porosity of the granules, which significantly increases the ability to absorb and hold the humidity.
The ability to deformation
The deformation coefficient is determined by the porous structure of the material. As a rule, after the first test cycle, the overwhelming majority of material samples shows a reliable result of shrinkage. The permissible value of the deformation coefficient is not more than 0.14 mm / m.
Thermal conductivity
On the heat insulation properties of the ceramisitis, the vitreous phase of production has a great influence. The greater the glass content, the lower the thermal conductivity of the material. Ceramizite of good quality has a thermal conductivity indicator of 0.07-0.16 W / m, which allows to save up to 80% of heat.
Method for the production of ceramzit
The clay slate is burned in metal furnaces in the form of drums with a diameter of 2-5 m and up to 70 m long. The drums are located at an angle of inclination. Shale granules pour into the upper part of the furnace, they come down the drum, where the fuel burning is located. The burning time of the granules in the furnace is 45 minutes.
There are two-drum furnaces, in them the drums are separated by the threshold and rotate at different speeds. In such furnaces, less high-quality raw materials can be recycled and obtaining clay crushed stone or gravel at the exit, not inferior to the material obtained in single-drum furnaces.
Where clamzit is used
- Economical bulk insulation for walls, floors, building floors, basements, shelling of a shell type, as well as for the arrangement of heat and water supply networks. Ceramzite gravel of good quality reduces the heat loss of the building by 70-80%.
- Filler for light concrete (ceramzite concrete). Production of ceramzite concrete blocks.
- Decorative material and at the same time thermal insulator for soil and lawns.
- Drainage material and heat insulator for earth road mounds in the places of water saturated soil.
Floor insulation methods with clampsite
In modern construction there are different ways of the draft floor. One of the frequently used is a clamping of the floor with a clay, which is performed both dry and wet.
Wet way
The use of claympsite as a filler for a concrete solution gives the strength of the structure. As a result of the penetration of the solution into the porous structure of the granules, the force of concrete clutch increases.
Cement and construction sand - 1: 2 or 1: 3. In the first case, it turns out a durable solid surface capable of withstanding large loads. Water add so much to get quite thick homogeneous mass. There are ready-made sandy cement formulations on sale, which are bred by water in accordance with the instructions.
How to calculate the consumption of clay
The calculation of the clamping of the floor screed is carried out taking into account the required thickness of the heat insulating layer. Before you buy clamzit and other materials for a screed, you need to calculate their quantity.
Usually follow the following proportion: at 1Qm. We will require a thickness of 30 mm thick 17 kg of cement and 50 kg of sand. The flow rate depends on the thickness of the insulation layer and the material fraction and is about one bag of 50 kg, which is sufficient for the device of a screed area of \u200b\u200b4-5 m2.
Calculation of ceramisite for a warm floor
The use of clay allows you to more economically spend the concrete solution. Laying of the "warm floor" has its own characteristics, since the concrete-clay coating is experiencing not only mechanical loads, but also temperature effects. In this case, the proportional content of cement and sand will be 1: 2.
The amount of clayzite depends on the thickness of the heat insulation layer, for example, with a layer thickness of 10 mm, 0.01 m3 of material is 1 m2. It is difficult to calculate the accurate consumption of claying, often the required amount of material is determined by the experimental way in the construction work process. A plasticizer was added to the concrete mixture for the "warm floor" at the rate of 150-200 ml per 1 m2.
The order of laying ceramzita
The thermal insulation with clay requires a clear compliance with technology.
The procedure for insulation by clay:
- Clear floor. If the floor is made, then remove all the designs with the exception of fastening beams.
- Estate lighthouses around the perimeter of the room, withsting a small clearance from the wall.
- Fill the surface of the sand layer with a thickness of 100 mm and tamper.
- On top of the sand layer to fall asleep clamzit. The minimum thickness of the claying layer should be at least 150 mm. It is determined taking into account the load on the floor.
