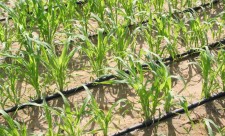
Welding inverter welding. Features of work Instruments
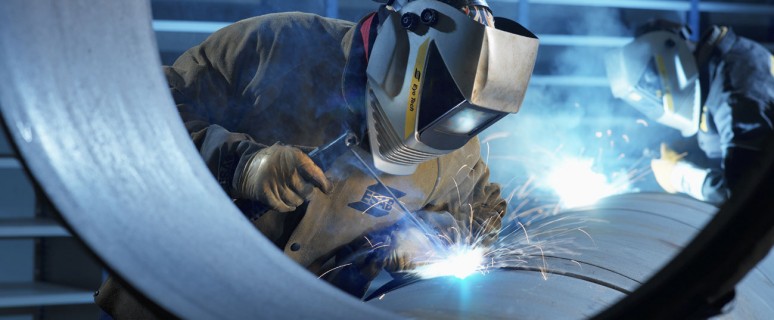
Today, most types of welding work has become easier thanks to the appearance of a welding inverter. This apparatus can be safely called progress in the field of electrical welding. It is a small-sized installation equipped with a transformer and generating a high force current, which serves to create and maintain a welding arc. About the device, nuances of work, advantages, shortcomings of this unit, we will describe further.
Content
Characteristics of welding inverters
When welding the welding inverter, a stable welding arc is formed between the metal and the electrode. With high temperature, the material is melted, and then freezes. As a result, there is a pretty durable seam, reliably connecting all the details of each other. With the help of arc welding, more than 80% of industrial welding works are performed.
The welding machine is powered by an inverter from an industrial or conventional AC voltage network in 380 or 220 volts. At the output, it creates a reliable current, the necessary power and voltage. The welding inverter solves the problem of lack of current obtained from the usual home electrical network. After all, as it is known, its voltage is 220 volts, the frequency is 50 Hz, and this is not enough for the welding works by the ordinary apparatus. The inverter is capable of functioning under such conditions, it converts current and voltage, supports the welding arc and changes it in wide ranges.
The term "inverting" refers to a DC conversion to variable. It was from this that the device name appeared.
The device of the welding inverter and the principle of its operation:
- When the device is turned on, the voltage obtained from the network hits the primary rectifier.
- Next, the alternating current is converted to a constant and served in the inverter unit. This part of the apparatus is the main one. Here the current returns again from constant to variable, but its frequency is no longer 50 Hz, but several tens of kilohertz.
- Such high frequency voltage enters the transformer. Then the voltage decreases, and its force, on the contrary, increases. And served on the secondary rectifier.
- At this stage, alternating current turns from the variable to the permanent and the cable is supplied to the welding electrode.
- Regulate the order, stability and proper operation of the control blocks of the device based on microprocessors.
Advantages and disadvantages
The welding inverter of argon-arc welding has the following advantages:
- Small weight.
- Compact size. When working with the instrument, high-frequency transformers are used, having smaller dimensions compared to low-frequency.
- CPD when working 80-95%.
- Stability and practicality. The operation of the voltage voltage tool in the network has practically no effect.
- Easy and ease of operation. There is a mode of operation for beginners.
- Reliable welding arc. The current issued by the instrument has a low ripple. It can be adjusted depending on the type of work performed.
- Seam during welding turns neat. When working, the metal is practically not sprinkled on the sides.
- Depending on the type of material with which the welding arc is needed to be operated. It can be long or short.
- It has a wide range of settings.
- You can use any type of electrodes.
- High quality work performed.
- Efficiency in the consumption of electricity.
- The tool is safe when working, as there are elements of built-in overheating and short circuit. Equipped with automatic shutdown system.
- You can perform programming welding.
There are some shortcomings:
- High tool cost. However, the price of apparatus is reduced every year. The welding inverter is becoming more and more accessible to home use.
- The tool often emerges with the management board and processor.
- Details of the device have a high cost. It increases the price of repairing the welding inverter.
How to choose a tool?
Depending on the operating conditions of the tool, you can choose a household or professional model. Differences are in the duration of work. So, professional welding inverters are designed for eight-hour work. Household can function continuously for no more than 20-25 minutes. Then they need rest for an hour.
For home needs and if there is a voltage in the network 210-220 volts, it is enough to buy a tool with a maximum welding current of 160 A. with a lower network voltage better to purchase a device for 200 A.
The strength of the current 200 A allows to cut the metal with a thickness of 4-5 millimeters. Therefore, if it is necessary to work with a thicker material, the power of the acquired tool must be higher.
The most popular manufacturers of devices are considered:
- "SELCO" and "HELVI" (Italy).
- "Gysmi" (France).
- "POWER MAN" (Korea).
- "FUBAG" (Germany).
- "Torus" (Russia).
Tips for work with a welding inverter
- Observe safety regulations. They are listed in the instruction manual.
- When working with the device, use protective overalls, as well as gloves and mask.
- Do not work during rain and snow. Do not operate the tool in conditions of high humidity.
- If the electrode does not flare up when working with the apparatus, then you can try to increase current strength.
- Do not knock on the tool surface. By this you can damage the coating of elements.
- If the item that needs to be processed is in an independent power supply device, then before work it should be deranged.
- Work with the device only in the temperature range, which is specified in the instructions.
- Keep a tool clean, far away from dust and dirt. This will extend the service life of its service.
- Do not allow metal dust when working inside the tool. This can cause a breakdown of the unit.
- Do not operate the machine when weakening cable contacts in contact slots. Any insulation disorder can cause sparkling and fire.
- Perform only the type of work that is specified in the instruction manual for the corresponding model. At higher loads, you can burn the inverter unit.
- If there is a voltage below 220 volts, malfunctions are possible during the operation of the tool.
- Do not store the tool in places with high humidity.