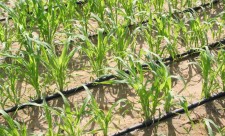
How to knead the cement Useful advice
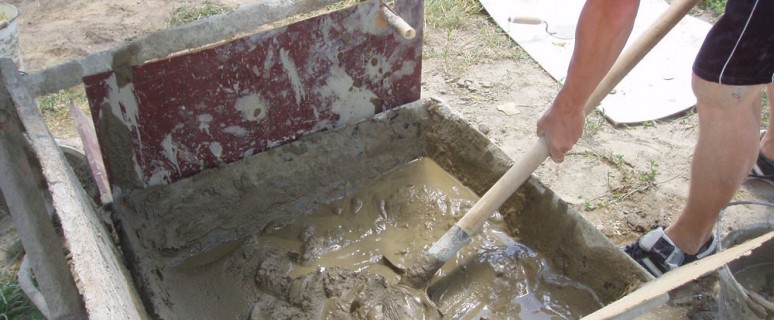
Concrete is the main material, without which no construction object is impossible, starting with the repair of the apartment and ending with the construction of factory buildings.
Content
- What is cement
- What are cement brands
- The most common cement designations
- How to knead the mortar from cement
- How to prepare a cement solution for the construction of the foundation
- How to knead the cement mortar for brick or masonry
- How to prepare a small amount of cement mortar at home
- How to prepare a cement solution for a tie
- What should be the consistency of concrete
- Safety regulations when working with cement
- Who is the most important on construction site
The cognizations of concrete are determined by its composition, the ratio of the amount of components, the method of kneading. It would seem that it is special here - to knead the cement mortar: I was flooded, mixed and finished! However, not so simple. In this matter, also has its own rules, the observance of which will allow not only to get high-quality material, but also to save strength and time.
What is cement
Cement is obtained as a result of crushing limestone, clay and additives. As an additive uses plaster, clinker or other material capable of sticking when mixed with water. These are the basic components of cement. There are also optional additives that give distinctive properties to different cement brands.
What are cement brands
On packing with cement there are notation, for example: M300, M500, M500 D0.
The assignment of the cement brand is carried out by laboratory testing of material samples for strength. Rectangular billets from cement-sand mixture and water after hardening are exposed to bending and compression.
Marking "M" - Characteristics of the sample strength for compression. Cement cubes are placed under the press and gradually compress until complete destruction. The tensile strength limit is calculated as the arithmetic average of 4 samples with the best indicators from 6 taken.
Thus, the M500 brand indicates the ability of cement to withstand the load of 500 kg / cm 3, Cement M400 - Load 400 kg / cm 3 etc. The maximum durable cement grades M600 and M700, mainly used in military construction.
Marking in the form of the letter "D" characterizes the percentage of optional additives relative to the clean clinker in the cement batch.
Thanks to the additives, the cement acquires additional specific properties: frost resistance, hydrophobicity, rapid solidification, resistance to salted water and corrosion. The designation M500 D20 suggests that in this batch of cement contains 20% of additives. And M400D0 marking means that optional supplements are missing. The group of slag cements is distinguished, the other name is SlagoporTlandcement, the content of additives in which more than 20%. There are additional abbreviations, for example, M500-D20-SS. The last two letters indicate the properties of cement attached to it additives.
The most common cement designations
- PC is an ordinary portland cement.
- The SPC is a slagoportland cement with a content of more than 20% supplements compared with the clinker component.
- BC - white cement for decoration.
- WRC - waterproof expanding cement. Used to seal seams in hydraulic structures. It has a rapid setting (4-10 minutes).
- N - normalized cement. Contains a clinker of a strictly normalized composition.
- PL - plasticized cement with high frost resistance.
- GF - hydrophobic cement. For 5 minutes, water does not absorb water, it is convenient for transportation, characterized by good plasticity and frost resistance.
- CC - sulfate-resistant cement. It is used for the construction of hydraulic structures under conditions of an aggressive water-salt medium containing sulfate compounds.
- B - fast-hardening cement. Used to perform urgent repairs.
How to knead the mortar from cement
To qualitatively knead the cement, first of all, you need to decide on its recipe: what components, in what proportions apply. The composition and ratio of the components of the cement mortar depend on the type of construction work and climatic conditions of the area. The technology of the cement mortar with a positive and negative temperature has differences.
When making concrete, cement marking, sand type and water quality.
Failure to comply with the rules of the formulation and kneading is fraught with the formation of cracks on the walls and brickwork.
How to choose the right components for cement mortar
Recently, many types of cement mixtures have appeared with various fillers to enhance a function of concrete: mechanical strength, thermal insulation, sound insulation, waterproofing. Basic materials of the concrete solution remain cement, sand and water.
There are various grades of cement: M100, M200, M300 and others. The higher the figure, the more sand is required when mixing the concrete solution. For example, for the manufacture of concrete from cement M100, the ratio of cement and sand 1/1 will be required, and for the M400 - ¼ brand.
