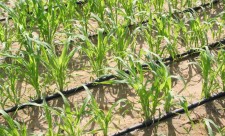
CHINAL CEMENT. Characteristics and application Building materials
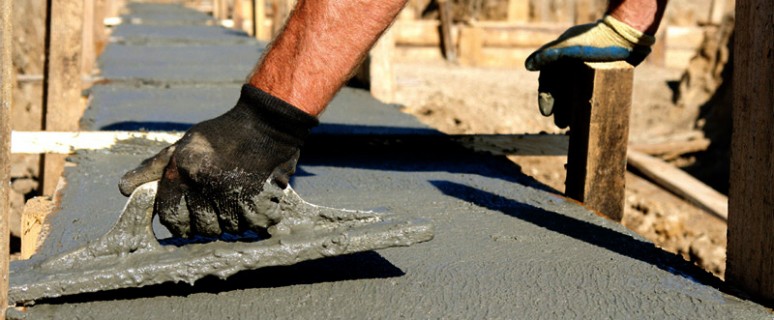
Hinlace cement is a hydraulic high-speed mixture that is characterized by the ability of rapid solidification in the air and aquatic environment. The material is obtained by the technology of grinding the burned raw material enriched with alumina. Primary raw materials for the manufacture of clay cement - limestone, boxcides or rocks containing aluminum oxides. Due to this, the mixture was received by the second name - aluminate cement.
Content
Marking
According to GOST 969-91, there are three types of aluminate cement, which differ in compression resistance:
- Hz-60 alumina cement.
- Hz-50 alumina cement.
- Hill-grade cement Hz-40.
The leading producers of alumina cement today are: SECAR, GORKAL, CIMSA ICIDAC, Ciment Fondu.
Composition of alumina cement
The main component of the composition is the low-main one calcium aluminate SAO-A1 2O 3which, when hardening becomes a two-killy hydroalum. The clamp cement is divided into high-known, containing CAO over 40%, and a little-known, in which the CAO is below 40%.
Glazymatic cement, composition of chemical elements:
- Aluminum oxide - 30-50%.
- Calcium oxide - 35-45%.
- Silicon oxide -5-15%.
- Iron oxide - 5-15%.
The mixture also contains a twocalcium silicate for slow screwdock, aluminates and ballast impurity - gelity.
Properties of alumina cement
- The binding properties of the material and its high strength after hardening are due to the presence of calcium in aluminates. The process of rejection of the aluminate cement proceeds similarly to Portland cement. And unlike the PC, the action is associated with abundant heat release. In the first day, the screwdrive is released to 70% of heat, which is a danger. If the temperature of the medium rises above 30 ° C, the cement stability will decrease by 2-3 times.
- In comparison with Portland cement, the alumina cement forms a more dense artificial stone, it has higher strength and high resistance to the aggressive environment. But it is easily deformed under the influence of an alkaline medium and it should not be mixed with lime, PC and plaster to eliminate the reduction of hardening.
- The period began to harde the alumina cement is at least 30 minutes, and the end of the process occurs after 12 hours. The grasp period is similar to Portland cement, but the chicken strength of the alumina cement is already manifested after 72 hours, while the PC is gaining strength only after 28 days.
Special properties of alumina cement
- the possibility of using alumina cement in winter conditions, due to the high heat generation indicator;
- resistance to the effects of aggressive liquids and gaseous media;
- quick strengthening of the mass after hardening;
- artificial stone of high density;
- Thermal stability for refractory cement.
Scope of alumina cement
- Updating damaged bridge structures.
- Glazymatic cement finds use in high-speed construction, when the desired stability of the design should be formed in the first 72 hours.
- The construction of structures where an increased coefficient of sulphate resistance is necessary.
- Fixation of anchor bolts.
- Insulation of oil wells intervals.
- Elimination of scaffolding and deformations in maritime courts.
- Isolation of breaks in the breed with abundant water consumption.
- To accelerate the rejection of concrete on construction sites.
- Production of tanks that are influenced by the aggressive environment during operation.
- Production of refractory concrete with temperature characteristics up to 1700 ° C.
Waterproof plaster
The use of aluminate cement in the manufacture of waterproofing plaster:
- In the construction of industrial facilities, the waterproofing plaster is used to close the cracks of the plumbing lines, under a working pressure of 10 atm. As well as for the production of tanks intended for storing liquid fuel.
- In the structure of the metro, the use of plaster provides waterproofing of the walls of underground corridors, sealing seams between tunnels, restoration of outdated structures.
- In the field of public utilities, plaster is used to seal the joints of pipelines, for waterproof coatings of sewage stations, repair of pools and shower facilities.
Almighty cement in home construction
Cement is alumina with its properties and characteristics, not only for industrial construction, but also for home appliances. For its competent use, it is necessary to take into account the features of the chemical composition of the material and its properties.
Preparation of aluminate cement
If the weight of the material is specified on the bag with an alumina cement, then it is fed to the concrete mixer immediately from the bag. In the case of the use of cement, which was stored in bags for some time, it may be necessary to pre-break the mixture. For this purpose, cement stirring in vibrational sieve is permissible using a construction vane auger.
Concrete solutions
The alumina cement has a higher viscosity in comparison with Portland cement. This requires a longer mixing of a concrete test, unlike the substance to the PC. The duration of the stirring is established by an experimental way for each specific case. And the duration of this process affects the homogeneity and stability of the material.
Stirring the aluminate cement occupies an average of 2-3 hours, after which the concrete mixer must be rinsed thoroughly. It must be done immediately, because for this time segment there is a grasp of the excess concrete. As a result, purification will be very trouble.
Actions with concrete in winter
The process of conducting construction work using a holled-grade expanding cement in the winter months has a number of features. Such work differ from similar actions with portland cement, due to the high exothermia of the aluminate cement. In the process of hydration of cement mixture, exothermic reactions with abundant heat generation occur. The temperature of the cement dough can reach 100 ° C. This phenomenon depends on the percentage of water in the total cement mass.
The temperature of the concrete substance on the alumina cement at the time of laying should not exceed 15 ° C. This can trigger the rapid frozen of the concrete mix with the further process of frozen the concrete test.