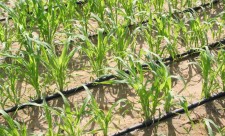
Grinding machine with their own hands Instruments
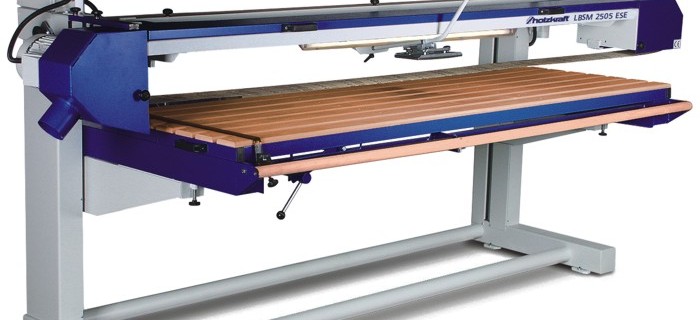
When performing any construction or repair work, there is a need to align the surface of the parts used. To date, there is a large selection of grinding machines and machines that allow you to get the necessary result. Consider more in detail the principle of operation, the method of manufacturing and using a grinding machine.
Content
Features and types of grinding equipment
The purpose of the grinding machine is the finishing processing of parts from wooden or metal material that has passed a certain preliminary training. In the process of grinding from the surface of the metal products, a thin layer of material is removed, so that all irregularities are removed. There are three types of processing performed by metal machine:
- At the first stage of the processing of the blanks, their trimming is performed.
- In the second stage, surface grinding is carried out.
- The last stage provides for sharpening the tool.
The grinding machine for metal is classified into several categories:
- flatShelifice machines that handle the plane of the product with increased accuracy;
- circular solid devices are used to work with cylindrical surfaces. Their peculiarity is that with the help of such machines, it is possible to grind not only smooth, but also intermittent surfaces;
- subscencylifish units that are used when working with long products, as well as with parts that do not have holes in the center;
- details of large sizes are treated with planetary machines.
The grinding machine on the tree is used to complete the surface alignment of the material. Using such a device, products made of wood material give an absolutely smooth surface, the existing irregularities are removed - various recesses, influx of primer and varnish, and also get rid of sowers.
Also, the grinding makes the roundabout and performs the inner grinding. Such an effect is achieved due to the presence of a cutting abrasive tool, which is equipped with the machine. To align the surface of the wood apply:
- tape;
- drum;
- disk machines.
Scheme of grinding machine:
Device grinding machine
In the design of the homemade grinding machine for wood processing are the following details:
- This design form a countertop and a desktop on which the fastener of the cutting tool is carried out. The table can be enshrined in relation to the tabletop in various positions, depending on the technological necessity.
- The machine is equipped with a mechanical drive, the purpose of which to ensure the movement of the desktop in the desired direction.
- Over this table is a working tape. Its regulation is carried out by means of a screw device.
- The grinding process is performed under conditions of the transverse movement of the table and moving in the longitudinal direction of the iron, with which the tape is pressed against the part being processed.
- In motion, the tape leads an electric motor.
- Also, the machine is equipped with a dust receiver, which receives waste converted in the grinding process.
When choosing grinding mode, it is necessary to focus on the properties of the material and its roughness. Based on these characteristics, choose:
- feed rate;
- skin grain;
- the level of effort to which the tape must be pressed to the workpiece.
The grain of the skins is determined on the basis of the properties of the material hardness and the desired roughness of its surface. The force used for pressing the tape and the feed rate is mutually determining indicators. If the tape is pressed with a small force, and the feed will be carried out at a fairly high speed, there is a chance that grinding will be fragmentary. That is, some places will be missed and not processed. In the case of the opposite situation, with a large power of pressure and insufficient feed, the material turns on.
Important! A prerequisite for the procedure for installing the tape is to check the quality of its gluing. Refrigeratedly connected, assigned tapes are not recommended to be applied, since this will negatively affect the quality of the product being processed. The adjustment of the tension tape is carried out using a tensioning roller by moving it. It is very important to determine the correct level of tension. An overly stretched tape can break, and the weak tension causes the slippage of the tape for pulleys and its heating. To properly install all the parameters, you need to focus on the strength of the tool that performs cutting.
Principle of operation
Grinding on a machine having a manual feed can one worker. Grinding procedure is performed as follows:
- The worker moves the processed part longitudinally with respect to the cutting tool and turns it around the axis. Thus, the entire working surface is in contact with the ribbon.
- The condition that provides high-quality grinding, is the pressure regulation exerted on the iron handle. As well as the speed with which the table moves.
- To perform grinding on a machine having a mechanical feed, two employees are required. One places the part and adjusts its location on the table surface. The second employee takes ready-made products and follows the quality of grinding.
- It is impossible to handle the details using a machine that have significant defective surface changes and different thicknesses.
How to make a grinding machine yourself
The cost of the grinding machine is high enough. A more affordable way to obtain such a home tool is an independent manufacture. The materials necessary for this are quite affordable - this is the engine, rollers and a bed.
- The engine can be taken from the washing machine. It must have a capacity of 2.5 to 3 kW, and the number of its revolutions per minute should be 1,500.
- When using a grinding ribbon, the speed of which is 20 m / s, the drums used must have a diameter of 20 cm. When these conditions are met, the engine will have sufficient turns and the need for a gearbox will not arise.
- For the manufacture of the bed, the thick fragment of the iron size of 500x180x20 mm will be required. To one side of the bed will be fixed the platform with the engine, this side must be trimmed with a milling machine.
- Next, in the end of the cut part, you need to drill three holes and with bolts to perform the site mount.
When choosing the desktop parameters, you should consider the length of the table. The longer the work surface is, the more technological capabilities will be introduced to the processing of parts in the process of work. In order for the surface of the workpiece to be grounded at a high level, the length of this product should be less than the size of the desktop or have similar parameters with it. If the processed part exceeds the specified parameters for its length, it will be extremely problematic to achieve a good result.
- On the bed, we place the engine. At his shaft fix the drum. The second drum is placed so that it can rotate freely.
- That side of the table, where the second drum is located, should have a small bevel. This is necessary to ensure a smooth touch of the table surface ribbon. For the manufacture of these two drums, the chipboard is quite suitable. The manufacturing process provides for the following actions:
- from the chipboard you need to make blanks, cut the parts with a size of 200x200 mm each;
- then these billets are collected in a package of 240 mm;
- these parts are folded on the axis and are pulled to reach a diameter of 200 mm.
- The diameter of the drums along the edges should be about 2 mm less than in the central part. This is necessary in order to arrange the grinding tape in the central part of the drum.
- The tape should have a width of 200 mm.
- The width of the emery material is 1 m, from it you can glue 5 such tapes. Bonding should be embarrassed, pre-placing the dense material.
- On the rollers it is necessary to pull the rubber with a width of 30 mm. Suitable ordinary rubber from the bike.
- Ready. We built a grinding machine. The technical characteristics of the self-made product are not inferior to the factory unit, having a significant advantage in price.
On such a machine, in addition to alignment of wooden and metal parts, you can sharpen various tools - knives, axes, chisels. Also another positive property of this tool is the ability to perform the processing of parts with a curved surface.
Conclusion
The grinding machine makes it possible to get an absolutely smooth surface of various wooden and metal parts. Such a tool will necessarily need when performing repair or construction work. The cost of grinders in the market today is high enough. An alternative option will be the manufacture of grinding machine with their own hands. Materials that will be required for this are sufficiently available. The technological process, subject to studying the procedure, will not cause difficulties.
The manual for the manufacture of the machine is also represented on video: