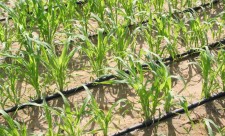
Proper connection of electrical wires: crimping or soldering with their own hands Lighting,Useful advice
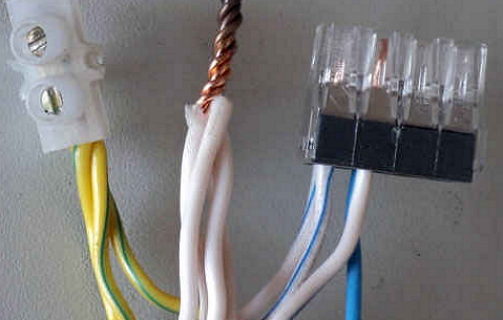
Installation of wiring in an apartment or a cottage involves connecting wires of junction boxes and shields. From how correctly all the compounds are fully implemented, the safety of the power grid and its trouble-free operation depends.
Content
- Methods for connecting electrical wires
- Feature to use terminal blocks for connecting electrical wires
- Use spring terminals for connecting electrical wires
- Conductor connection with Poll Siz
- Pressing sleeves
- Welding and soldering electrical wires with hands
- Wire connection with simple twist
- Clamp type "Walnut"
- Using a bolted connection for connecting electrical wires
Methods for connecting electrical wires
Electrical installations use the following wire connection methods:
- twist;
- soldering;
- with the help of terminal shoes;
- crimping;
- with bolts;
- plastic sisami;
- "WAGO" - spring terminals;
- "Nuts" from plastic.
The choice depends:
- from the material live wire (cable);
- from the operating conditions of the power grid (outer or internal wiring, hidden or laid in the open);
- from the cross section of the connected lived;
- from quantity lived in one connection.
The connection of the wires of the junction box must be completed in such a way as to ensure reliable contact and avoid heating lived. Your attention overview of the current connection methods listed above.
Feature to use terminal blocks for connecting electrical wires
The terminal block consists of a plastic case, brass or copper sleeve with thread and screws located on both sides.
Such a device allows you to:
- save on electrical equipment: Terminal block cheaper than other connectors;
- securely connect the wires;
- compound lived from heterogeneous metals (copper with aluminum);
- reduce installation time.
Disadvantages of terminal connectors:
- unfortunate for connecting more than two conductors;
- difficulties during the attachment of aluminum lived: with excessive tightening of the screw, the metal may be alleged;
- understandability of use for stranded wires.
Terminal pads for connecting electrical wires
The connection of the electrical wires in the terminal block is performed as follows.
- The cables are partially removed external insulation and the veins are broken. The length of the bare conductor depends on the size of the terminal.
- The length of the wire section is checked without isolation, for which it is necessary to unscrew the screw of the terminal and enter the opening in the hole completely. Excessive cut by the windows.
- To improve contact, a copper wire is fired.
- The connecting cores are alternately entered into the terminals and clamp into several receptions.
- The reliability of the connection is checked.
Tip: In order to remove the insulation without damaging the core, it is recommended to use a special tool. In the absence of such a sharp knife, only the surface layer of insulation in a circle is caught, after which the wire should be bent along the cut line. After rupture, insulation is removed with a slight movement of pliers.
Use spring terminals for connecting electrical wires
The compound of conductors with spring terminals is carried out by means of springs, pressing the contact plate to metal of the veins. The mechanism is activated by a special lever.
Wago Terminal Connector
The technology "WAGO" has several advantages over other installation methods:
- allows you to connect aluminum wires with copper;
- can be used to connect more than two livers;
- allow you to switch the wires in small junction boxes;
- installation is performed qualitatively and in the shortest possible time;
- conductors' veins are not damaged;
- after installation, it is possible to check the integrity of the chain using the probe of the device or the indicator through the hole in the housing.
In order to connect the wires using the "WAGO" terminals, it is necessary to remove the insulation so that the bare veins can not be seen, after which we introduce the veins in the connector's jacks and press the levers until it stops.
NOTE: There are spring terminals "WAGO" of reusable and one-time application. The latter, if necessary, repair the connection is cut, after which new connectors are installed.
Conductor connection with Poll Siz
PPE Cap Hounds to connect clockwise
Abbreviation SIZ means "connecting insulating clamps". Connector design is a spring located in a plastic case. The spring reliably holds the veins together, which creates reliable contact. The advantages of this method:
- the possibility of marking wires with colored caps: Phase cores connect to the Phase, "zero" - blue or white, "land" - yellow or green;
- fire protection: Connector hulls are made of non-combustible plastic.