- Align the surface of the ceramic layer on beacons with a fishing line.
- Covered with waterproofing film to protect the clay insulation from moisture penetration.
- Pour concrete solution. Laying concrete requires accuracy to not disrupt the level of clay. For 3-4 weeks, the floor is regularly wetted with water to avoid cracking.
Dry fashion
The feature of the technology of the dry screed is that the concrete mixture is not used. The design consumption of clay is 0.01 m3 per square meter of the floor with a layer thickness of 10 mm. However, the calculation of the ceramizite for a dry screed is made on the thickness of the layer 30-40 mm, which means that 1 m2 of the area will be required at least 0.03-0.04 m3 of the material.
In practice, the consumption of clay can be somewhat different from the estimated domestic reasons: the slope of the floor, changing the area of \u200b\u200bthe screed after the installation of beacons, etc.
Ceramzite floor insulation
Country house can be insulated with clay. The insulation layer should be at least 30 cm. When laying a claygery directly to the ground, the floor will be cold. More efficient method of double floor flooring. On the beams attached a draft floor from densely fitted, without boats of boards. The flooring is covered with fine durable paper - pergamin, which is used instead of toly. From above to the level of the middle of the beam, clamzit is poured. Then the purple floor is stacked.
Heaters requires protection against moisture formed both inside the house and penetrating the external environment. This uses waterproofing membranes.
What is mineral wool
Mineral wool is one of the most common heat insulators, which has been used in various types of insulation. Mineral wool - soft large-fiber building material. The mineral wool insulation from metal waste and carbon alloys of minerals is produced.
Mineral wool is widely in demand in construction, due to durability, simple and rapid installation, fire resistance. The disadvantage of this insulation is reduced moisture resistance. To protect against dampness, the material is impregnated with special compositions.
This property of mineral wool as air permeability is especially valued. Thanks to the ability to "breathe", mineral wool is often used to insulate wooden houses. The form of the release of the mineral wool insulation: plates, rolls, mats of various lengths and thickness. The selection of the size of the plates depends on the conditions of thermal insulation mounting and upcoming tasks.
For summer houses, the dimensions of the insulation will be smaller. So for a panel cottage house, 50 mm thick sheets will be required. Houses of year-round residence need more thorough insulation, in this case the required thickness of the mineral wool layer reaches 200 mm.
Operational characteristics of Minvati
- Mineral wool is a refractory material.
- Provides a high degree of sound insulation, which is especially relevant in residential buildings with thin walls.
- Not exposed to deformation from exposure to high and low temperatures.
- Acceptable price. The cost of the material depends on the form of release and sizes. For example, a set of mineral wool in fiberglass-based rolls for heat and sound insulation of various designs of two matte size 8200x1220x50 mm costs 1 375.00 rub.
Disadvantages of the mineral-cotton insulation: the material is continuing and non-tech. Minvatu can not be called an eco-friendly insulation. Its particles when entering the respiratory organs have a harmful effect on the human body.
These disadvantages are neutralized with the proper handling of the material and compliance with the technology of thermal insulation installation.
Thermal insulation of the floor mineral wool on lags
One of the ways of thermal insulation of the floor is label laying.
Floor insulation on lags is produced on the ground. The underground space with this method will be cold. If the house is brick, then it is necessary to warm the foundation of the house. This is caused by the large thermal conductivity of the brick and the possibility of forming cold bridges. The heat insulation in the lagham method is more often carried out in wooden houses, as the tree has less thermal conductivity.
Modern insulating materials are very effective. But sometimes their use leads to the freezing of the base and in wooden buildings. Such an opposite effect is associated with the high tightness of modern heat insulators and an obstacle to the heating of the underground space due to the heat of the house. Therefore, with the insulation of a wooden house with modern materials, heat insulation of the base is also required.
The procedure for insulation of sex by lags
- Dumping soil.
- Laying a layer of rubble, bonded by bitumen mastic. Bitumen is used for waterproofing.
