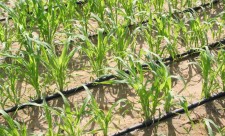
Stone shape do it yourself Useful advice,Building materials
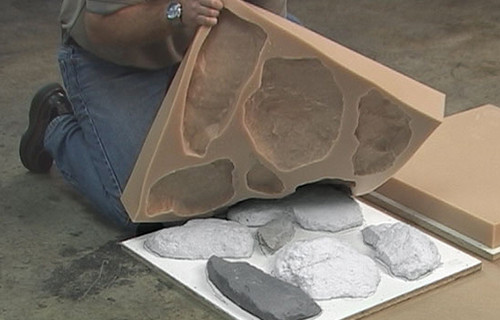
The artificial stone appeared in the building materials market not so long ago, but immediately gained popularity around the world. This is a comfortable facing material that allows you to easily, quickly and cheap to reflect the facade of the house or the household territory. The cost of the finished artificial stone is often indecently high, so many prefer to do it with their own hands. To do this, you can buy a special form with the desired texture, but if you want to create something completely original, then you can make it own. In today's article, we will talk just about this and tell how to make a form for artificial stone.
Content
Types of Forms
There are several varieties of forms for the manufacture of artificial stone, characterized by the material. However, the principle of "work" of all of them is the same - on the inner surface there is a special texture (wood, layers of breed, streak, imitation of the skin, etc.), cement or gypsum mixture is poured into this form, and when it freezes, then the texture of the matrix is \u200b\u200bimprinted on an artificial stone. In fact, all the technology is very simple if you have the right consumables, and most importantly - a form for stone.
Depending on the material, the following forms distinguish:
- wooden;
- silicone;
- polyurethane;
- plastic.
Immediately it is worth notify that the purchase form and the hand made do not have a significant difference in value, if it comes to a single instance. The main reason you may need to make a matrix for filling a stone with your own hands - the desire to make original products with a special texture and what is on sale does not satisfy your requests. Making a stone formed with your own hands will save the visual penny, but it will give valuable experience and the ability to decorate your housing.
For comparison - the cost of a standard form for a decorative stone of 0.24 m² in a supermarket is at least 1500 rubles. Having bought one product, you can produce only one batch of stones at a time, waiting for the complete solo to the solution. Two forms will cost more, but it will go faster. But if instead of spending money on ready-made matrices, put them on the purchase of materials for casting our own forms, you can significantly increase productivity and reduce the time of work.
So, what advantages gives an independent making form for an artificial stone:
- Financial savings.
- Fast pace of work.
- The ability to create unique textures and products with original dimensions.
- Useful experience.
- You can make money on renting or selling already unnecessary forms.
Wooden forms
Wooden forms for the manufacture of stone are not the most successful option, but not to mention them in the context of this topic would be incorrect. The technology in this case is very simple - to create a wooden matrix use old boards with a maximum number of defects - bitch, cracks, convexities, etc. The "worse" board, the more bright texture and the more beautiful there is a stone surface.
In the creation of an artificial stone, it is important to obtain a relief surface and flat walls, so for the bottom of the matrix use texture boards, and for sidewalls - smooth straight rails or phanel.
All items are connected to each other, fixed with nails and coarse joints so that there is no slit, through which the solution can be found. Then it remains only to prepare a mixture from which you will make stones, and pour it into the matrix.
This method of creating forms has the right to exist - it is very inexpensive and simple, but the quality of the result leaves much to be desired.
Silicone forms
Silicone matrix looks like a plastic plane, the bottom of which has the necessary relief. Often, this matrix is \u200b\u200bdivided into several elements and allows you to simultaneously receive several products at a time.
Silicone form properties for stone:
- It has high elasticity and softness, but at the same time very durable to the gap.
- It is quite simple to cook it - it is only necessary to mix several components in the desired proportion.
- Variating the volumetric ratio of components, you can change the properties of the material (beginners in this case it is recommended not to deviate from the instruction).
- In the process of casting the shape in the silicone mixture, small air bubbles will necessarily appear. They must be removed to increase the strength of the product. To do this, use a vacuum machine.
Not any silicone will be suitable for the manufacture of the matrix. It can be classified according to the degree of viscosity. Thus, liquid varieties are used when creating a theater grima, in medicine and jewelry, since it allows you to embody forms with high detail. But Silicone is already suitable for filling more coarse and simple forms - for artificial stone, baking, paraffin, etc.
Polyurethane forms
Some of the most convenient, and therefore popular varieties for decorative stones. Polyurethane products are very durable, possess high elasticity and give a high-quality imprint of the texture on the frozen mixture. In addition, polyurethane itself has enviable durability. Silicone forms, in any case, most of the purchased products are calculated for a certain amount of fillings - 100, 300, 500. Polyurethane matrices can be used much longer, so making them with their own hands is a profitable investment of funds.
The injection molding polyurethane is a synthetic product of a viscous consistency, which, after frozen, acquires the quality of durable rubber. In fact, it can be called the "older brother" of silicone.
Properties of polyurethane forms for stone:
- High elasticity.
- Stronger than silicone.
- Long service life.
- Resistance to the effects of chemical reagents.
- Good transfers the texture from the consumable material on the matrix.
- Easy cooking - you only need to mix two components according to the instructions.
- Forming can be produced at home.
- No need to use a vacuum machine to remove air bubbles. In this case, it is used to warm the construction hairdryer.
Like silicone, polyurethane can be divided into several species depending on the stiffness. Less viscous is used to create forms of decorative elements, medical equipment and various buildings. Medium - molds for stone from plaster, resins or concrete. Hard polyurethane is used for the manufacture of automotive parts, furniture, technical gaskets and various industrial products.
Plastic forms
Another kind of stone forms, but this is not possible to make such at home. Plastic matrices are characterized by stiffness, so they need to use them with extreme caution, so as not to break the product. Their cost in contrast to silicone and polyurethane models is rather low. Basically, plastic forms are used to create paving slabs.
Interestingly, polyurethane is used for the production of plastic form, only the manufacture is carried out by the method of hot and pressing and pressing on special factory equipment.
Making polyurethane form
Such a surface view is quite enough to select the material for the form. Plastic products automatically disappear due to the lack of factory equipment. Wooden models are too rude and unreliable. For home use, it is better to give preference to polyurethane matrices, since they can make stones from cement and plaster mortar, they are easy to manufacture, do not need a vacuum machine, and the price is pleasantly happy.
On this video, the manufacturer of a polyurethane stone shape is shown in detail:
The entire process of producing decorative stone is reduced to keep the mixture in the desired position until solidification. The instructions described below can be used both for polyurethane and silicone forms. The only difference lies in the fact that in the case of silicone, it is necessary to remove air bubbles with a vacuum method, and not heating.
To work, you will need the following tools and materials:
- polyeva polyurethane two-component Duramould et 45A (polyurethane + harvesting) - 10 l;
- silicone for plumbing (waterproof);
- samples of artificial stone with a suitable surface texture;
- furniture stove MDF;
- delimiter;
- mixer (construction or household);
- self-tapping screw;
- scales (better to take kitchen electronic, as they are more accurate);
- putty knife;
- plastic bucket of 1 liter.
Useful advice: Samples for creating a relief matrix can be purchased in a construction store - buy a minimum allowable volume or look in residues or bosa. You can also search the stones with a suitable texture just on the street. Natural stone fragments can be positioned in a beautiful order or slightly sharpen the edges if necessary.
How to make a stone forms:
- Put the MDF plate on the table or a smooth land plot.
- Spread on it 0.5 m² of samples of natural or artificial stone, leaving a 1 cm gap between the elements.
- When all the stones occupied their place, alternately glue each of them to the stove plumbing silicone.
- From the Plate MDF build formwork. Its height should exceed the upper boundary of the samples by 2-3 cm. Screw the shields of the formwork to the plate with screws and thoroughly allocate all the joints with silicone. Apply it outside and inside the shields.
- Check the surface horizontality by the construction level.
- When silicone completely freezes, apply the separator on the stones and the inner surface of the MDF. After frozen, it form an impenetrable film, so after drying the polyurethane mixture, the form can be easily separated from the stones.
- For the manufacture of a form, not only English polyurethane Duramould et 45a can be used, but also any other. You may find options for cheaper, the main thing is that it is two-component. Duramould et 45a comes in plastic 5 l - red liquid and transparent viscous. Taking advantage of the weights, measure 0.5 liters from each canister and proceed to the bucket.
- Mix the mixer to uniformity and pour the mixture into the formwork.
- Slightly warm the surface with a hairdryer to come out air bubbles. Praise Fill out the form to the edges and leave to dry about a day.
- During this time, the viscous substance will grab and turn with an elastic form for the production of stone. Now you can split the formwork and remove the matrix. In those places where the polyurethane is strongly sliding, it is possible to work as a stationery knife.
- If you should stick sample stones to the MDF plate, it is not difficult to decide. If some elements still remained in the matrix, they can be carefully squeezing from there.
- After separating the form, give it some time to completely dry - the inner surface will first be a bit raw and oily. Wipe it with a dry cloth without push and leave for a couple of hours. After that, you can start making beautiful decorative stones of our own production.
Useful advice: Polyurethane does not secrete toxic evaporation and generally practically does not smell, but it is better to work with it in a well-ventilated room. The temperature in the room should be at least 21c.
Despite the seeming elementality of the entire technology, skills and clear following instructions are needed for the manufacture of perfect and smooth shape. Mix polyurethane components in a clear ratio - the operational characteristics of the future product depend on this. Before you begin to cast a form, we advise you to practice "on cats" - make molds of small sizes from one brick, stone or relief tile.
Stone shapes: photo
If you do not know what form to give homemade stones, we suggest you to see a selection of photos. As samples for pouring, you can use literally anything, ranging from natural minerals, ending with plants, wood and even stucco.