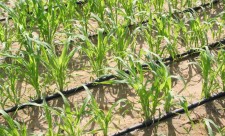
How to make Phaneru do it yourself Building materials
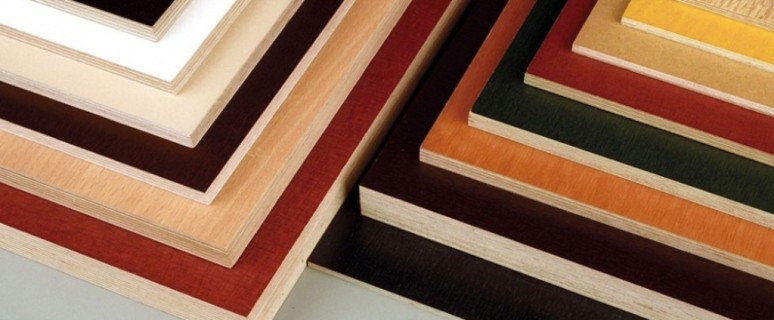
The most versatile and simple in the processing of building material is plywood. Despite not very low cost, popularity and demand for it grows more and more. Unlike wood, plywood is lighter, well, the advantage over Fiberboard and chipboard is obvious - ecological purity.
Content
Product specifications
Wooden plywood is made by gluing a very thin wood sheets (veneer). This material is easily amenable to different processing, both thermal and mechanical, it can be painted with paint and varnishes of any kind. It is worth noting that Plywood is very well harmonized with any other material than designers successfully use. Veneer, as otherwise, the people are called plywood, has the following characteristics:
- It has a layered busty structure.
- For the production of material, veneer sheets 2-4 mm thick, as a result, the thickness of the plywood sheet can reach from 4 to 32 mm.
- The quality of the construction plywood depends on the type of veneer, which is natural and tinted. Natural veneer is more durable, stronger, environmentally friendly and safer.
- It has very good thermal conductivity and environmental friendliness, which is superior to chipboard, fiberboard and MDF.
- The ratio of operational indicators and the cost of production in plywood above metal or plastic.
- It has enough weight, easily tolerates temperature differences.
Classification of plywood
Depending on the characteristics of Plywood, any hardness differs in service life, appearance, types and varieties:
- For purpose, it happens:
- plywood construction - used in the construction of houses as overlaps and partitions;
- industrial plywood - for shipping, wagon and motorways;
- packaging plywood - used for packaging of overall products, the same furniture, electronic technology and the other;
- furniture plywood - made of home and office furniture;
- constructive plywood - used to create various designs, scenery and exposures.
- Depending on the number of layers of plywood veneer, it happens:
- three-layer;
- five-layer;
- multi-layered.
So that the sheets of veneer were located symmetrically in relation to the central sheet, they are taken by an odd amount. In the case where the number of veneers is even, it is necessary to glue two central sheet perpendicular to two outer, it will strengthen the strength and resistance to deformation. The thickness of the plywood leaf, the one, respectively, is more expensive.
- There are three types of plywood:
- moisture-resistant plywood (FC) - moisture resistance relative, because even in rooms with not very high humidity it may be a story. Actively used in the manufacture of furniture and packaging material;
- increased moisture resistance (FSF) - due to good resistance to moisture applied not only for internal works, but also external. This type of plywood is well bent, it is easily amenable to a different processing - drilling, grinding, planing, sawing, perfectly painted and opened with varnishes. Many builders note that working with this material is great pleasure;
- increased moisture resistance of melamine (FQM) - under the manufacture of melamine or bakelite glue. This type of plywood has a folk name - marine plywood. It is used for shipbuilding, aircraft engineering, mechanical engineering, it does not sink in water, has good resistance to most aggressive media. FCM is also characterized by the fact that it can withstand more than 100 staining.
- Plywood treatment can be laminated or ordinary.
- Depending on the material from which the veneer is made, plywood happens:
- birch - less in demand due to its high cost;
- coniferous plywood - produced from larch, pine, fir, fir;
- plywood from the Siberian cedar - is used mainly for the sake of decoration.
- Depending on the number of defects that can be revealed by external features, Plywood has several classes:
- E class (elite plywood) - the manufacture of plywood without any defects, not counting only small changes in the structure of the tree itself;
- I - a defect is allowed not more than 20 mm in length;
- II - a defect is allowed not more than 2% of the total material area;
- Iii - a defect is allowed in the form of cracks not more than 10 pieces per square. m., which can be up to 6 mm;
- IV class - very low quality plywood with cracks from 40 mm.
- Depending on the surface treatment of plywood, it can be:
- unlined (NSH);
- plywood polished only on one side (sh1);
- grinded on both sides (sh2).
The grinding surface is better to process, it has good adhesion with varnishes and paints, so such a plywood is more expensive and it is customary to use when decorating. Unfordable plywood is often used for hidden work, its price is small compared to polished.
Plywood manufacturing technology do it yourself
Today, Phaneur can be purchased at each construction store. But many lovers do all of themselves as independently, how to make Paneru do it yourself. It turns out that it is possible. For the manufacture of plywood you will need a veneer, it can also be made independently.
Making veneer at home
Veneer is divided into three types:
- Natural - veneer, which has a natural color and wood structure. It is manufactured by spilivation, lunch and planing of thin layers. It is important to preserve the wood structure. Environmentally friendly material, very light.
