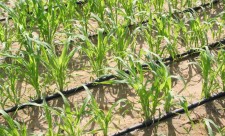
Technical characteristics of ceramzita Building materials
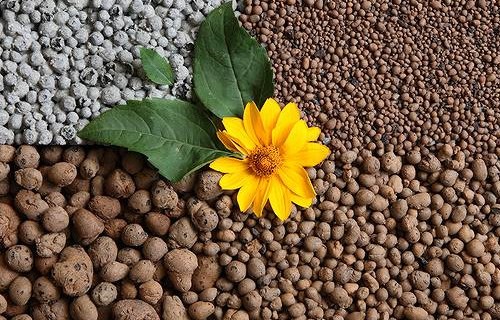
Ceramzite is a building material obtained by accelerated heating of clay raw materials, which can carry out the process of pore formation at a temperature in the furnace 1050 - 1300 C, 25 to 45 minutes from the start of heating.
Content
Keramzit is characterized by a sizernary, a form of grain, density and durability:
- Gravel - having oval shape.
- Crushed stone - has a multifaceted shape with corners and edges.
- Sand.
GOST 9759-76, fundamental paper compartment. It regulates the clamzite fractions: 5-10, 10-20 and 20-40 mm, the restrictions on the presence of other fractions in the base in the ceraims are indicated.
The table shows the data on the strength and brand of the clay filler.
GOST separates the produced clay filler by 10 varieties, in accordance with the density, from 250 to 800. Thus, the brand 250 is indicated by the clay filler, with a density of up to 250 kg / m3.
To determine the density of the ceramitis use dimensional containers. The average value of water absorption of clay gravel is from 8 to 20%. Existing technologies for obtaining clay are designed in full compliance with this GOST.
The indicator of its frost resistance is at least 25 temperature difference cycles from the minimum to the maximum. In other words, the service life of the filler is at least 25 years.
The thermal conductivity characteristics of the cerarmisit cannot always meet the requirements for low-temperature resistance, so before applying requires their careful examination.
The thermal conductivity of the ceramisite is determined by the amount and size of air pores, their humidity. The formation of the so-called glassy phase arising in the pellets may influence the decrease in this properties of the ceramisite.
The main properties of clay, its varieties
Ceramzit gravel
These are pellets with porous inside and surface mounted by high temperature. The lion's share of the produced clay filler in the Russian Federation is gravel.
As noted above, gravel has an oval form. Its surface is painted in a dark brown color, on a break, as a rule, almost black.
The clay filler is made in the form of peasant with dimensions from 5 to 40 mm. In addition to fire resistance, moisture resistance, it is different and the fact that it does not contain substances of the contraindicated cement. For the manufacture of clay filler, specialized equipment with a rotating stove are used.
Ceramzit crusp
Craftsitic crushed stone is obtained by crushing large pieces of foam mass of clay. Unlike gravel, it has an arbitrary, angular shape.
The production of the clay filler uses the natural properties of clay, namely the release of gases and the presence of a pyroclastic state. The transition to such a state of clay occurs under the influence of the maximum temperature. In this state, the melt is formed (the liquid phase of the aggregate state of the substance) and it takes place (boiling). At the same time, the ceramzite receives another property - gas-tightness.
Ceramzit sand
Production of claying sand is carried out in several ways: using a classic rotating furnace, mechanically using a vertical furnace in a boiling layer.
For the manufacture of clay sand, it is not always appropriate for the use of classic stoves. This is due to the fact that with such small grains, he simply does not have time to foam, so sand is obtained on roll crushers, grinding large pieces. The production of 0.5 m3 of sand is spent 1 m3 of finished clay. The second effective way to produce sand - firing in a "boiling layer".
The essence of this technological process is as follows: Pre-prepared clay crumb diameters from 3 to 5 mm is placed in a stove with a vertical chamber. The air under pressure is supplied to such a furnace and gas fuel is sprayed.
The combination of air and fuel at the specified modes allows you to move the solid crumb to the discharge state. The flow of sprayed fuel directly in the layer of clay raw materials performs its smooth heating and causes boiling (swelling).
The density of the ceramic sand is about 500 - 700 kg / m3. The technical requirements for claying sand are approximately the same, in comparison with the usual river. The content of large granules should be significantly larger.
Raw materials for production of clay
The basis for the manufacture of clay - grade clay, which relate to sedimentary rocks. These are shale, argillitis. The breed of this type is characterized by a complex mineral composition. They include quarters, swipes and other inorganic and organic compounds.
Basic raw materials for the manufacture of a clay filler is a montmorillonitic or hydropower clay. The admission of raw materials for the production of clay filler is carried out only after a thorough study of its composition, in particular, on the content of quartz.
Application
In many regions of our country, ceramzitobeton has become the basis for mass development. Its most effective is its use for the manufacture of blocks of brands 300, 400, 500. The strength of these blocks lies in the range of 5 to 7.5 MPa.
The properties of the ceramzite concrete provide simultaneous carrying out carrier and thermal insulation function. In multilayer structures, it is possible to use as structural ceramzite concrete and manufactured insulating concrete with a density of 600 kg / m3.
Studies have shown that the use of combined (structural and thermal insulation concrete) provides a decrease in material intensity and ensures the quality and reliability of such panels.
The ceramic filler with stamps 700, 800 is used to manufacture light construction concrete concrete, in particular, for the needs of bridge buildings, where one of the main tasks is to reduce the weight of the structures.
Easy mining of raw materials, relative simplicity of production, low cost of clay - all of this made it popular building material.