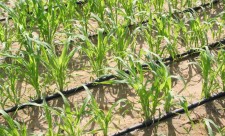
How to fold the oven Baths, saunas and pools
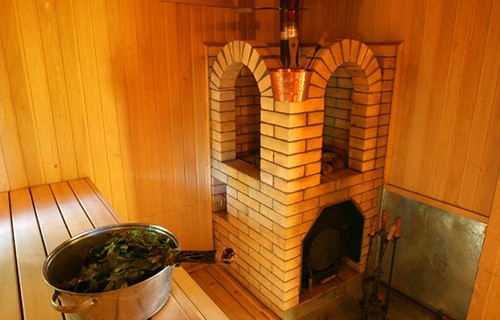
Sould not be simple metal bath stoves, as if cheaply they did not cost, the owners of the bath still seek to establish stone (brick). The reason lies on the surface - the heat generated by a brick stove spreads evenly. Couples from such a furnace does not create difficulties with breathing in a fairly extreme atmosphere.
Content
Types of brick stoves
- white;
- black;
- gray;
- with stove.
The furnace for the furnace, which call "black", has no chimney. In the old days used, and now, in some areas such furnaces are used. According to the connoisseurs of a bunny case, only such a furnace can provide good couples, but in order to use it, it is necessary to wait for all the fuel.
"Gray" oven is erected with chimney. It quickly heats up, but soot is still present and postponed on the stones. When operating this furnace, it is also necessary to wait until all the firewood will turn around.
Furnaces "In white" do not pack the room of the soot, but for its heating it is necessary for a long time about 12 hours. This is due to the fact that the stones get warm from the metal plate.
The furnace "with a stove" is characterized by a design - tank and stones are located on two cast iron plates, from which heat get. The tank is plated by brick. This allows longer than a long time to maintain high water temperature. A tank or heater can be installed above the furnace.
Choose a brick for building a furnace
A red ceramic brick of standard size is used to masonry the furnace with their own hands.
Brick choose proper geometric shape. There should be no cracks, chips and other defects on its surface. A qualitatively burned brick with a slight blow hammer publishes a ringing sound. It is strictly not desirable to apply a slit or silicate brick, since they are destroyed from exposure from high temperatures.
Masonry solution
Without a doubt, the masonry solution is preferably made from the same clay from which the brick is made. In this case, the thermal expansion coefficient of brick and the seam will be the same and accordingly, it will extend the service life of the furnace.
From practice it is known that the thinner of the seam, the better the quality of the masonry. The optimal seam thickness is 5 mm, you can even thin. For the manufacture applies river washed sand. The presence of il or its traces is unacceptable. The sand fraction should be 1 - 1.5 mm. The clay is placed in the container, crushed and poured with water. In the flooded and mixed state, the mixture remains for a day. The water level should be higher than the level of clay.
After the time passed, the mixture is passed through a sieve before the destruction of lumps. As the uniform clay mass is obtained, sand is added to it. The volume of flooded sand is determined by the fat content of clay. In the resulting mass, the ratio of 1/2 to 3/2 sand from the clay volume is maintained.
There are two simple ways to assess the quality of the resulting solution:
1. The first method.
From the resulting clay with hands make a ball, which in diameter should be about 5 centimeters. Then it is placed on a wooden plank and the second plate starts to put it up to the preparation of visible cracks. From the experiment, it follows the conclusion: the ball scattered before the crack is obtained - it means the solution is poor quality. If the cracks were formed on 1/3 of the diameter of the ball, then the solution is normal, and if the cracks appeared by ½ diameter, then the solution requires the addition of sand.
2. The second method.
Two balls with a diameter of about 5 cm are made of the resulting clay. One ball is rolled into the cake with a diameter of about 10 mm. Then the ball and the pellet leave in the shade for 2 to 3 days. If after an indicated time they were covered with cracks - this means that the solution is too fat. The dried samples did not receive cracks, and the ball abandoned from a height of 1 meter on the wooden board remains the whole, then the solution is good.
Preparation for masonry
Tool for work
- corner grinding machine with abrasive circle for metal and stone;
- drill and nozzle-mixer;
- 10 - 12 liters bucket;
- master OK;
- level;
- plumb;
- wooden kiyanka;
- roulette and marker.
Features of masonry furnace
The furnace should be installed on a separate foundation, independent of the foundation of the structure. It also arrange hydraulic insulation.
Founding of the base of the furnace is carried out below the bunny floor using cement-sandy solution. In the process of the furnace base device, in the place where the furnace door will be located, the metal sheet is placed at the floor level.
