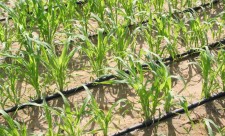
Setup and adjustment of metal cutting machines Instruments,Useful advice
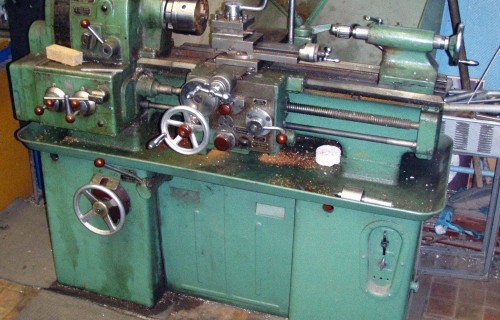
Production workshops have a large range of Matthewing installations with an automatic or semi-automatic system. Installations of this type are treated with processing parameters and support automatically this ability. Efficient use of equipment is possible when conducting a high-quality label and modern one-handing of the process line.
Content
- General Methodology Calculation of Matthewing Stunches
- Adjustment of electrical equipment for turning machines
- Methods for adjustment of electrical equipment of metal cutting machines
- Electric metering devices
- Fixtures for metal cutting machines
- General scheme for setting up metal cutting machines
- Types of settings for metal cutting machines and tools
- Repair of metal-cutting machines
General Methodology Calculation of Matthewing Stunches
Adjustment - specialization of metal-cutting installation to the manufacture of products according to the technological characteristics: dimensions, shape and size. Classic operation is step by step:
- The technical installation technicians are studied, its functional destination.
- The unit is completed with the tools and the sheet.
- It is set to the instrument and adapts, designed to fix items.
- Mechanisms are governed by matters of matures and booting devices.
- Installations are installed for the billets.
- Changing coolers or tough wheels.
- Proprietary setting and the preservation of the release instrument is performed.
- The rotation of the spindle rotation is established. There is a pre-wedding ranking of the length of the length of the supret. The position of the movement and change of the rotational fountain of the spindle is set.
The above is completed, the preparation of the metal cutting machine is considered to be made. The mechanism is ready for the processing of parts in a given mode, with the maintenance of forms and sizes, exactly coinciding with the drawing. The adjustment of metal-cutting machines is performed using the electrical and mechanical parts of the unit.
Adjustment of electrical equipment for turning machines
Turning group of machine tools is used in each production. These are universal or with a narrow-controlled functionality of the machine. Most often by adjustment is the electrical equipment of machines. It is performed in several cases:
- Before conducting a test test at the manufacturer. The complex of work, which drives all elements of electrical equipment, ensuring the further technological processing process in a certain specified mode.
- Before passing the machines to the consumer. Test adjustment.
- Repeated or secondary adjustment. It is performed after repair and restorative maintenance, with the machine failure in the system, with a constant operation in a strained mode. Starting covers the verification of the compliance of the replaced electrical equipment or elements of the installation project. Along the way, possible malfunctions are detected and eliminated in the scheme, electrical apparatus, drive systems and elements are adjusted, insulation integrity is checked, ground efficiency. Make control records of devices and sensors. Submit voltage and conduct a test for overloading the scheme.
Methods for adjustment of electrical equipment of metal cutting machines
Electroschemes that control the drives of machines differ in the complexity of the scheme for the electrodes used, by intended. The operation of the adjusters is not built in the template manner, but has accommodated methods to identify a malfunction:
- Classic or observation method. The easiest way to identify malfunctions in the work of the machine. The order operator monitors the interaction of the schema elements, evaluates the effectiveness and correctness of the cumulative action. This method is applicable to all machines, including complex automatic installations. No more than 3-4 units of equipment take part in such devices for one operation. The professional adjuster knows the location of these functionals, their location in the housing, and by their state, the specialist is an act of operation, the direction of movement. The observation method in this case helps or identify the cause of the fault, or narrow the search area of \u200b\u200bthe defect site.
- Exception or localization. The area of \u200b\u200bverification is artificially reduced. The faulty element is detected by disconnecting the node schemes before the failure is detected. This is a long and painstaking process: electrical and mechanical elements are excluded.
- Comparison. Presumably defective element or item is replaced by the same serviceable. The detected defect is eliminated and the time for installing the working part is reduced.
- Reverse sequence. The method is applicable to schemes from several components, functionally dependent on each other. The output of each link is checked in the direction of the last to the first. Effective and fastest method - allows not only to quickly identify a defective area, but also pass the control testing of the chain. The use of the method reduces simple and increases productivity.
- Direct sequence. This method is used when adjusting experienced machines with a complex circuit and numerous electrical apparatus. Performed with insufficient workload experience. The method is simple, but takes from 10 to 48 hours of equipment downtime. Used extremely rarely.
Electric metering devices
Adjusting the electrical equipment of metal-cutting machines is performed using special and universal meters:
- Universal devices with multiple types of scales are used for schemes consisting of alternating and direct current. Such sensors include voltage indicators, ampere and voltmeters, tester probes.
- Special devices are used to check electronic devices, circuits with electronic sensors. The execution of this type of adjustment makes it necessary for work and experience in this area.
Fixtures for metal cutting machines
The devices are divided into groups and have a different functional destination. For setup of metal cutting machines, two types of fixtures are used:
- Urals - specialized setup devices. Assigning data nodes: Location and fixing a strictly defined billet. Comes in the complex, and then collected under a specific workpiece. Elements are intended for repeated use. Adjustment is made for each batch of products.
- SPB - defective devices. Used to accommodate and fastened samples with close in size and constructive parameters characteristics. Apply to the manufacture of multistage shafts, flanges, disks. Adjustment is done one-time and does not change during the operation of the aggregate.
General scheme for setting up metal cutting machines
The essence of the setup is to ensure accurate matching of the processing of blanks according to the specified parameters on a particular machine, to ensure the function of the perfect coincidence of the finished disc drawing project.
General setup scheme:
- The exact position of the stop, the cutting tool and the processed billet / part is set relative to the position in the plane and coordinate systems.
- The conditions are ensured based on a specific working job, the drawing for the manufacture of the part completely coinciding by parameters with a reference sample.
Initial setting as it work on metal-cutting machines is knocked down due to wear of the cutting edge of the tools. Details begin to be made with a large error from the specified parameters. Therefore, it is configured for a specific billet branch, and then the next adjustment of the machine is performed. According to statistics, a simple adjacent setting is 10-15% of the total process of the technological process.
Types of settings for metal cutting machines and tools
Exact quality processing of blanks is associated with the correct setting. Combining methods and methods of selection to ensure high accuracy is called dimensional setting.
Overall and linear values \u200b\u200bof parts are set with admission and error. To calculate the possible error of the settings use a special formula. According to the quadratic summation of all the well-based values.
Semi-automatic trial work
- A small surface fragment of the sample is processed by a cutter.
- The measurement results are used to change the position of the cutting tool, taking into account the errors.
- Claims for error settings are presented depending on the design and functionality of the work unit. For example, for boring and chub-cutting machines with CNC, the products of the processed product is maintained in automatically, and this increases the requirements for the malfunction and reduce errors.
- Adjustment Outside the machine is performed using optical devices, for example, BB 2010. To check the device is mounted on the panel or countertop. The base of the device from two caretok: transverse and longitudinal. The carriages are moved by ceric guides. In order with the installed projector. The bracket with digital display is strengthened. The exact coordinates of the carriage installation are achieved by the microcomputer node. The surface of the turret or caliper is attached to the surface. It is installed in it with a cutting tool. The simulator of the reference system serves a digital indication with an inductive linear displacement sensor.
- Configuring the cutting tool is made by moving the adjusting screws along the two coordinates in the horizontal. Having achieved alignment with the crosshair of the projector, align the cutter vertically. The exact installation is made using a clock indicator from the instrument kit. The instrument setup is made according to the control unit certified by the size of the base.
- Modern systems for the size of the cutting tools consisting of an optical instrument, a projector, digital display immediately equipped with a revolving head. These systems can set up more than a dozen different metal cutting machines. For example, MicroCet EG-400. Used to optically adjust the turning cutter in the rapid tool block. Conducts a tool setting up to 0.01 mm. Available in two modifications: with a digital sample and light display display, with an optical reference system.
- The advantages of the method: the tool setting is not performed on the machine. Simple technology is eliminated. High accuracy of setting the handling of parts, strictly follow the parameters specified.
Method disadvantages: attracting additional devices. The method does not compensate for the inaccuracy of positioning, it does not adjust the rotation of the turret head.
Automatic trial working stroke
- The first way. Modern technologies allow you to set up the top of the cutter. For this, the cutter is set to the holder, the sample movement program is specified to the sensor. The vertex position error is calculated and the automatic adjustment and positioning of the cutting surface.
- The second way. A special program for moving the cutter to the workpiece is set. Cheap removal is performed. Automatically determined performed, real size. Compare the result obtained with a reference sample. The trajectory and position of the cutter is automatically adjusted.
Repair of metal-cutting machines
Large and private industrial enterprises operate metal-cutting machines with a planning-warning repair. Faults are detected in electrical equipment, setting chains are installed. Preventive repair helps to reduce downtime machines by 70%. Minor repairs always leads to a collection of settings. They must be restored at a professional level. Apply the modern method outside the machine setup. Methods of repair and commissioning work are entered into a plan for maintenance of technology and are carried out with a stop of production and without it.