What sand to choose for cement mortar
To obtain a smooth beautiful seam with facial laying, it is better to use river or career sand without clay, sowed from garbage and stones. The clay is badly mixed with the cement and when the laying seam falls outside the hole forms a hole. For laying under the plaster you can add to the solution of any sand. Clean sand is more white, and with clay - yellow.
What water can be used for a cement mortar
During the construction of serious construction objects and supporting structures, it is not recommended to use rainwater and water with oil content for mixing cement. In domestic conditions and small construction, cement mortar makes from any water.
Preparation of materials for mixing cement mortar
To get a high-quality cement solution, it is important to properly prepare the starting materials. Preparatory activities include:
- Pre-flushing rubble for cleaning from pouring dirt and garbage.
- Careful sifting and if possible, washing the sand to remove stones, clay and dust.
How to prepare a ballast for cement mortar
Before mixing the cement mortar, gravel and sand is sieved to exclude foreign impurities and sort the components in magnitude. Crushed stone passes three times through a sieve with cells of different magnitude. First - 20x20 mm, then - 10x10 mm, and for the third time - 5 mm. The screening of 20-40 mm value refers to the first fraction. The second fraction is a grain of 10-20 mm. Third - 6-10 mm.
For the preparation of cement mortar, 30% of the ballast of each fraction is used and mixed thoroughly.
Non-compliance with the proportions of cement mortar components negatively affects the quality of concrete. With a lack of cement, strength, frost and moisture resistance decrease. Excess water leads to corrosion of reinforcement inside the concrete structure. If the water is not enough, the plasticity of the solution deteriorates, which makes it difficult to work with it and will require additional compaction of concrete. The optimal is considered to be water consumption per 1 cubic meter of concrete 150-170 liters.
What are the methods of the cement mortar
After preparing the components, it is embarrassed.
Apply 2 methods of kneading: with the help of concrete mixer and manually.
Mechanized method
The advantages of using concrete mixers are obvious: mixing the cement solution is faster and physically much easier.
Especially justified the use of concrete mixers for large building volumes. It is absolutely optionally to buy a concrete mixer, it can be rented. In addition to the aggregate itself, the bucket and the Soviet shovel will be needed. The machine is worst concrete itself, only compliance with the mixing sequence is required.
Procedure:
- The slope of the concrete mixture bowl is installed at an angle of 45 degrees.
- First, water is poured into the concrete mixer. The volume of water is taken taking into account the amount of cement. For 1 cement bucket approximately as much water. Water is added gradually as mixed. The amount of water also depends on the weather. In the rain - less water, in the heat - more.
- Then poured half the standing norm.
- Then the entire cement is added, for 2-3 minutes everything is stirred and the remaining sand is poured.
- The desired consistency of the mixture is adjusted, adding water slowly and mixing for 3-5 minutes.
manual mode
A small amount of concrete can be kneaded by hand. This will require: a trough, bucket and shovel. Conveniently kneading cement slurry on a sheet of vinyl or linoleum extensions for advertising.
two kinds of manual mixing is used in construction practice.
Variant № 1.
The trough is poured already calculated the amount of water and add a measured amount of cement. Stir. Obtained slurry mixture. Such a method is convenient in that the solution is easy to stir until complete disappearance of cement lumps. Then poured predetermined amount of sand and mixed well until homogenous.
Variant № 2.
The capacity of sand and cement is poured in preset proportions and thoroughly mixed with a shovel.
In the center of the dry mixture make a slight indentation in the form of a funnel, which is poured into a metered portion of the water is less than the calculated amount.
Slurry is stirred from the edges to the center of the funnel shovel, moving the ballast dry cement mixture and combining it with water. To obtain a homogeneous concrete, it is important with stirring to reach the vessel bottom. This batch requires considerable physical effort, it is used in cases where it is not known how many parts need water to desired consistency of cement mortar. If the measure required amount of water, then the following portions of the cement slurry lighter kneaded, the first method.
For elastic mixture into water was added 50-100 ml of detergent or soap. Mixing the cement slurry at temperatures below zero has its own characteristics. Under such conditions, it is recommended to add a special FROST mixture potash.
With any method of mixing, manual or mechanized, the quality of concrete depends on keeping the proportions of all the components and sequence of technological operations.
How to prepare a cement mortar for the construction of the foundation
Concrete grout foundation kneaded as follows:
Materials and their proportions
- cement M500 - 1 part
- sand - 3 parts
- 4 parts of gravel,
- water - 1 part.
For example, one of the - one bucket.
- Step 1. Pour into a wide vessel 2 buckets of water. Depending on the degree of humidity of the sand may have further refill water.
- Step2. Absorb to 2 cement water bucket (without top). The bag 50 is placed 4 kg of cement bucket.
- When cement filling mixture is continuously stirred until a homogeneous slurry.
- Step3. Continuing to mix, fall asleep 6 sand buckets and bring the mixture to a homogeneous consistency.
- Step4. Fall asleep in cement-sandy solution 8 buckets of rubble.
