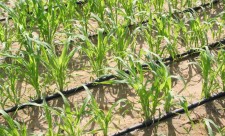
Grinding machine with your own hands Instruments
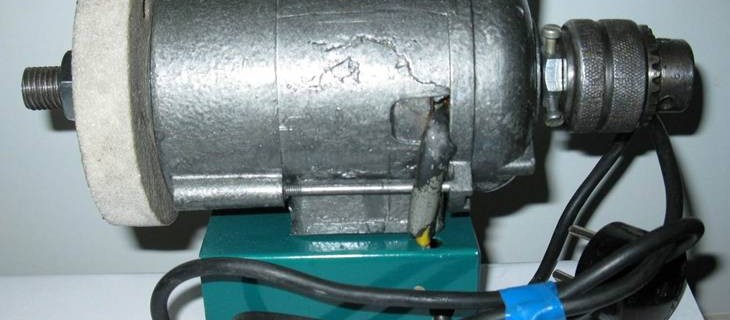
In the house there should always be in working condition Knives and scissors, and in the country the need for an acute tool even more: shovels, chips, braids, etc. Touch everything is manually - the occupation is tedious and unproductive. It is necessary to have a sharpening machine at its disposal. But this is not a cheap tool and therefore it is worth trying to make a grinding machine with your own hands.
Content
About the device of sharpening machines
The device of household sharpened obeys the following rules.
- The main details of the sharpening machine are the box and the electric motor fixed on it.
- On the ultimate part of the engine shaft mounted limbs, and on it - sharpening and grinding circles. On the sides, before grinding and sharpening circles there are columns with guides to adjust the horizontal supply of the tool being processed. The longitudinal feed of the stuffed part is performed manually: the part moves in the desired direction.
- Sharpening and grinding circles should be equipped with protective covers.
- A two-button switcher is installed on the housing.
- The mass of the bed must be such that sustainability sharpened.
- To reduce noise and vibration, the bed is equipped with rubber legs.
For the manufacture of a sharpening machine, you can use a conventional electric drill .
Functions of a sharpening machine
For domestic use, you need a sharpening machine of the universal type. Unlike a special, with the help of such sharpened, you can handle most of the home instruments. Electrical sharpened is used to solve the following tasks.
- During the drilling of thick metal, it often overheats and breaks the drill. It is impossible to work further by such a device, but it is still early to utilize it. With proper sharpening, the drill will last for a long time.
- For sharpening scissors, knives and other tools, a sharpening machine is required. This design is optimal for domestic use.
- For grinding metal surfaces with a felt circle.
- On the other side of the shaft, a cam cartridge can be installed for fixing the drills and, in this case, a sharpening machine will be used as drilling.
Criteria for selecting a sharpening machine
Choosing components for the design of a grinding machine, it is necessary to take into account the following technical indicators of the device:
- power: It should allow processing massive parts and tools (for example - an ax) without a significant reduction in the rotational speed of the electric motor;
- the diameter of the planting hole: it is taken into account for the manufacture of the equipment;
- the diameter of the sharpening and grinding circle is selected depending on the size of the parts being processed;
- rotation speed: it should not exceed 3000 rpm (better limit to 1500 rpm);
- the ability to adjust the speed of rotation is a convenient function required for processing different parts;
- mass - It matters when necessary to move sharpened.
How to make a grinding machine
In order to assemble a homemade grinding machine, you need to purchase an electric motor with a capacity of about 1 kW (this will be enough), as well as shaft, bearings and two pulleys.
Helpful advice: As an engine, an aggregate from the old washing machine can be used for sharpened.
Select the electric motor
From the old washing machine of the brand "Vyatka", "Riga", "Siberia" need to extract the engine. A starter and switch also come in handy. There may be a problem with the addition of a grinding stone: the engine shaft does not have a thread and does not coincide with a diameter with the size of the screw circle. The problem can be solved using a custom-to-adapter. The engine from "Washing" is low-power: within 100 - 200 W, but this will be enough.
Rotation frequency in 2700 rpm. And the specified power is the optimal parameters for a sharpening circle with a diameter of 150 mm. An increase in the frequency of rotation will lead to the destruction of the stone.
Pull the flange
The solution to this task is performed in stages.
- We prepare the drawing, which indicate the diameter of the engine shaft, type and size of the thread (if available) and the inner diameter of the grinding stone.
- On the lathe with the help of a specialist, you pull out the flange, the thread is cut on it, after which it is attached to the motor shaft.
- The flange is fixed by a bolt and nut.
Important: The direction of thread cutting the rotation of the electric motor shaft depends on the direction of the rotation of the electric motor. If the shaft rotates clockwise - a left-side thread is needed, if the other side is right-sided. Otherwise, the nut will be unwound and the stone will not hold on the shaft.
Determine the direction of rotation
The direction of rotation of the rotor of the electric motor does not always suit. To change it, in the asynchronous engine you need to switch windings. This is followed for this.
- The tester is determined which of the windings is a working, and which is starting. The resistance of the first is about 12 ohms, the second is about 30 ohms.
- Conclusions of the working winding connect with 100 V. connection cable conclusions
- One starting winding output is connected to one trigger output, and a short-term touch with the second winding output is made by the second output (it is convenient to use the relay). If the direction of rotation is correct - perform switching according to such a scheme.
- To change the direction of rotation, the conclusions of the launcher are changed by places.
- If there is no starting coil in the connection diagram - the direction of rotation is set by hand: To do this, you need to turn the stone in the desired direction immediately after connecting the power to the network.
Assembling a sharpening machine
The final assembly of the sharpening machine consists of the following steps.
- From the steel corners with the help of the welding machine, the bed is made.
- The electric motor with pulleys is screwed to the bed with screws and nuts. To prevent the spout of the nuts under the influence of vibration, engravers or additional nuts are used.
- From the corner is manufactured and a plane is installed, which regulates the slope of the stuffed part.
- The sheet metal is made and the protective casing is made. Its thickness should be 2-2.5 mm.
- The curtain is cut out of the plexiglas, which is fixed to the top of the cut-out in the protective casing by attaching.
- The starter button is attached on the bed. The network cable should pass aside from moving parts of the machine.
- After the assembly, a trial start and checking the work sharpened. At the same time there should be no strong beats of the sharpening stone and vibrations of the bed.
Important: It is necessary that a safe distance (minimum 10 mm) was respected between the grinding circle and plate of the workbench.
Using the recommendations given in the article, you can independently make a grinding machine, whose work will be the most positive. It is important not to forget about the safety technique and always work in protective glasses.
In conclusion, we suggest familiarize yourself with the video on which the designer will introduce you to another design of the grinding machine.