Important: The connection of copper and aluminum wires using PPE is not allowed.
Pressing sleeves
Connection live conductor sleeves
The method lies in the fact that the veins released from insulation wear a metal tube (sleeve), which is crimped with press clamps. As a result, the conductors are tightly connected to each other. Connection location isolate.
Important: The connection of aluminum and copper conductors is allowed only to be performed using specially intended for this sleeve.
Welding and soldering electrical wires with hands
Welding or soldering technology allows you to get a reliable wire connection.
The disadvantage of this method is the inability to monitor the integrity of the network after installation and insulation, as well as the maintainability of such a compound. In addition, the burner for soldering with your own hands is dangerous when used.
Alternative to soldering of wires is their welding. The process involves the use of the welding machine.
Wiring technology
When connecting copper wires in this way, it is recommended to try out the transformer for the brassing of the copper wires with your own hands before proceeding to work. It is important to know that the melting of copper is carried out at a temperature of 1080 ° C, but already over 300 ° C, this metal becomes fragile.
In the absence of a special soldering device, use the conventional inverter welding machine. The phased process of welding wires is as follows.
- From the ends of the wires, insulation is removed for a length of up to 10 cm.
- The veins of the connected wires are tightly twisted with each other. As a result, a twist should be formed about 5 cm.
- The "mass" cable inverter joins the twist closer to its beginning.
- The current force adjustment knob is set at a position from 30 to 90 A (at a voltage of 12 - 36 V): the value is selected depending on the cross section of the wire and their quantity.
- A coal electrode of the welding machine briefly (no more than 2 s) touches the twist so that the arc formed. As a result, a welded monolithic compound is formed on the tip of the twist.
- After complete cooling, the connection is insulated with a shrink tube or sticky ribbon.
At the ends of the veins, connected by welding, a monolithic alloy is formed
Connection of electrical wires soldering
Copper wire soldering is an old, tested way to obtain a reliable electrical connection. Technology allows you to mount monolithic and stranded wires of various sections. In one connection there may be several conductors.
Work is performed according to the following technology.
- From the ends of the connected conductors, insulation is removed by a special device (approximately 5 cm).
- The veins are tightly twisted with each other manually or with the help of pliers (depending on the number of lives and their sections).
- The twist is processed by flux or rosin. It is necessary to improve the quality of the soldering.
- On an open fire (a gas burner or a gasoline soldering lamp is used) a glass soldering iron (Fortorka) has been heated. Bowl of Futorts to the edges is filled with tin-lead soldier of the Mark 30, Po 40 or Po 61.
- Solder is heated to the state of the yield.
- A twist is briefly (up to 1 second) fully dipped into the Fortorka bowl, as a result of which the solder must completely cover the bare cores.
- After the natural cooling of the twist is insulated with a sticky ribbon PVC or a plastic cap.
Important: Wiring solder should be performed in protective glasses and tarpaulin mittens. During operation, it is necessary to comply with the rules of fire safety.
Copper wire solder is done as shown in the video.
Wire connection with simple twist
Conducting wire connections in a junction box for low-power electrical networks can be implemented by a simple twist without applying additional fixation tools. It is important that the scroll step is as small as possible, and its length is at least 20 mm. It is connected in this way only veins of homogeneous metals: copper - with copper, aluminum - with aluminum.
It is not allowed to apply this method of installation in wet premises and in wooden houses.
After twisting, the connection of the wires should look like shown in the photo
Clamp type "Walnut"
For connecting wires with a cross section of 4 square meters. mm and more conveniently use the "Walnut" clamp. It is a pair of plates of special shape, which is pressed to each other with screws in the corners. Benefits of the method:
- simplicity of connection;
- ability to connect copper veins with aluminum;
- comparative cheapness of materials.
Important: "Walnut" clamp does not apply in junction boxes (do not allow dimensions). In order for contact to remain reliable, the screws must be tightened from time to time.
Using a bolted connection for connecting electrical wires
To connect large cross-section wires, as well as for mounting ground elements, a bolted compound is used in the electrical panel. The ends of the wires freed from the insulation are screwed into the thread of the bolt in the direction of the clockwise direction. The connection is pressed with a walker with engraver and nut, after which the bolt is isolated.
In conclusion, we suggest familiarizing yourself with the training video (master class with a specialist comments).