To facilitate work, rubble should be evenly scattered throughout the capacity in which it is made. The resulting concrete solution is stirred after each bucket of the ballast.
After the last, the eighth portion of rubble and thorough mixing, the concrete solution is ready for fill to the formwork.
Mix the concrete mixture can be shovel, garden hoe or flat.
How to knead the cement mortar for brick or masonry
Preparation of this type of solution is characterized by fewer water: one and a half bucket of water instead of two. The greater the water content, the stronger the solution and the slower dries. As part of a construction mortar for brickwork, cement and sand is used in the proportion of 1: 5, if the work is carried out above the ground level and in the 1: 3 ratio, if the masonry is shrouded below the soil level.
How to calculate the consumption of cement mortar for brickwork
The solution consumption for all types of brickwork is almost the same.
For the manufacture of one cube of the cement mortar, 8 bags of cement are required to 50 kg and stirred with sand in the ratio of 1: 4. Consumption of cement mortar per 1 m 3 Brick masonry solid wall is approximately 0.25-0.30 m 3.
How to prepare a small amount of cement mortar at home
There are situations in the household when a small construction repair is required with cement: seal cracks in the walls, irregularities on the floor.
In such cases, the ratio of sand and cement is most often used for the preparation of the solution. 3: 1.
A small amount of cement mortar is kneaded in a wide plastic or metal container. First, three pieces of sand poured into it, then one part of the cement is added. Use only fresh and dry cement, without solid lumps. If the sand contains stones, lumps of clay, land, then it is pre-sifted.
Cement and sand are well mixed with a spatula. Then water is poured into the container, in the same volume as cement. Components are stirred to obtain a homogeneous mixture. Do not knead too liquid solution. Properly prepared solution is well kept on a sphate or trowel. Ready solution must be used for two hours. Therefore, we knead such a volume to have time to spend it during this time.
For interior applications often instead of water during concrete kneading using a mortar.
How to prepare a cement solution for a tie
For the preparation of the solution, building materials will be needed:
- Sand. Not too wet, sinking and peeled from pebbles and garbage.
- Cement M400. Be sure to become fresh, since the quality is reduced during the storage.
- Plasticizer. It is intended to give a mixture of elasticity, facilitates the laying process and prevents the appearance of cracks in the screed.
- Fiber. Polypropylene fiber, which prevents the appearance of cracks.
In the manufacture of a solution for a screed of floor liquid and dry ingredients are mixed separately.
First fall asleep and thoroughly mix dry components: sand, cement, fiber. The proportion of sand and cement is 3: 1. Fiber is added with small beams so that there are no lumps.
If the sand content is greater than the norm, the finished screed will become crumbling and the density of the coating will be inhomogeneous.
A plasticizer is poured into another container, then water is added and stirred thoroughly. The amount of plasticizer is taken from the rate of approximately 190 g per 50 kg of cement. The volume of water is 1/3 of the mass of cement for the subtraction of the volume of the plasticizer.
After that, it is embarrassed to connect the liquid and dry parts: a dry mixture is poured into a container with water, continuously stirring so that there are no lumps.
Touch the screed too viscous solution is more difficult, but the cracks are not formed. Liquid screed is easier in operation, but often cracks and requires wetting surface to several times a day for uniform dying of all layers.
It is easier and better to stir the solution manually, but with a drill or a construction mixer with a special nozzle. Mixing time for at least five minutes. The finished solution has a form of viscous, homogeneous, plastic mass. After 2-3 minute pause, the solution is re-stirred for 2 minutes.
The finished solution is suitable for work no more than one and a half hours, after which it freezes. Therefore, the whole solution is used immediately. The re-stirring of the cement mortar is impossible.
What should be the consistency of concrete
The thickness of the cement mixture is determined by the nature of the work performed. For brickwork, walking, more liquid for plaster. In most cases, sour cream-like consistency is optimal.
There is a reception to verify the proper consistency of concrete. On the surface of a concrete solution, the blade of the shovels are cut off square and check the condition of its edges. If the mixture is crumbling, then insufficient water. Too wet or even filled with water edges mean excess moisture. In this case, it is necessary to wash some cement.
Safety regulations when working with cement
To avoid traumatization and harming to health during the mixing of the cement mortar, it is important to strictly follow the rules of individual safety:
- Use special glasses to protect your eyes from cement dust.
- Put the gloves to prevent cement from entering the skin.
- Protect respiratory organs with a respirator or petal mask.
- Avoid lifting weights, in the case of forced need to lift the cargo, slightly bent the knees, applying the power of straightening legs, and not strain the muscles of the back.
- When using a concrete mixer to wear noise-protect headphones.
Who is the most important on construction site
Cement mortar is the basis of all construction work. There is no substitute for this material. Every year new cement formulations of improved quality appear. For large-scale construction, the solution is released on special concrete factories using high-tech equipment. In private construction it is quite possible to prepare a cement solution yourself: both manually and with a concrete mixer or construction mixer. If you adhere to simple rules for the selection and preparation of the components of the solution and environmentalizing them, it turns out a strong and durable concrete coating.