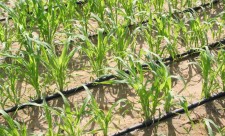
Sucks on windows from sandwich panels do it yourself Window
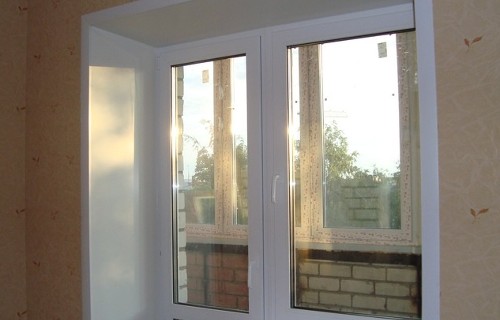
The next job after installing new windows is the installation of slopes. From how important this procedure will be performed correctly depends on the insulation of the room. Materials for the finishing of slopes are quite a lot. One of the most modern and easy-to-install is a sandwich panel.
Content
Features Sandwich panels
Sandwich in the modern building nomenclature it is customary to call materials that consist of several inhomogeneous layers. Sandwich panels for slopes are:
- two-layer,
- three-layer.
Two-layer slides consist of an internal filler, most often from pressed foam, insulation and an external hard coating of PVC.
In three-layer panels, an internal sheet is added to the outer PVC. From the practical side, it is inappropriate, since plastic has very weak adhesion with any fixing materials. The only argument in favor of three-layer panels is planned to change the windows to another size in the next few years and redo the slopes.
Sandwich technology allows you to combine external aesthetic appearance in one design and reliability. Polyfoam has zero thermal conductivity, respectively, the cold of the walls of the house is not transmitted to the frame and the windows do not postpone. On the other hand, such slopes have an energy saving effect, reflecting up to 95% of heat back to the room.
In addition, the slopes from the panel sandwich are sold already in the finished form, therefore, the installation process is performed quite quickly and simply.
As with any material, the sandwich panels have their drawbacks:
- bad cut off
- suitable only for smooth surfaces,
- due to the thickness of the material steal a lot of space.
Nevertheless, for those who want to independently perform the work as much as possible and quickly - this is the perfect material.
In the assortment of most construction stores sandwich panels are presented in a wide palette of colors, so many interior solutions are quite a lot.
Required tool
In order to make slopes from the sandwich panels, you will need:
- stusl
- metal hacksaw,
- putty knife,
- screwdriver,
- pistol for liquid nails or construction foam,
- construction stipagler.
In addition, you must purchase a film that closes the floor under the windows. First, it will protect the floor from pollution, secondly will provide the working area so as not to store the tool on the windowsill and do not scratch it.
Depending on the destruction, it will take a putty. Finishing work is performed only after the finishes of the slopes of sandwich panels, but at the initial stage there should be large holes and align the surface. In addition, there may be wooden bars of minimal section.
Methods of decoration of slopes Sandwich panels
Specialists use three basic technologies:
- montage on the foam
- installation on liquid nails,
- installation on wooden bars.
Installation on the foam is the easiest option. To do this, buy a sandwich panel with a rigid frame. The procedure looks like this:
- dimensions are removed
- cropped strips frame,
- collected frame
- it is fixed in the strut between the windowsill and the upper slope,
- cropped panels,
- next they are inserted into the frame.
At the beginning there are two side slopes, and only then the upper one. Before placing the design of the foam, you need to check the slopes and set the struts so that the foam foam does not shift the frame.
For this method, only two-layer sandwich panel is suitable. At the same time, to increase the adhesion before spinning the inner surface of the panels and the wall of the house should be treated with water (from the sprayer or conventional tassel).
After a day, foam will become and it will be necessary to cut it. After that, decorative linings are dressed. Some masters do it immediately, but it does not meet the technological requirements.
The huge advantage of this method of finishing the window slopes sandwich panels is that parasites are not breeding in the mounting foam, it is resistant to any stimuli, both natural and chemical. Therefore, apply it is advisable to work with wooden windows.
Liquid nails are suitable if the surface of the walls is preserved quite well. They allow you to do without a frame and mount panels directly on the wall. This method is relevant for high windows, where the abundance of additional plastic spoils the appearance. Work is done as follows:
- remove the sizes
- crop panels
- make pre-fitting
- align the wall (to confuse more or recycling),
- glue panels.
The first thing is glued to the top panel, the sides are adjusted already under it. After performing the work, two unsolved tasks will remain:
- seams in the places of adjustment,
- open end part.
The seams are cleaned either by the usual putty under the color of slopes, or (if the color of plastic is white) silicone. Recently, for these purposes, also high-quality acrylic paint is used, which is similar to the PVC coating on the texture and creates a harmonious appearance.
The end part is enough to shock. If the windows occupy the entire area of \u200b\u200bthe wall, it is very impressive to paint it into white, while, the panel sandwich should also be white. More orthodox way - plating wallpaper.
In order to reduce the consumption of foam when installing complex, strongly destroyed slopes, use wooden bars, which serve as the basis for fastening the frame. This technology is:
- dimensions are removed
- cropped beams
- of them are going to a rectangle,
- sandwich panels are sewd to it by construction panels.
- cropped panels and inserted into the frame,
- foam is blown away,
- after 24 hours, decorative lining is cut off superfluous and mounted.
Such window sluts from the panel sandwich are still resistant to mechanical damage. It is best to use a three-layer panel, since the two-layer does not have sufficient rigidity for this design. But it is not fundamentally.
Sleeping panel sandwich do it yourself
In fact, the production technology of the sandwich panels is quite simple. If desired, they are easy enough to make themselves. At the same time, the appearance of the design, the materials used and their physical properties will be driving only from you.
To work, you will need the following inventory:
- wooden or metal hacksaw
- pVC panels or wooden siding
- pistol for liquid nails,
- polyfoam (no less than 2 cm in thickness).
Collecting slopes at home, it is possible to immediately make monolithic panels. This is relevant for the houses of the old building, in which the width of the slopes reaches from 0.4 to 1.5 meters.
The first thing is measured and cut off the foam, the material itself is insulation, so there is no need to use minvatu or its analogs of necessity.
Next, another interesting point opens. Wooden siding is quite expensive and far from everyone will have to taste, therefore, on an industrial scale, such slopes are not produced. But connoisseurs of real wood can replace the PVC surface to siding. Materials glued with liquid nails.
With plastic, work passes exactly. It is advisable to choose the widest possible panels so that the slopes are seamless. If it does not work so much, and I still want to see the design one-piece, the solution is a frame with a tension PVC film. A rectangle for the size of the slope is collected from the profile for drywall. A foam is inserted into the middle, and the PVC film is tensioned from the front side. In addition to the material itself, the construction hairdryer will also be needed.
Shields are mounted either on liquid nails or foam.
New comments
Add a comment
To send a comment you need authorize.
and where to buy such a sandwich panels, I can not find