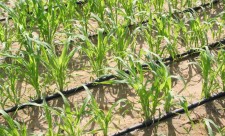
Wall formwork: Calculation, Installation, Fastening Construction
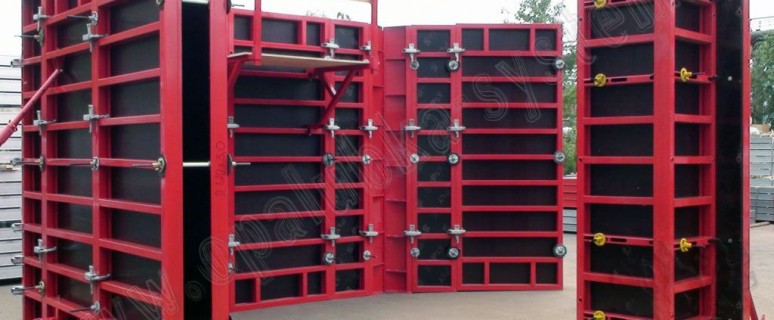
The formwork of the walls is a design, due to which high-quality laying of a concrete solution occurs. Its main scope of application is the installation of reinforced concrete elements of buildings. Our article we will talk about how to make a formwork for walls with your own hands
Content
Types of formwork
A concrete solution filled into formwork has a rather solid pressure on it. Therefore, that the design is not broken, it should be reliable and durable.
For the manufacture of formwork, various materials are used:
- Boards. The most popular and affordable material.
- Plywood or OSB sheets. Different with high cost, but reduce the amount of consolidated concrete.
- Metal. It is rarely applied, from it makes racks for fastening formwork shields and other elements to enhance the design being created.
- Polystyrene foam. The main scope of application is a non-removable formwork device when the material is additionally used and as a heater.
Depending on the method of the wall formwork device, the design is divided into:
- removable;
- non-removable.
Removable design is disassembered after setting the concrete solution. In most cases, wooden boards or metal serve material for its manufacture. If necessary, the removable formwork can be reused.
Failure formwork in the flooded concrete remains forever. For this reason, heat-insulating materials are used for its manufacture, which simultaneously protrude as a sound insulation coating.
Calculation of formwork
To create a design, it is mandatory:
- calculation of its bearing capacity;
- determination of the required amount of materials;
- the choice of the most optimal erection technology;
- the cost of renting wall formwork.
Only a properly compiled project guarantees high-quality installation work with minimal cost. On the formwork size, a significant role will be influenced:
- area of \u200b\u200bfilling concrete construction;
- thickness of erected walls.
The amount of concrete used directly affects the number of reference racks, with which the deformation changes are not allowed when pouring the solution.
The main criterion for calculating the formwork made of wood is the dimensions of the board. Its standard dimensions are:
- length - 6 m;
- width - 1-1.5 m;
- thickness - 2.5 cm.
The dimensions of the filling design are determined by dividing the length and width of the board (height). On average, to create 1 m³, it will take 40-42 boards that have a width of 1 m.
Removable wooden opal
In essence, the removable formwork for walls made of wood is several batches connected to each other. You can use both thick boards and plywood (or OSB plates). If the choice fell on the paneur or OSV, then the acquired material must be absolutely moisture-resistant.
For reliable fixation of wooden panels, a bar is used, which simultaneously acts as the rigid rigidity. Wire twists, frames or wooden screeds are used to attach individual parts formwork.
The inner part of the shields is fixed using spacers made of timber, size 5 * 5 cm. For fastening the outer side of the formwork, uses:
- pegs;
- clamps;
- clamping boards;
- truck.
As a result, the installation of the wall formwork should withstand both the direct pressure of concrete and the side. The connection of the shields is carried out in such a way that their width corresponds to the sizes of the flooded surface. If a solid amount of concrete solution is to be pledged, the formwork is installed using guide boards. For their attachment, pegs and decks are used.
In the process of the formwork device, special attention is paid to the coincidence of the deck planes with the auxiliary elements. For more reliable stability of the structure, additional fastening of the shields with vertical disconsees occurs. Related rows are connected by struts and clamps.
One of the important requirements when creating a removable formwork refers to the lack of large gaps. Their maximum value should be within 3 mm. Otherwise, when the concrete solution, the concrete solution will flow out that it will reduce the quality of the surface fill. Before concreting, all the cracks are wetted with water.
If it was not possible to make narrow slits, then come as follows:
- slots, the size of 4-10 mm is close to packles;
- the slit, the size of over 10 mm is closed with wooden slats.
Removable metal opaubka
This design is made of leaf rolled products. They are trimmed with a frame made of corners and profile pipes. For removable wall formwork, sheet rolled sheet, 1-1,5 mm thick and a profile tube with a cross section of 2 * 2 cm.
To fix rental to the pipe, screws for metal or point welding are used. The device of a non-removable formwork involves creating a crate whose cells range from 0.2 * 0.2 m to 0.4 * 0.4 m. The specific cell size depends on the thickness of metal sheets.
When mounting the formwork of walls, the upper rows are connected by jumpers. Immediately it is necessary to pave the sleeves from the pipes through which various communication systems will be carried out. To prevent the design of the design, you need to install additional support racks.
Simplify the dismantling of the formwork and keep the wall in normal condition by lubricating the design with a special composition.
Dismantling removable design
Dismantling work begin a few days after concreting the wall when the upper layer is free. First disassemble the upper elements of the formwork.
The process of dismantling the removable construction provides:
- unscrewing nuts on studs that connect parallel shields;
- removal of several retaining slope racks;
- disconnecting locks that connect structural elements.
Disassembling the removable formwork of walls at the highest point is carried out very carefully. If, after dismantling the first shield, it turned out that the concrete solution was frozen normally and the wall surface is not impaired, then you can safely disassemble the remaining formwork.
Failure opal
Failure formwork for walls is the perfect option for those who want to build a warm house without attracting specialists. The design consists of elements that are hollow blocks with locks to fix these blocks. The non-removable formwork is characterized by speed and simplicity of assembly, since blocks without problems are cut using a conventional saw.
As a material for the manufacture of non-removable designs can be used:
- Polystyrene foam. It is characterized by increased strength, excellent thermal insulation properties and minimal load on the concrete surface. Shears air, which allows the concrete to "breathe".
- Arbolitobeton. Its distinctive feature is the presence of air bubbles that are between wooden chips. Due to this, the reliability of the formwork increases several times. The material is characterized by fire safety, moisture resistance and inconsistency of rotting.
- Fibrololite. It consists of caustic magnesite and wood chips. In some cases, Magnezit is replaced by Portland cement. The material is practical and environmentally friendly, frost-resistant and vapor-permeable, fire-resistant and bosel.
The most popular is the non-removable formwork made of polystyrene foam. The connection of the elements of this formwork occurs with the help of jumpers made of polystyrene. Due to the fact that the blocks are light and empty, much easier will be the process of reinforcing and concreting.
The lower and upper planes of formwork elements consist of special complex locks, thanks to which the block separation is excluded when concreting walls. And this in turn will reduce the use of various backups.
On the inner surface of the polystyrene foam formwork there are grooves that contribute to a more efficient adhesion of the walls with concrete solution. The outer side of the structure is characterized by a smooth surface, which simplifies its finishing finish.
As a result of the adhesion of polystyrene foam blocks, their outer layer will protect the reinforced concrete base from the freezing and the negative impact of natural factors, and the inner layer will prevent the heat of the heat of the cold wall.
Video on the creation of formwork for walls: