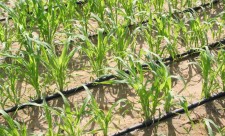
Laying of walls of ceramzite-concrete blocks: technology, features, methods Walls
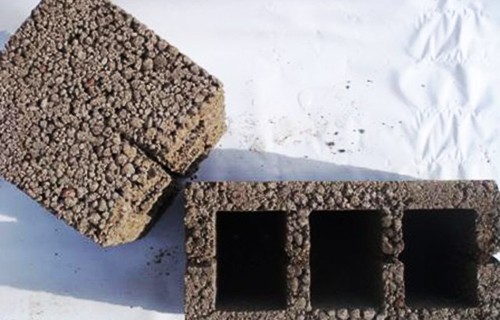
Today, the abundance of building materials allows you to choose the optimal option for any needs and any wallet. In the field of manufacture of outdoor enclosing structures, there is a tendency to replace ceramzite concrete products, other varieties of insulation. However, despite everything, the construction of walls from ceramzite concrete blocks remains the most common way to build durable and warm structures.
Specifications
The initial raw material for ceramzite concrete blocks is a fully natural product. Ceramzite is an undent and foamed clay, which as a result of processing acquires the structure of frozen particles of foam. The resulting granules are covered with a smoking shell, which provides high strength of the material. The porous structure of the clamzite makes it extremely easy and convenient to use. Ceramzit concrete blocks not only correspond to high standards of heat and sound insulation, but also make up serious competition to ordinary concrete and bricks.
Ceramzitobeton is used everywhere for the construction of residential buildings, the arrangement of underground communications, livestock equipment.
Advantages
Walls made of ceramzite-concrete blocks have excellent sound and thermal insulation. This material is universal, well withstands the temperature differences, does not let moisture and is suitable for construction in any climatic conditions. The special structure of the ceramic blocks allows you to pass the air, adjusting the air flows indoors. Thus, it is possible to ensure good ventilation of the internal space.
Constructions built from ceramzit concrete blocks can be considered eternal without exaggeration. The material does not require special care, it is not subject to corrosion, burning, damage to pests (insects, rodents, fungi). It combines the most useful quality of earth, stone and wood. The thermal insulation properties of the material often play a decisive role when choosing. Special research institutions have repeatedly carried out testing of various clay gravel fillers. As a result of the test, it turned out that this material is capable of reduced heat loss by more than 75%.
The flow of this building material also causes to be bowed in its favor - the thickness of the wall of clay-concrete blocks 390 mm is equal to a brick wall posted in 1.5 bricks. The same indicators concern and height. Thus, the use of clay makes it possible to significantly save not only the costs of building materials, but also the time to build the structure.
Laying wall
Methods
The molding of walls from ceramzite concrete blocks can be carried out in several ways. The choice of method directly depends on which thickness should be the wall and which cladding materials will be used for finishing.
Consider every method:
- Wall masonry, the thickness of which corresponds to the width of one clay-concrete unit 200 mm. The inner surface of the wall is separated by plaster, the outer-layer of the heat-insulating material is thick up to 100 mm. It can be a foam, mineral wool, Polyopoentherol, etc. This method is perfect for the construction of garages or warehouses.
- Wall masonry, the thickness of which corresponds to one length of the block. They are tied with each other, and the outer and interior decoration is performed on the principle of the first method. The only difference is the thickness of the heat insulating layer must be twice thin (maximum 50 mm). This method is ideal for the construction of a bath and small structures.
- Laying walls with dressing of ceramzite concrete blocks and leaving a small empty space between them. The thickness of the ceramic concrete wall in this case will be 600 mm. Plaster is applied to the inner part, and the thermal insulation is laid in between blocks. This method is suitable for the construction of country houses.
- The outer surface is laid out by two parallel thin walls bonded by reinforcement. In between the walls, thermal insulation is laid. A layer of plaster is applied to the inner and outer surface. This is the most time-consuming method for the construction of walls of ceramzite-concrete blocks, but the most winning in all indicators. The level of thermal protection and durability is much higher than that of any other building material. This method is suitable for building buildings in the prevalence of cold climate.
Technology
The construction of walls from the ceramzitobetone by and large does not differ from the use of ordinary brick. The same tile or spoon rows and mandatory bandage are made.
Required tools and materials:
- building level;
- small rubber hammer;
- plumb;
- swarf cord;
- corolnic;
- kelma with a rectangular area;
- extending;
- USM with cutting circle 23cm in diameter;
- armature / reinforced grid (if reinforcement is planned);
- shovel;
- capacity for breeding solution.
At first it is necessary to align the basis on which the first number of blocks will be laid. After that, waterproofing of two layers of rubberoid is based on the basis. Then cement glue or prepared mortar is superimposed on top of the waterproofing. The thickness of this layer should not exceed 30 mm.
The solution is two types:
- cement glue - calculation: 1 cubic masonry meter by 40 kg of dry mixture;
- cement mortar - 1 part of cement, 1 part of sifted river sand on 3 parts of career sand.
When calculating the walls of ceramzite-concrete blocks, it is necessary to remember that construction begins with an angle. Then the full range is laid out, and the inner partitions of the wall will chase evenly with the outer. To avoid the appearance of cold bridges on the ends of the blocks, set in the outer wall, it is necessary to isolate these blocks of rectangles cut out of foam. The thickness of the rectangle is about 50 mm.
When a series of ceramzite concrete is completed, it is necessary to make sure the surface evenness. To do this, use the construction level. Each ceramzite concrete block is characterized by a slight cone.
Reinforcement should be performed using a special reinforced grid or reinforcement 10 mm in diameter. To achieve the best results, the procedure must be repeated throughout the perimeter of the walls every 2-3 rows. A grid or fittings are put on top of the finished row, glue or solution is applied on top, after which another row is placed. In the process, do not forget about the alternation of spoonful and twitch rows.
Main nuances
In order for the design of the wall of the ceramzite-concrete blocks, it is solid and reliable, you need to adhere to certain masonry rules. Consider the construction of a wall from blocks of 9 * 190 * 188 mm. For construction partitions, blocks 390 * 190 * 90 mm are used.
Sequence of execution:
- To smooth out the superimposed layer of the solution to find a uniform coating.
- Tut the tame to the ceramzitobetone to the edge of the block, already squeezed in this row. Leave a gap between blocks about 5 cm.
- Attach this block to the place where it should be located in such a way that the vertical seam assembled a bit of solution. It is recommended that the seam's tile does not exceed 10 mm.
- Without waiting for the solution until the solution is hardened, create seam. There are several varieties of special seams: embroidered convex, embroidered concave, void, inlet.
- At the end of the masonry process, regardless of the method that you took advantage of, you need to fill over Armopois. This is a reinforced concrete structure, the task of which is to perform the function of the rafter system. Armopois does not allow the walls to fall under constant pressure of the roof.