- Colored veneer is the same natural veneer, only painted in different colors.
- Fine Line is obtained after the reconstruction of the old imperial veneer, which is formed into blocks, and from them, in turn, make a veneer. It can have any color gamut, drawing and sizes like a natural tree.
Depending on the manufacturer's method, it happens:
- Veneer sawn - from all kinds the fattest material, it turns out during the sawing.
- The planed veneer is obtained in the process of planing of wooden bars.
- Lush veneer is manufactured using a vesting mechanism.
Tools for work
For the manufacture of veneer, and in the future plywood from it, you will need the following material and tool:
- wood (birch, pine, spruce), which you can purchase in a specialized store or on woodworking production;
- a venerol system for the manufacture of peeled veneer;
- piloram for the manufacture of sawn veneer;
- planed steel plane plane;
- grinder;
- grinding machine;
- press "Cold and Hot Method";
- drying chamber;
- phenol-formaldehyde resin as glue and components to it;
- pencil;
- varnish or paint.
Steps of veneer manufacturing:
- The first thing to be done is to select raw materials (wood). Prefer birch or pine, as a last resort, ate or use it to combine plywood. Birch is a longer material, and pine and spruce is easily ease.
- Prepare wood to work - clean it from the cortex and saw on a bars with a length of 1 m with a sharpening machine.
- Straighten the workpiece vertically.
- With the help of a venerol system, we send the veneers with the thickness you need. If you make a planed veneer, then you need to use the plane, and the sawmill is useful for sawn veneer.
- Cut the veneer to the desired billets.
- Seeing the veneer in the drying chamber, in which it is possible to adjust the humidity.
- Exceeded veneer sort and relent.
- Then the dried veneer of good quality can be made, and the discarded it is recommended to refresh and glue to get a sheet of the desired size.
Assembling plywood
Ready sheets of veneer can be collected in packages:
- Apply glue on both sides of the veneer and connect the sheets in the packages.
- Send packets under the cold press.
- Spread the veneer packs into plywood sheets with a hot press. Do not forget that the number of veneer sheets must be odd, it is necessary to combine them so that the fibers of the glued sheets are perpendicular to each other.
- Now you can crop plywood sheets for the size you need.
- Push the phaneer with a grinding machine so that the surface becomes perfectly smooth.
- Finished Phaneur can be decorated with paint or open with varnish.
How to Bend Faneru
In some cases, for example, in the manufacture of furniture, you may need bent plywood. Bend it is possible at home. It is easiest that it will be done with a flexible plywood whose thickness does not exceed 3-4 mm. Flexible Fauer can be purchased in the store. But you can bend the paneur of any thickness to bend, only first it is necessary to carry out the accurate calculation of plywood - in which particular place you will bend it.
The process consists of the following steps:
- Sparking. In terms of production, this is done in special installations, after which it is bent under the press. At home, you can disappear sheets of plywood in the bathroom or in other tanks. The thicker material, the longer it needs to withstand in water. The minimum time is 15 minutes, the maximum is 5 hours. The water temperature must be 90-100 ° C. But, as you understand, it is quite difficult to implement at home, and not cheap. It is possible to replace sprinkling in warm and cold water, while the process time increases for cold water 15-30 ° C 20 times, for warm water 60 ° C. 1.5-2 times. After steaming, plywood sheets must be bent and secured so that they dry in this position completely. To speed up and facilitate the process, you can only moisten the surface of plywood, and unpack the place of the planned bend.
- Cut. The method is suitable for plywood with a thickness of 15-24 mm. Using the cutter, you need to make small cuts (not deeper than half of the sheet thickness) in plans of the planned bend. This method is used in the construction of boats. The outcropped blank is bent, stick on it another sheet of veneer and fix. In such a position of plywood should be at least a day.
- Gluing. This method helps create a detail of the rounded form. Cut pieces of 5 mm more than the required length. Spread on the table the details so that in the finished product of the veneer direction alternated, it is necessary for greater strength of plywood. Glue together all the details and fix them on the workpiece you need. When your item will dry up, stick it and remove the excess glue.
Useful advice
Before proceeding to flexing plywood, read the useful information:
- Cross fibers are more difficult to bend than longitudinal.
- The humidity of the premises in which you plan to store bent sheets of plywood should be low - no more than 10%.
- Starned and clouded blanks are easier to be bent in a warm state.
- The thickness of the plywood, the more difficult to begun it.
- It is easier to begun to Faneru, in which the layers of the veneer are located in parallel to each other.
- Do not overeat Phaneur in the water, it can bundle. To find out the exact time required to break the plywood of a particular thickness, you can use an experimental workpiece. Soak it and check the condition every 3-5 minutes.
- Very complex and volumetric designs are still recommended to bend in specialized workshops.
Staining plywood
For a longer service, Phaneur must be painted or opened with varnish. This is especially true of the material that is used outside the premises.
Stages of painting work with plywood:
- The first step is to sand the plywood. For this purpose the skin №80.
- After this plywood is covered with acrylic primer and withstands at least 4 hours.
- If necessary, the surface is covered with putty on a tree.
- After drying, the putty is again covered with the surface of the skin No. 80-100.
- Another layer of primer is applied and withstands 4 hours.
- And the final stage there will be plywood staining itself.
After reading how to make Faneru, as it bends and stained, you can build not only the arches and partitions in the apartment and in the country, but even make it yourself to make and decorate the furniture.