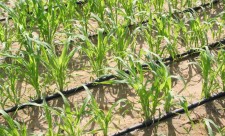
Machine for cutting foam with her own hands Instruments
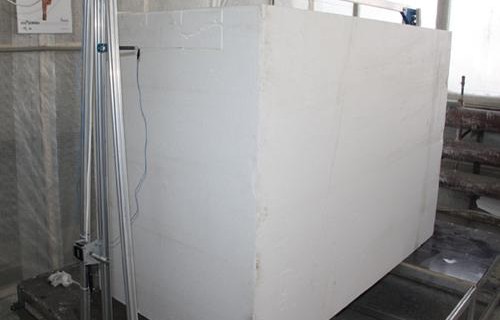
Polyfoam is a wonderful material used in many areas of construction and decor. With it, it is equipped with hydro and heat insulation, create decorative ceiling coatings, baguettes and more. With all its multifunctionality, it is also cheap. The only problem arising during working with it is cutting.
Content
Cutting foam: Machine with your own hands
Cut foam on your own so to get clean and even sharp is extremely difficult. It crumbs and bursts, if applied to the saw, even the blade or razor do not solve the problem.
A hot metal can be released, but how to use it at home? Describe homemade foam cutting machine!
Method number 1.
To carry out this idea, you will need:
- the table is better if each of its parties will not be shorter than 2 m;
- metal springs with low current resistance;
- transformer transforming current with 220 volts;
- strings with high resistance, if there is an old heater, remove from it.
Also need a string height regulator. Use a couple of beams as it. Between them will move the cutting string with the holder.
The transformer is not necessary in each case. It depends on what material the string is made. If it is chrome - permissible is considered to be a current of 220 volts. But, working with such a discharge, the safety rules should be clearly followed, otherwise the case may end it sad.
If you work with a discharge of 24 volts, there is no danger to life and health. He just do not feel, and when defeated, it is necessary to simply wash the injured water.
It should also be remembered that when cutting a foam plate with a hot metal, toxic pairs are distinguished, so it is necessary to use a protective mask at mandatory, and to ventilate the room well, otherwise the poisoning will be provided. And best of all, in general, working on the street, but it is possible if there is a private courtyard.
In order to be easier to assemble from the above materials, the machine for cutting foam, below shows a schematic drawing:
Method number 2.
In the absence of a suitable table, a DSP sheet, plywood, board, is quite suitable for the device.
Homemade machine assembly sequence:
1. Attach the nichrome wire to the springs, the springs are put on the screws M4, and they, in turn, screw them into special racks.
2. Press metal racks in advance in the roof of the table, the chipboard plate, or any other surface chosen as a base. The height of the rack and the thickness of the base depends on the needs of the machine owner. If the plate thickness is 1.8 cm, and the rack is 2.8 cm, then the screw will not pass through the screw stream, and the foam of 5 cm thick can be chopped with a thickness of 5 cm.
3. If in the future you need a thicker cutting, then the short screws will need to be removed and screwed into their place long.
4. For pressing, drill at the bottom of the hole. Its diameter should be less than the diameter of the rack per millimeter. Stands lend the hammer into the holes, but before that, to make it easier for this procedure, pass the sandpaper on the sharp edges of the ends.
5. Before screwing the screw in the rack, drink the groove under its hat itself. To carry it out, clamp it with a screwdriver, and under the head attach a thin file and turn on the rotation. This groove is needed in order to fix the wire in one position, which can otherwise move when adjusting.
6. So that the wire does not have saved, lengthening because of heating, attach it first to the springs, and they are already to the screws.
7. After all the fasteners are ready, secure the nichrome wire. That the contact between it and the conductive wire is reliable, use the method of fastening the "twist with compression". The copper wire must have a cross section of at least 1.45 square meters.
8. Remove the isolation from the end of the wires by about 2 cm. Copper conductors turn on wire in those places where it is attached to the spring. The end of the wire, holding the pliers, wrap around the conductor. Thanks to such a winding, the contact of the wire and conductive wire will have a large area, and when the machine will earn, the connection site will not be late.
9. To make the ability to adjust the thickness of the material cutting, make the conductive conductors in the form of a loop. And so that the wires are not confused at hand while using the machine, do it at the base of the hole, skip the interfering segment through them and attach to the back of the surface with a bracket.
10. Wires are best folded together and twisted in the form of a non-nominal harness. So they will not be confused.
11. At the ends of the wires, solder the clause terminals to connect them to the power supply.
The device described over the instructions described above will be enough to use at home. In addition, it is possible to use it as a machine for curly cutting of foam.
Useful advice
During the cutting, the speed of the material should be medium. If you move the foam very quickly, then it will definitely reappear as when cutting the saw. If on the contrary, move it very slowly, the edges of the cut figure will be melted.
If the foam is required for insulation of the house during construction, then it is better to purchase thicker. Because of the simple manufacturer and small demand, such a material is much cheaper than thin.
If in the attic from the Soviet times, a stereo-magnetophone "Lighthouse", then the transformer does not buy, and take it from it. It is just suitable, because Submits 24 volts voltage.
In the case when the work is carried out in the absence of electricity, connect with each other three kroons of 9 volts, and use them. Thus, the device will be able to function 30-40 minutes.
But apply auto accumulators for this purpose is categorically prohibited. Despite the low voltage, they have a very large current strength that can burn the string and it simply burst. It is with good scenario, and with a bad - sprinkle with a hot metal.
The choice of foam for the arrangement of thermal insulation
There is a special foam plastic intended for the insulation of facades. On the package, there is usually an appropriate marking in the form of the letter "F". It has high, in comparison with the usual material, density and resistant to mechanical effects. It springs well, thanks to which it is badly breaking.
When cutting the foam, it should not be installed below 50 mm for thermal insulation. The fact is that a thinner material will not be quite effective, and when wetting it all will lose most of its wonderful properties. With high humidity, such thermal insulation will be permeable for cold air, as well as ordinary brickwork.
Use the mineral wool slab as an additional material for thermal insulation. In addition to the mentioned properties, it has another important advantage - in the event of a fire will not be lit.
Machine for cutting foam, video: