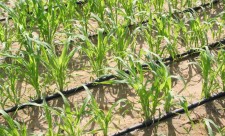
Metal garage with his hands Construction
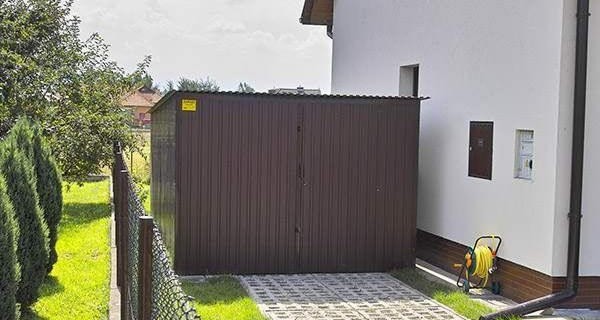
Buying a car, the driver has to take care about the future of "life" of the iron horse. Garage save motorist from car parts paint to protect against rain, as well as the frequent repairs, the cause of which could become a fallen tree or awkward cyclist.
Content
Comparing the stone and metal garage, we can say with full confidence that the metal has more advantages. If you have the time to autograph the production of metal garage, let's understand the intricacies of assembly and forms, and you have to select an option that is acceptable to you.
Despite the proclaimed administrations of many, especially large cities, the "war" of metal garages, they are still very popular among motorists. This popularity can be attributed to several factors:
- The price, which often can not be compared with the price of heavy stone garage.
- The high speed of production, placing orders to finished product takes a few days.
- The simplicity and speed of assembly on site.
- The possibility of manufacturing a collapsible metal garage.
Methods of making metal garage
1. As always, there are two ways to resolve the problem, or roll up your sleeves, invite a few mates and yourself metal garage to make their own hands. This solution requires certain skills of work with welding machine, angle grinder, a drill and a paint sprayer.
2. The second option - is to place an order for the company, which specializes in the manufacture of metal structures of this type.
Before starting work on the construction of the garage, the consumer has to choose to be the next garage of what material.
Materials for the garage
- standard sheet and metal;
- profiled sheet and a special bent profile.
We consider the construction of the garage of the conventional, standard rental with a gable roof, which will be erected on the spot. Dimensions of the garage are in the process stages:
- 5.5-6.5 m length;
- 3,2-4 m width;
- height (from floor to roof ridge) 2.2-2.5 m.
Materials and tools
For the construction of a metal garage with your own hands, you need the following materials and tools:
- Concrete and rebar for the foundation.
- Steel corner shelf with 50 mm.
- Sheet steel flat, the thickness and other dimensions are determined by drawing.
- Welding apparatus, a working current strength of at least 200 A.
- Angle grinder, cutting and stripping circles.
- Individual protection means.
The difference between modular and integral garage
The one-piece garage is made on the spot. All parts are held together by welding "firmly" and do not understand. The one-piece garage is difficult to transport, as required transpartirovka finished large-scale structures. Also, when transporting it is likely damage to the welding seams.
Demountable garage is a set of elements made of sheet steel and equipped with holes and slots for their bonding with each other via bolt connections. This garage can be transported. This requires to disassemble the structure and after transpartirovki gather again.
Preparation for work
Construction work, especially if carried out on their own, require particularly careful preparation. It includes:
- Development of drawing a metal garage.
- The calculations required amount of materials and tools.
- Purchase and delivery of materials and tools to the work site.
Foundation
Construction begins with the arrangement of the garage foundation. Practical experience suggests that under the garages of this type is quite possible application as a continuous footing and foundation of reinforced monolithic slab.
1. Before you start work related to the foundation, it is necessary to clean up the construction site. It may well have to remove the top layer of soil. The platform must be flat and be positioned in a horizontal plane.
2. After stripping, you can begin to dig a trench for the foundation. Knowing the overall dimensions of the garage, it is necessary to mark the future trench. The width of the foundation trench lies within the width of the bayonet shovel, and its depth can be from 150 to 300 mm.
3. After the soil is extracted, it is necessary to put a sandy-gravel mixture on the bottom of the finished trench and thoroughly take it.
4. In order for water to enter into a garage during a strong rain or in the spring during an active melting, you can raise the top edge of the foundation above the ground level by 100-200 mm. To do this, you will have to make a formwork.
5. When pouring the foundation, it is necessary to install reinforcement pins at the corners and in the middle of the parties to fasten the bottom edge of the garage. After drying the concrete (48 hours) you can proceed to actually, the construction itself.
Frame
The frame is the basis of the whole structure, it is from its strength that the quality of the erected structures, its resistance to wind and light load depends on its strength. Therefore, the framework is erected from standard metal rolling, for example, a corner 50, with a shelf thickness of at least 3 mm or channel 5. When assembling the frame there are two ways to connect its elements: with welding or bolts.
Depending on the type of the chosen roof it will be clear, it is necessary to make rafter structures or not.
1. The construction of the carcass of the garage begins with the manufacture of the lower frame. In accordance with the drawing, the garage cut the beams and fasten them among themselves on a pre-made foundation. It is also necessary to remember that the collected frame should be associated with predetermined pins, this ensures the fixability of the frame. These pins should be located inside the frame.
2. The next step will be the installation of angular racks, special attention should be paid attention to their verticality, i.e. When installing uses measuring instruments (plumb, level), which will ensure the quality of installation. The installed racks, along the top edge, are cut off with a metal strip or a corner.
3. After installing angular racks, vertical racks are installed along the side and rear walls. In the future, they will serve as the basis for fastening sheet shestts. The distance between them should be less than the width of the sheet for several centimeters (from 3 to 5), especially this is relevant when the framework is trimmed by the brass sheets.
Roof
Based on the developed drawing, the farms needed for the roof of the garage are made and mounted. Farms are fasten with welding or bolts, depending on the type of garage (collapsible or solid). Each item must be securely strengthened. It depends on the strength of the roof and its wind resistance.
Sheaving
As a material for plating the garage frame, you can apply both a regular metal sheet and profiled sheet. The main thing is that the thickness of the sheet is at least 1.2 mm. It is possible to mount with long screws, nails or brackets.
From what place to start the trim? As a rule, it starts from the front rack. For reliability, that the roof does not flow in the seams, the sheets impose a mustache about 15 centimeters and then treated with sealant. After completing the walls of the walls, the roof is trimmed.