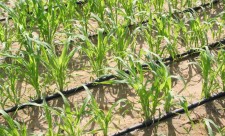
Removable Formwork Mounting Technology Construction
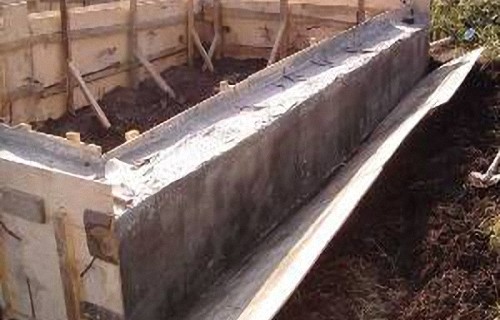
Formwork is used to fill monolithic structures. It happens removable and non-removable. A non-removable formwork is easier to install, but has a number of negative moments. One of the most fundamental is the residual elements in the foundation or wall. Over time, they begin to rot and destroy the monolithic design. Therefore, today the question of how to make a removable formwork is relevant.
Content
Varieties of removable formwork
The production of removable formwork is carried out both industrial enterprises and small building brigades. For private construction, removable formwork is applied with their own hands. But first needed to determine the source materials. It happens:
- from chipboard
- from plywood,
- from plastic,
- from boards.
Any of these species has the same design. The formwork consists of:
- shield
- skewing frame
- retaining beams.
Removable formwork for monolithic construction is also divided by types of work for which:
- foundation
- walls
- overlaps.
Although the design in each of the options will have the same set of elements, installation technologies are noticeably different. Therefore, for each type of work its formwork is made.
Installation of formwork for foundation
Removable formwork for the foundation is done the easiest. To do this, you will need:
- wooden boards 0.2х50 cm,
- 5x5 cm beams.
If you find a board with a width of 50 cm will not work, you can dial from several narrower cloths. Too thick boards are not recommended, as it is taking the design. As a result, you will need more support beams.
We proceed to the construction of the formwork. At the first stage, we make a shield. Depending on the size of the foundation, we determine its height. The top edges of the shield should be 5 cm higher than the foundation. In the length of the shield is made from 40 to 60 cm. Too long shields are difficult to fix. Note that the formwork should clearly form the boundaries of the foundation. Therefore, the length of the shield is formed on the basis of the size of the foundation. Installation of a shield:
- sprinkle the canvas desired long,
- dial the height of the shield with several canvases,
- connect the cloth with the outside beams,
- beams install perpendicular to the canvas and fasten with screws.
Operation to repeat before reaching the desired number of shields. Important, formwork is installed on both sides, the shields are made immediately on both. If time allows you to save and make shields only for one side of the foundation. Choose longer. Thus, the fill occurs gradually. But if you ordered a machine with a filling basis, the formwork must be installed throughout the perimeter.
Next, the shield is associated with a skeletal skeleton. For this you need:
- prepare 5x5 cm beams
- attach them with self-draws parallel to the canvas.
Make two belts. The lower, at an altitude of 10 cm from the ground, serves as the main focus and does not allow to spread the fill base. Upper is the basis for the backups. Made at an altitude of 40 cm from the ground.
The backups rest in the upper belt and are installed at an angle. They reliably prevent the discrepancy of the formwork. They are installed for 2-3 pcs, on the shield, depending on the thickness of the foundation.
Construction of walls with removable formwork
Monolithic construction technologies are actively developing. Build a house from a removable formwork and slag concrete quickly, cheaply and does not require compliance with complex standards. When performing this work, it is important to correctly make a removable formwork for walls.
Walls, in contrast to the foundation, must be as smooth as possible. Therefore, gaining a shield for it is impossible. From solo materials, experts recommend:
- plastic,
- laminated chipboard.
Chipboard is very reliable and practical material with which it is easy and convenient to work. The sheet can be cut on comfortable pieces, from which shields will be formed. The use of such a structure will save on line with materials, but will not give perfectly smooth walls. In places connecting shields there will be small influx of the filling base. These flaws are hiding with decorative plaster or "fur coats".
Installation of the formwork is made in the same way as in the case of the foundation.
If you plan to make walls under painting, then choose for removable plastic formwork. This technology allows you to seamlessly pour any surface size. Plastic formworks are produced in an industrial way and cost enough. In order to make them at home, you will need:
- set plastic panels,
- P-shaped profile
- wooden beams 5x5 cm.
To work, use a 4-meter profile. Even if the height of the walls will be less than 3 meters, profile trimming will go to the skew frame. The profile is installed every 30 cm. In order to determine how much it is necessary: length of the wall in meters divide by 0.3.
Further, on the inside, we recruit plastic on the profile. In the hidden part, you screw the panel with screws to the profile. When you fix the next plate, it hides the screw. As a result, a seamless connection is obtained. If the length of the wall is more than 6 m, then the panels are fixed into the scatter. This avoids the seam in the places of compounds.
From the outside, the horizontal profile binds to each other perpendicularly. For this you will need trimming. Their edges are bend in such a way that the resulting bending is convenient to fasten to the carrier profile. The firming belt is made at a height of 10 cm from the ground, and then each 50 cm.
At an altitude of 40 cm from the top level of the formwork, the reference beam is fixed. It puts in the strut and supports the design. The beams must be installed every 30 cm. Sometimes beams are replaced with tie screws, it simplifies the design, but is at the heart isolation. After removing the screw, the cavity is formed, which actively destroys the wall.
A wall made of concrete or slag concrete should be completely completely completely. Partial performance of work is not allowed, as it is significantly reduced operational characteristics. To save the walls poured in turn.
Construction of floors with removable formwork
In monolithic construction use two types of overlaps:
- reinforced concrete slabs
- bulk structures.
The use of plates requires the attraction of special heavy machinery. Therefore, the removable formwork of overlaps is used. This design should be as reliable as possible, but at the same time easy. To do this, need:
- plywood thickness of at least 6 mm,
- 5x5 cm beams,
- 10x10 cm beams or metal columns.
Plywood is only slightly inferior to the chipboard in strength, but it is much easier. In contrast to the tree, on the removable formwork from plywood there will be no big seams through which the filling base swells. In addition, it is not necessary to make reverse shields for filling overlaps.
Formwork Installation Technology:
- make from beams 5x5 cm Frame around the perimeter of the first floor, the top edge of the beam should be at the beginning of the overlap level,
- attach to the 5x5 cm beam frame so that the basis for plywood,
- with the help of beams 10x10 cm, set supports, at a distance of 2 m from each other,
- post plywood sheets and cut off shields
- install Phaneur on the frame.
Metal profiles are found in the wall, which holds overlap. Therefore, you do not need to make boards for fill. It is important that the overlap is well renounce. If the construction of a two or more storey house is supposed, then the metal must perform 10 cm beyond the walls. It will serve as a basis for installing the crate on the following floors.