Each row of bricks first stacked "on dry", without the use of a masonry solution. This is done in order to choose bricks of the same size and optimize the thickness of the masonry seam. The masonry of each row begins with an angular brick. Before the brick is put in place, it is immersed in water for a few seconds.
Masonry Rules
Each row of bricks is laid according to a specific scheme. This scheme is called order. There are many such schemas. Each order provides various parameters of the bath oven, design and amount of heat.
Kielma is buried by the desired amount of solution and unfolds in the place where bricks will be installed. The solution is carefully smoothed. It is necessary to ensure that the same amount of solution is obtained on the Kelma. Brick, which has already visited dry styling in its future place, is immersed in a bucket with water (no more than 20 seconds) and stacked in place.
Carefully tapping the cielma, the brick is placed in place and follow the thickness of the seam (no more than 5 mm). The solution that is squeezed out from under the laid brick is collected by Clavma. The solution with the solution is repeated, only before laying the next brick it is necessary to smear the solution on the end of the already installed brick.
The next moistened and ready for laying brick, the end is also lubricated. The thickness of the layer is not more than 3 mm. The new brick is stacked in such a way that the face with a solution was lubricated to each other. Tapping with Colevma, we give a masonry seam to size 5 mm.
Subsequent rows fit in the same way, the main thing is more often checking the correctness of laying in order. After the three or four rows are laid, they need to wipe the wet rag.
The following rows of masonry are also carried out as the first, we are more often with my friend.
The coincidence of vertical seams is not allowed. Vertical seams should be blocked by bricks on top and bottom.
Vertical seam should be blocked by a brick next and previous rows.
Can not be laid with bricks cleaved quarters inside the flue channel, under the action of heat, they start to collapse. Bricks with squared edges fit only in the clutch, but no it is not inside the stove or chimney.
furnace chamber
Combustion chamber made of special refractory bricks - refractory.
Combined installation simple red and refractory fireclay is not allowed, they have different coefficients of thermal expansion. Due to its fire-resistant properties, fireclay brick is used for improvement of the combustion chamber.
There are several points on which we must focus:
- the bricks are laid on edge;
- between the walls of the combustion chamber and the oven must be a clearance of not less than 5 mm;
- binding between a fireclay refractory brick clay should be used.
Installation of furnace devices
These devices made of metal - iron. Features Installation of devices is that they stop with gaps, otherwise, the heated iron simply break off the brick.
- Grate - grate.
Grate laid on a prepared place without the use of solutions or other adhesives. The gap between the edge of the grate and bricks is at least 5 mm. When choosing a furnace project must take into account the fact that the grate should be freely retrieved.
- Doors - the ash-pit, water treatment, flue.
In the frame of the door has a mounting hole into which insert a soft wire and roll into a bundle. Next, in brick, installed in an area spread solution. Placing the door in place, it is necessary to check it horizontally and vertically. With other bricks, both clamps are used, fix the door in the obtained position. The ends of the resulting tow put into the joints.
Then, lay the ends of the wire in the masonry joints. And we continue obkladyvat door bricks. Above the door at the same time should be placed two bricks of half the length of each side of the door.
Chimney
One of the harmful passions bath lovers - this longing raskochegarit stove, so that would be "Wow!". But in this case, fans of this method kindling bath forget that in this case the temperature of the gases at the outlet of the furnace reaches 75 0C. A permissible (working) for chimneys of metal not more than 45 0C. Yes, it is possible to exceed, but not more than 20-30 minutes. Heaters also can not withstand such temperatures.
The output of this situation is simple - to make the first knee of chimney from thick steel or cast iron pipe.
Drying the oven
It is not possible to immediately start the rebound furnace at full capacity. The field of completion of the work is dried. For several days to hold out open doors and dampers, it will not be superfluous to open the windows and doors in the bath to create a draft. After 4 - 5 days, it is possible to arrange a test furnace as an experiment. The fuel uses a small chip, and the firebox time is not more than 15 minutes.
Such short floors can be held two or three throughout the day. The stove readiness indicator in this case is the surface of the damper, if condensate is collected on it - this means that the furnace does not dry. As soon as he stops falling, the drying was successful.
We consider expenses
The size of the value of the furnace masonry depends on the value of the components:
- foundation;
- bricks for the furnace;
- furnace equipment;
- chimney.
Since all work will be conducted independently, all expenses will be reduced to the value of materials and their delivery to the place.