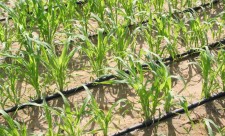
Metal drill sharpening Instruments
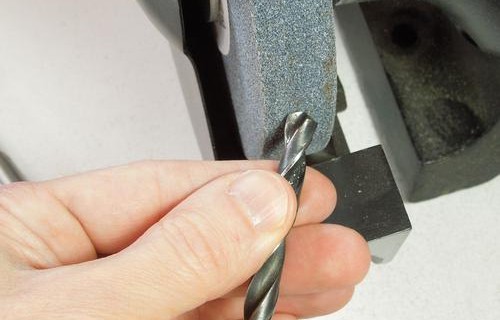
In the arsenal of any wizard, as a rule, there are drills. In order for these cutting devices to function properly, it is required that they are high-quality and sharp enough. It is no secret that over time any drill, even made of superpower tempered alloy, loses its sharpness. In this case, it is not necessary to throw it away - an instructive master can restore the geometry and the performance of the drilled drill. These works can be performed independently, applying uncomplicated devices like a sharpening circle.
Content
Signs of need for sharpening drill
For economic needs, a small diameter drill is most often used - no more than 16-18 mm. Unlike analogs for wood processing, which can serve for a long time without any sharpening, metal drill for efficient use should be exclusively acute. Nevertheless, in the process of metal processing, they are quite quickly wearing. Such a cutting tool, starting to blunt, in operation, makes an unpleasant sharp creaking. When metal drilling, there is a significant heating of the cutting edges, in such cases heat removal from their corners is very difficult. Accordingly, the drill is stupid from the corner, and gradually this process covers the entire edge, and it becomes noticeably rounded. Next begins abrasion of the rear edges and crushed cutting edges. Without sharpening, such a tool in the course of operation will overheat, and the wearing process will increase significantly.
Each time to throw drills and acquire new enough. In order to avoid this, it is necessary to sharpen on time. It is convenient to perform it using specialized equipment. You can also restore the drill performance on your own - for sharpening the drill on metal with your own hands, you can do the use of primary tools with a fixture in the form of a grinding circle.
At home, adaptations are used for sharpening drill on metal:
- grinders;
- electric power;
- electrodels equipped with a special nozzle.
Such equipment will probably find almost every workshop or in the garage. In general, any device is suitable, the electric motor of which will be able to provide the necessary number of revolutions - about 1000-1500 rpm. You will need to assemble the platform for installing the motor and attach an abrasive stone to it.
Technology sharpening drill
To obtain holes in the metal, we use spiral drills with retractable longitudinal grooves, according to which the chips appears when processing the material is treated. Due to the presence of grooves on such a drill there are two screw pen (they are also sometimes called "teeth"). The width of the groove and the pen of the cutting tool must be approximately the same. The core is determined by the depth of the groove. It should be noted that with an excessive increase in it, the chips is more conveniently located, but the thickness of the core decreases - as a result, it can be weakened, in this case, the strength of the drill will decrease.
Rejected back at an angle the screw surface of such a cutting tool on which the chips flows, it is customary to refer to the anterior face. This sharpening corner of the metal drill, formed by the screw groove, is respectively designated as the front. Due to the presence of deviation, the metal chips easily descends on this face. The surface of the cutting tool facing the parts is called the rear face, and the angle to which it is deflected from the cutting surface - respectively, the rear corner. Such a deviation helps to reduce the friction of the tool when drilling. The cutting edge is formed at the intersection of the front edge of the drill with the rear.
The sharpening can be mastered, having learned a little on the failed old drills. To understand how to cool the metal drill, it will be necessary to first take the "keep" the desired pressure and slope. The main thing is to learn to abide by the front and rear corners, and also do not drag the front face. You can select the angle of inclination, pushing out from the diameter of the cutting tool (in the range from 1/4 mm to 1 cm, it changes from 19 to 28 °), as well as from the type of material used (with an increase in its soft, the slope increases). The table of sharpening angles of the metal drill is shown below.
The sharpening should be carried out by processing the rear verses of the drill, and it is required that the sharpened both teeth are identical. It is enough to achieve obtaining the desired form of the rear face and withstand the necessary rear angle of inclination. Implement these tasks is not easy. If the conditions are not observed, the friction of the rear surface and the accompanying heating will increase - therefore, the durability of this cutting tool can slightly decrease. Special equipment is applied to the drainage of metal drills for metal, at home will need sharpening with a simplified method with the help of the available devices.