- Installing brick columns with a longitudinal interval of 2 m and transverse - 60 cm.
- Waterproofing of columns.
- Laying wooden lag with a cross section of 100x50 mm, which is enough to keep the load on the floor.
- Fixing the windproof layer at the bottom of each lag. First, the metal grid is fixed, and it is a wind-protective film. It is necessary that the insulation layer does not flush under the action of air flow under the floor of the house. This film permeable film.
- Laying the mineral wool insulation on film between lags. Mineral plates with windscreen coating are now produced. In this case, the metal mesh and film is not required.
- Coating the insulation layer of vaporizolation.
- Sealing junctions between sheets.
- Floor flooring from the board.
If the floor is wooden on a concrete base, then the boards are removed and everything that is under them and purify the concrete surface. If the boards are in good condition and it is planned to re-lay after insulation, then the order of their location is noted and carefully removed.
Then they spread the waterproofing film. From above laid in a section of 50x50 mm at a distance of 50 cm from each other. There are insulation between lags. From above is fastened with small slats laid marching vapor insulation film. Finishing Stage: Flooring flooring.
With the insulation of the floor of the Minvata, it should be borne in mind that the height of the floor will rise by approximately 50 mm.
Insulation of the attic room of mineral wool
So that the attic is not empty, it can be insulated and turning into an additional attic room or storage room. For thermal insulation of the attic room apply:
- Organic derivatives (polyurethane foam).
- Mineral wool materials.
- Funny dry insulation (ceramzite).
For high-quality thermal insulation, the attic is used and combined all three types of materials.
Mineral wool is well suited for insulation of all surfaces attic: gender, walls and roofs. Insulation The attic of the Minvata requires additional use of the outer wind and hydro-insulating polymer film. The metal surface of the roof is desirable to treat oil paint to prevent the appearance of condensate in the cold season of the year.
Minvata has a loose structure, the pairs misses well, therefore, from the inside, the insulation is covered with a vapor barrier layer of foil polyethylene.
Mineral wool is used in the form of rolls and mats. The seams between the individual fragments of the insulation are carefully sealed with a metallized adhesive tape.
Mineral wool is placed between roofing rafters, and on the floor - between lags of carrier structures. With thermal insulation works, it is very important to take into account the load gain on the reference poles due to the weight of the insulation.
Therefore, before the start of insulation events in the attic room, you should make sure the strength of the supporting structures and the roof itself, and, if necessary, replace obsolete worn items.
Thermal insulation attic ceramzit
Ceramzite is an excellent material for insulation of the attic room. A dry loose claymzite layer creates a well-ventilated space and at the same time holds heat. Ceramzite is usually used to insulate the attic floor, and in some cases for the thermal insulation of the frontones and the roof itself.
The loose claymzit layer misses moisture well and the air, and therefore the outside the wind and moisture protection polymer layer are necessary. It is recommended to leave a small ventilated gap between the roof and the claying layer to exit moisture vapors.
From the inside the clay layer needs vaporizolation protection. Failure of the clamzite is made in a special framework. It grows part of the space inside the attic room. On the floor make a special box, clamzit poured into it, and the wooden or tiled flooring is placed on top.
Often, thermal insulation with a clamzite is complemented by minvata or polyurethane foam, especially in the pipe area, where ventilation is most required. In these places, clamzit falls asleep and is carefully closed from all sides by moisture and windproof membranes.
So what is better: Minvata or Ceramzit?
The thermal insulation of buildings of mineral wool and clay is considered the most common thanks to several factors: a relatively inexpensive price, a fairly simple installation process and a very decent quality of insulation.
The choice of one or another insulation depends on the specific conditions for construction, financial and technical capabilities. In addition, the ceramzite and minvat are perfectly complemented by each other and are often used in the combined version. Ceramzit and mineral wool are materials tested and have become traditional in construction. And it seems, in the foreseeable future are not going to give up their positions.