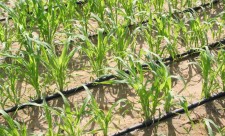
Polymer floor covering materials Floors
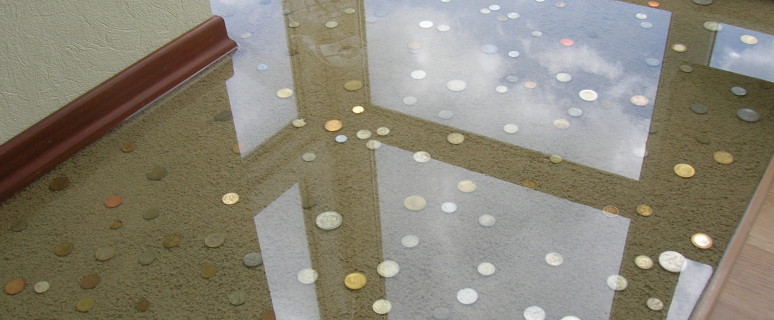
Polymer materials are often used to create floor coverings. Polymers are characterized by good strength and elasticity, wear resistance and durability. Despite the fairly high price, such coatings are quite popular due to its operational properties.
Content
Positive and negative qualities of polymeric materials for floating floors
We will understand in detail how the pluses have floor coverings of this type:
- The polymers are very elastic, in connection with which they are resistant to abrasion, shock loads and other mechanical effects.
- Materials of this type are not afraid of water and aggressive chemicals, so easy to care.
- Polymer coatings are fireproof, do not absorb dirt and dust.
- Their laying can be made independently.
- The strength of such floors is talking about the long service life.
- The surface of the polymer layer, despite its smooth species, is characterized by good anti-slip qualities.
- Such materials look aesthetically, can imitate various surfaces: water, stone, tile, wood, etc.
Along with the advantages, polymer coatings for concrete floor have a number of shortcomings:
- The high price for polymer flooring for the floor is one of the first drawbacks that the consumer draws attention. Such a floor will be on the pocket not everyone, but the quality and durability of the finish will pay off all costs.
- In the construction market you can find polymers of the budget class, but such materials are very quickly losing a decorative look. Under the action of sunlight, the coating fades and acquires yellowness.
- The liquid polymer floor requires careful preparation of the base. The concrete screed must not be just perfectly smooth, but also very strong.
- If there is a desire to change the floor covering, dismantle the bulk polymer layer will be very problematic. A simple variant will be the laying of the new floor on the already existing one.
- Before mounting a polymer flooring for the floor it is very important to take into account the humidity and the temperature of the base.
Types of polymeric materials for the floor
Polymer coatings are available on sale various forms. They are slab, rolled and mastic. The first two species are usually used in the construction of residential buildings, and mastic polymers can more often meet in industrial or public premises. The reason is that the mastic is more resistant to wear and adversely surrounding factors.
Rolled coatings
Rolled outdoor coatings include various types of linoleum:
- Polyvinyl chloride linoleum is considered the most common type. It is undoubted consisting of one or more layers, and may have a felt or polymer base. The material on a porous polymer base has good heat and sound insulation properties, so it can be mounted directly to the concrete tie. Other types require preliminary laying of additional layers. The multilayer linoleum is beneficial from one-layer in its strength and wear resistance.
- The second type of linoleum is alkyd. It is produced by applying alkyd polymers on a layer of jute fabric. The polymer also includes vegetable oils and certain fillers: cork and wood flour. The production of such a coating is considered the oldest technology, but on the technical and operational characteristics of the alkyd linoleum exceeds the polyvinyl chloride analog. Such an outdoor coating can most often meet at the facilities of the transport sector.
- The colloquiline linoleum is manufactured on the basis of nitrocellulose supplemented by various mineral impurities. This is a single-layer material with poor color gamut represented by red and brown tones. To date, such a coating is used infrequently.
- Rubber linoleum is a two-layer coating. Its front side is synthetic rubbers painted in any shade. The structure of the lower layer of material includes the used rubber, bitumen and a small percentage of synthetic rubbers. To make the coating heat-insulating properties, the lower layer makes porous. Such a linoleum can most often meet at industrial facilities, in buildings with increased hygienic requirements, in rooms with high humidity.
Polymer floor coverings are not only rolled, but also slab materials. Such tiles are made from synthetic polymers and additives: plasticizers, fillers, dyes. For technical properties, slab coatings are very close to linoleums and differ only in the format. It is more convenient to use them in residential areas, where from elements of different forms, colors and sizes, you can create interesting ornaments and drawings.
Monolithic floor coatings
Monolithic polymer coatings are created from mastic materials. They are applied to the base in liquid form, and then harden for several days. The result is a smooth, smooth, seamless layer. Mastic coatings after drying acquire good strength and wear resistance, they are not afraid of shock loads, the effect of chemicals, high and low temperatures.
Seamless polymer floors are made from several types of materials:
- Methyl methacrylate mastics are characterized by rapid solidification, it is possible to work with such compositions even at low temperatures. The finished coating is characterized by high strength and hardness, as well as resistant to scratches.
- Mastics on epoxy based on their strength characteristics are not inferior to methyl methacrylate mixtures. In addition, there are almost no aggressive chemicals scary with epoxy coating, be it alkali, acids or solvents. Such coatings can often be found in the rooms where high humidity is present and there is a risk of contact with chemicals.
- Polyurethane mastic is considered no less durable. Their distinctive feature is large elasticity. Even with strong bending, the dried polyurethane will not break, does not crack and does not crumble. Like epoxy formulations, polyurethane coatings do not react with chemical environments. The elasticity of the material makes it particularly stable before shock loads and mechanical effects. Such gender is often used in residential premises, no household damage can affect its wear resistance and durability.
- Cement-acrylic coatings are made of dry mixtures. Different with durability, strokes resistant and temperature fluctuations.
The price of polymer flooring for floors will largely depend on such factors:
- value of material on the market;
- room area;
- floor layer thickness;
- payment of services attracted professionals.
Pouring polymeric sex with his own hands
Preparatory stage
- As a rule, polymer mastic applies to a concrete basis, but it is important to understand that the screed must be even and durable. If it does not comply with the declared requirements, concrete is needed before applying the polymer. For this, the working surface is well examined, trying to find defects. If there are protrusions and bugs on the basis, they are cut by a grinding machine or any other suitable tool. Pits and protrusions are filled with a concrete mixture consisting of sand and cement. Ingredients ratio: 1 part of cement on 4 parts of sand.
- If there are too many flaws on the surface, and you do not want to spend time on the seal of each crack, it is easier to lay a layer of high-quality and smooth cement screed.
- When the screed dry, it is covered with primer deep penetration at least twice.
- Before applying mastic, you need to wait for the time until the primer is dry. As a rule, it takes at least 4 hours. It is impossible to start work before work, since the moisture content of the concrete base should not exceed 4%.
Laying thin layer polymer
In rooms where the floors do not experience significant loads, can be used for finishing thin layer polymer coatings. In this case, the mastic is applied to the concrete surface as an ordinary paint. The dry mixture is bred in a liquid and stirred by a construction mixer or a drill with a nozzle. Mastics are applied to the base with roller. It is dipped into the solution, remove the surplus about the edge of the tank, after which the roller is crossed by a small section of the floor.
The consumption of material in this case will be small, since the polymer layer on the floor is quite thin. On 1 m² of the area will take about 0.5 kg of substance.
Leaving the floor to dry, it is important to prevent dust from entering into another entrusting coating. At the same time, the room is desirable to provide good ventilation.
Creating a bulk floor with a polymer coating
The bulk floor is considered a universal option, it can be found much more often than thin-layer or high-filled floors. Mastics in this case are prepared in a large volume, kneading at least 25 liters of solution. Components are also stirred using a building mixer or drill with a nozzle.
The prepared mass is poured into the floor and smash with a special rubber mop, trying to create a homogeneous and uniform layer on the surface. Then, even for raw coating, conduct a needle roller. The needles, piercing the thickness of the solution, release air bubbles from mastic. If you neglect such a procedure formed in the drying layer of the cavity negatively affect the quality of the floor, its operational characteristics.
The device of a high-filled polymer floor coating
Mastic, from which a high-filled coating is made, consists of epoxy polymer and sand, and the sand occupies at least 70% of the volume of the substance. The main properties of such floors are high strength, the ability to transfer strong loads, long service life.
The high-filled coating is placed in two methods. The first method is carried out like this:
- the working surface is first coated with a uniform layer of epoxy polymer;
- then the raw polymer is falling asleep by quartz sand and leave until complete froze;
- when the solution hardens, the surplus of sand is eliminated with a vacuum cleaner;
- then the gender is again covered with a layer of polymer and give it to dry.
The second method provides for mixing two components, followed by applying the prepared mass onto a concrete surface. Prior to the end of the polymerization, such a floor is treated with a grouting machine, and when the solution completely freezes, the gender is once again aligned with a mosaic-grinding tool. The final stage in creating such a coating is its lacquer.