Preparation for drafting
To perform work on sharpening the drill, it is necessary to properly prepare. It is worth considering that when the rotating grinding stone and the tool interacts, metal particles and sparks can fly into all directions, and when entering open areas of the body, especially in the eyes, can cause serious damage. Thus, during the sharpening of the metal drill, it will be necessary to use protective glasses and gloves.
It should also be taken into account that due to the friction on the rotating plane of the grinding disk, the tool is significantly heated, so in the process of sharpening it will be necessary to periodically cool it in order to prevent overheating. To do this, prepare a container filled with water in which you will need to dip the processed drill. If it is still overheated, the metal will acquire unnecessary fragility and cannot withstand significant loads, with further service such a tool will quickly come into disrepair.
Sharpening methods
Spiral drills are widely used in domestic conditions, with their help you can process both wood and metal. Such a cutting tool is equipped with a shank of one or two-protective, conical, helical or cylindrical shape.
The method of sharpening the drill on metal depends on which form it is required to give its back surface. One-glossy sharpening implies the smooth step of the rear surface of the tooth in the form of a plane with the rear angle of inclination of 29-30 °. With such a drainage, it will be necessary to observe the maximum accuracy, since there is a risk of cropping the cutting edge. This method is optimally suitable for drills with a small diameter (up to 0.3 cm).
Universal drills with a diameter greater than 3 mm are most often treated with a conical sharpening. In this case, it is necessary to repeat the initial sharpening if possible - in this case, the necessary angles will be optimally observed.
Manually, the shading procedure in a simplified form can be performed in the following ways:
- Take the drill to the left hand not far from the cone, the right hand need to capture the shank. Press the rear surface of the drill to the grinding plane. Then, in the direction of the cutting edge, it will be necessary continuously, slowly and smoothly produce its hand. It is worth considering that the drill should not be torn off from a grinding stone until the rear edge of the tooth acquires the desired cone shape. Next, the procedure should be repeated for a second tooth.
- As with the use of the above method, the drill will need to hold the left brush of the hand near the cone, and take the shank to another hand. Next, it will be necessary to press it to the plane of the abrasive disk and, smoothly rotating the drill around its axis, sharpen it back surface. It should not be cut off the cutting tool from the abrasive disk. For the maximum accurate compliance with the desired angle of the drill, you can apply special bushings or racks.
After such a processing, it is easy to get a shank in the form of a cone. For home drill with a diameter of up to 1 cm this sharpening may be sufficient. If there is a greater thickness tool, it is recommended to further apply a bit in front in the cutting edge area - this measure will make it easier to facilitate the drilling process.
With the proper sharpening of the metal drill, symmetry relative to the axis must be observed. It is required that its edges are straight and one length. In addition, it is required to obtain equal angles (pointing edges, as well as rear) at the top of the tool. Check the quality of its sharpening is easy, applying a template made of sheet metal with a thickness of about 1 mm. With it, it is convenient to control the magnitude of the angle of acuction.
Winning drill with attacks can also be fused. It is possible to improve its sharpness by applying an electrical stroke with a diamond stone (in addition, for solid metal processing, speed will be reduced to minimal). It is possible to sharpen such drills if the height of the attack is about 10 mm - in this case, it is necessary to apply one-dimensional sharpening of the disk with short touch, giving the rear surface flat shape and stealing it to the attack. In addition, the front surface will be treated. The coaching angle will win 170 °.
How to perform a sharpening drill: useful tips
When carrying out sharpening, we should not forget that in the process of friction on the abrasive disk, the drill is largely heated. If overheating occurs, the metal softened, losing strength. In order to maintain the maximum working capacity of the drill in the future, in the process of sharpening, when heated, it is necessary to periodically dip it into a container with water or the soda solution (using machine oil is not recommended). It is worth considering that carbide drills in such cooling do not need.
If, due to any reasons, it is necessary to sharpen the Tool Tool, then it is necessary to use the minimum speed of rotation of the sharpening disk. In addition, it will be necessary to sequentially remove the minimum layer of chips, and in the presence of the slightest signs of overheating to stop the procedure before the metal cooled. It will be necessary to constantly monitor that it is heated not higher than comfortable temperature.
The sharpening of the drill is recommended to be performed in the direction opposite to the movement of the abrasive disk - as a result of this processing, the risk is reduced to smith and spark the edge. Processed in this way the drill will serve sufficiently long.
Under the production conditions, the drill sharpening is completed by tapping with a grinding circle with a shallow abrasive grain. As a result of this procedure, the surface of the cutting tool can be given the maximum smoothness, removing the jar. After it, the drill acquires greater wear resistance. If you have such an opportunity, after sharpening, you should configure.