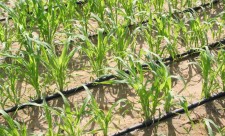
Laying of laminate on concrete floor Floors
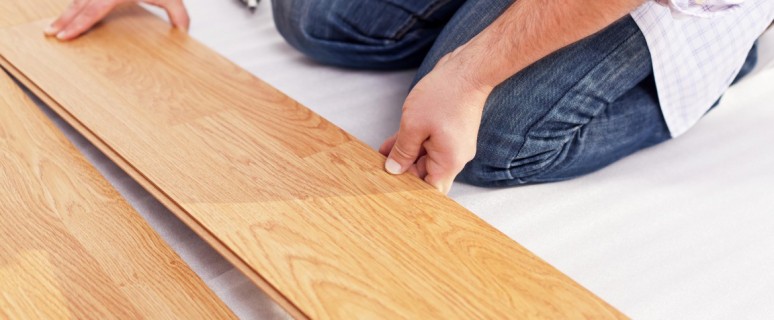
Laminate, you can shoot, the youngest material that is used for laying the floor. It has a lot of advantages over other floor coatings. Most of all, he is valued for having a relatively low price and is practical. At the same time, due to the variety of colors and drawings, this material has aesthetically attractive appearance and is suitable for lining almost any rooms. In addition, it can be laid on a wide variety of surfaces. Put the laminate on the concrete floor is simple enough. Therefore, these works can be performed independently. Tell me further.
Content
Characteristics of the coating
Externally, the laminate is similar to the finest wooden plates, the thickness of which is usually 7-11 mm. In this case, the width varies from 170 to 300 mm, and length from 1 to 1.5 meters. If you pay attention to its structure, it will become clear that it looks like a multi-layer pie. Moreover, each layer of his own appointment. The lower layer acts as bases, the other provides a protective function, the third - the stabilizer, the fourth - the decoration layer, the fifth - the protective film. Laminate more distinguished by the method and mode of production. On this basis it is separated into direct material and high pressure. The second option is considered to be more contemporary.
As for the service life, it mainly depends on the quality of the base and the protective coating. In high pressure laminate, the upper part consists of a variety of components. In addition to high-quality acrylic or melamine resins, substances such as aluminum and corundum oxide are often used. The presence of these materials in the upper layer ensures the desired strength and wear resistance. The protective coating allows you to preserve material from abrasion, as well as from the destructive effect of the sun's rays.
The protective layer covers a decorative layer, which is usually performed from different materials. So, for example, it can be paper or a special foil on which a drawing is applied, often imitating wood, stone, textiles. Under the decorative layer is the main layer, which is made of fiberboard of high density plates. This layer material is usually processed by a special moisture-resistant impregnation. It is it that ensures the strength and wear-resistance of the product. In addition, there is a lock designed to connect the laminate.
Modern types of laminate have another layer, which is called a stabilizer. It is designed to prevent material from droplets of condensate and moisture. In addition, it partially plays the role of noise insulation. A simpler flooring is a direct pressure laminate. It has only three layers that are connected to each other at high temperature.
Methods of laying laminate on concrete floor
In total, two laying techniques are distinguished:
- On adhesive solution.
- Besleless method.
The first way today is applied more and less. The fact is that it has many flaws. Thus, when using it, the bar is fixed using the comb-groove method using special glue. But gradually glue loses its properties, which is why slots are formed in the coating. In addition, if you need to replace individual planks during the operation of the coating, it is impossible to make it if not destroying the floor design completely.
The second method is also called Castle. He is better and reliable. Installation according to such technology is quite simple. Fully eliminated the likelihood of gaps between boards. In addition, this method facilitates repairs. The coating laid in this method can be almost immediately used, and do not wait until the glue dries.
Preparatory work
The final quality of laminate laying largely depends on the state of the concrete base. The complexity of the preparatory stage largely depends on the initial state of the floor. The surface for further installation of the coating should be as smoother as possible. In addition, it should be protected from dampness and ensure good noise and thermal insulation.
If the old flooring was previously made, the surface is required to align. The protrusions are allowed not more than 2.5 mm. If defects are more, they need to be eliminated. For this, you can, for example, sharpen the slots or delete the protrusions. If the total area of \u200b\u200bthe coating is relatively smooth, and at the same time there are only small areas where there are cracks and defects, it is allowed to carry out repair work only in those places where it is really necessary.
For this purpose, "Problem Places" of the foundation must be cleaned, cracks as it should be cleaned with a width of at least 8 mm. The resulting deepening, after the priming process, should be sealed until the surface becomes smooth. To do this, you can use dry formulations that can be found today in many stores building materials. More for this, a solution cooked from cement, tiled glue and fine sand is suitable. All these components are mixed in the ratio of 1: 1: 3, respectively.
When the composition grabbies, the surface will be ground and the priming of the surface is carried out, the base can be considered to be prepared for the installation of the coating. If there are height differences or large concrete surface defects, then you will need a new screed. But it is worth noting that the new screed will significantly reduce the height of the room due to the fact that the level of the floor will turn above. This should take into account the substrate thickness (about 2.5 mm) and laminate.
You can use the traditional tie of concrete or cement base. The latter requires more time to dry. The thickness of such coatings has an important meaning. To minimize the thickness of the screed and faster setting, it is recommended to use special dry mixtures. It will also help get the most smooth surface. If defects are small, and the surface does not have large flaws, it is allowed to align the concrete base with the help of self-leveling compositions. They quickly frozen and make the surface perfectly smooth. Of the disadvantages, only the high price of such solutions can be distinguished.
When repairs will be carried out, the screed is reloaded, it will be necessary to wait until the surface is finally driving. It is best to check this with a moisture meter, but not all of them are at home. Therefore, most will more conveniently use a piece of simple polyethylene film of square shape with a side of 1 m. While water drops will be formed on this film during the night. Whatever rapid drying has promised manufacturers, you should not hurry. If it is already allowed to walk along the flooded floor, it does not mean that it can be laid a laminate. For this you usually need to wait a few days.
Next you need to do the installation of waterproofing. Alternatively, it is possible to use a conventional film that is stacked and combined with a tape. But this is not the best way. Some experts sometimes use moisture-resistant OSB or DVP plates during installation. This allows you to achieve a rather smooth surface.
However, this method is suitable only where there are no strong restrictions on the height of the floor. The fact is that such an alignment will reduce the height of the room by about 16-18 mm. In addition, the panels are mounted on a concrete base, and so that the emptiness is not formed. Otherwise, with time, the floor is deformed and an undesirable creak will appear. In addition, you should not forget that the wooden coating of the composite material can be the habitat of small rodents, insects, mold and rot.
Stepped laminate laying on concrete floor
Before laying a laminate to a concrete floor, it should lie at least two days in the open form in the room where it will fit. Moreover, it is desirable that the temperature there is at least 19 degrees, and the humidity is at least 75%. It is necessary that the coating is accustomed to the existing conditions. This will help when installing and reduce the likelihood of coating problems. As for the process of laying laminate, it is not difficult. The most important thing is that the work surface is properly prepared. This process is described in detail above.
From the tools for work it will be necessary:
- marker for marking,
- a ruler for measurements
- hammer,
- roulette,
- electrolovka.
Materials:
- wooden bar,
- laminate coating
- spacer wedges.
The procedure for performing work is as follows:
- First, a special protective substrate is placed on the working surface. It may be foamed polyethylene, cork coating, felt, etc. This allows you to soften the coating when walking. In addition, due to this, it is possible to achieve good noise insulation. The substrate is lined up before laying the coating.
- Further, the first row of laminate is stacked. Moreover, on the last bar, it is necessary to mark the distance to the wall to the wall and everything is superfluous with an electric bike. At the same time, when inserting spacer wedges, it is necessary to remember that between the wall and flooring, it is necessary to leave the gap of about 11-14 mm. It will then be closed by a plinth.
- For a more dense docking of layers with each other, it is recommended to use a hammer to bother them. And as a support, a tree bar is suitable. Chucking hammer should be carried out during the entire installation process.
- Next, laminate on the concrete floor. The second row begins to lay off the cutboard, which remained after the first row mounting. In the end, a piece of the plank will remain again, which will be the beginning of the third row, etc. As a result, it turns out the surface similar to the chess board. Due to which the load during the operation of the coating will be distributed equally.
- All rows of each other are fastened with the help of locks. They need to snap down by pressing down. Next, the technology that was described above is repeated until the entire surface is laminate.
Pay attention to the process of laying the last row to be smoked in length. For this, the last plank is located on the board of a row, which has already been set by sideways to the wall. It is important not to forget to insert spacer bars with a thickness of 11 mm, which will provide the necessary gap, which is needed in order to during the operation of the laminate it is not deformed, which can occur, for example, when fluctuations in temperature and humidity in the room.
After that, the bar is cut by an electrolybic. If you need to cut a hole for a cable or pipes, then you should leave the gap of 11 mm. When the main works are completed, these holes need to be closed with special outlets.