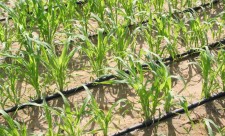
Blacksmithing equipment: Machine for cold forging with their own hands Instruments,Useful advice
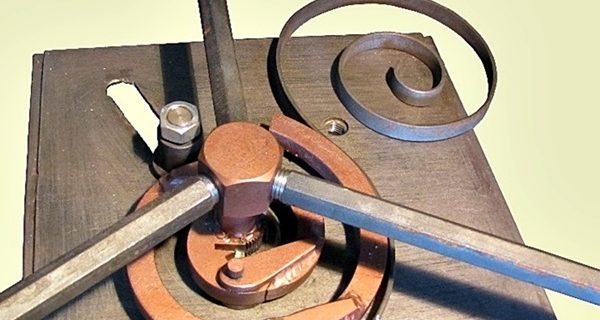
Forged metal products have always been distinguished by their beauty. Thanks to this, the profession of the blacksmith has always been in demand. Forged gates, wickets, window lattices installed in a private house, to this day are considered a sign of wealth and good taste. If earlier all work on forging metal was performed by hand by the method of hot forging, at which the blacksmith heated the workpiece and cut it with a hammer until it reaches the desired form, now it is not so. First, modern metallurgical enterprises rolled the finished profile for the production of forged products (mainly for them is used steel square with a cross section of 10x10 - 20x20 mm or a round rod with a diameter of 8 to 16 mm), and secondly, there is a whole linear of special machines, Which make forged elements, without resorting to its heating. The use of machines made it possible to produce serial details that would be the same size.
Content
Features forging machines
Cold forged machines can be divided into two main groups:
- Mechanical. Machines with electric and gearbox. Mainly factory manufacture. They allow you to increase productivity and establish a small business. However, the cost of such equipment is quite high, which is the cause of its inaccessibility for the majority of the population.
- Manual. More simple design and in the production of bending machines for cold forging with their own hands. They have more limited capabilities, however have two undeniable advantages: their price is more accessible, as well as such machines can be made independently.
About how to make a machine for a cold forging with your own hands, let's tell further.
Cold forging process, its features, advantages and disadvantages
The process of cold forging is one of the most simple methods of metal processing. He is an excellent start for those who are just starting work with steel. Thanks to the cold forging, you can make a large range of different figures for large metal structures.
The process of manufacturing metal structures using a forging without heating the blanks can be divided into three stages:
- Bending a design element. To get a curly element from a direct piece of metal, it needs to bendled. It is done on a cold forging machine using special mandrels.
- In order to give elements additional forms in the form of peaks or goose paws, the blanks are pressed.
- The last step, all elements with welding are collected in one design.
The main advantage of the cold forging process is the lack of heating the part, which eliminates the need to use combustible materials and the construction of the mountain. In addition, thanks to the use of cold forging machines, you can make large series of the same details, using ready-made patterns.
The disadvantage of the cold forging process are steel properties. With its cold processing, it becomes not too plastic that, with inaccurate work, can lead to cracking of the workpiece. That is why it should be carefully working with a cold blank.
Handmade Cold Forged Machine
The simplest to use for bending a metal blank is "Snail". This manual machine received its name at the expense of the mandrel, which has a snail shape. It is made of durable steel, capable of withstanding large mechanical loads. The principle of operation of such a machine is extremely simple. The end of the workpiece starts in a snail groove, and by turning the latter around its axis or movement of the workpiece itself, it is bent in the necessary form. For the production of details of various shapes use different sets of snails.
There are two types of hand machines for cold forging:
- With moving snail.
- With fixed snail.
The second type is most preferable. Due to the long mobile handle, which pushes the workpiece, you can apply a great force to it (lever rule), which will allow the rod to process any length. To select the most suitable design for specific conditions, you can watch the video on the work of cold forging machines made with your own hands to assess their capabilities.
The homemade machine for cold forging, made by their own hands, consists of several main parts:
- Stanna. The metal surface on which the snail is fixed. It consists of a desktop and stand on which it is fixed. The table is made of sheet steel with a thickness of at least 5 mm. In this case, its surface must be perfectly even so as not to spoil the workpiece. The desktop is made in the form of a circle, so that the handle of the machine rotates around it. The rack of the bed is made from the pipe with a diameter of 76 mm with a welded flange to fasten it to the floor on anchor bolts.
- Lever arm. It has a rather complicated design. Consists of the upper removable part and the bottom - the main part. The lower part is a profile tube with a size of 45x25 mm, at the end of which the bearing bearing with a protracted bolt is welded from the pipe of a large diameter. Thanks to the bearing, the lever will rotate around the table.
- Two supporting metal structures are brewed to the lower part of the lever, which will be inserted up the upper part. It will be removable, which will allow you to remove it if necessary, as well as adjust its position on the table. The upper part is made from the same profile pipe with the bearing welded on the end. The first one is stubborn, thanks to which the lever will slide on the surface of the table, and the second will directly put pressure on the workpiece. Thanks to the collapsible design of the lever, such a machine can be used for the manufacture of twisted products. To do this, in the center of the table and in its working head, fixtures for the clamp of the rod are made. Now, when rotating the lever, you can twist the rod around its axis, making twisted products.
- Mandrel. Mandrels can be made both independently and purchase in specialized stores. To install on the surface of the table, end-to-end holes are made.
To facilitate the task, it is recommended to make the drawings of the machine for a cold forging with their own hands.
Making a machine for cold forging with their own hands
Before making a cold forging machine, you need to prepare materials and tools. Materials will need:
- Sheet steel with a thickness of 10 mm for the manufacture of a table and squeaks.
- Pipe pieces with a diameter of 90 mm and 76 mm for the manufacture of the rack and the closure for bearings.
- Pipe profile size 45x25 mm for the manufacture of levers design.
- Corner and strip. Need to enhance the top of the lever so that it does not get bent during the folding of the workpiece.
- Bearings. The size of the bearings depends on the diameter of the seating. Pick out of not too complicated.
Order of work:
- To begin with, a circle of 600 - 700 mm is cut out of a piece of sheet metal. This is done using a gas cutter. If this is done problematic, you can order it in a company that trades metal. From the cutting of the metal produced off. To install the bed from the same sheet, a rectangle is cut with a size of 1000 x 900 mm.
- Then cut a piece of pipe with a diameter of 76 mm. Its length is determined individually. It is welded 4 kosinki from the bottom end. After that the pipe is welded to a rectangular base.
- Now the bottom of the lever is manufactured. Pipe profile is taken and a piece of 1400 mm long is cut. It is welded to the cut pipe of a pipe with a diameter of 90 mm and a length of 30 mm. Then there are two holes with a diameter of 8 mm and 2 nuts are welded. They will screw up 2 screws to hold the bearing.
- Next, 2 supporting structures for the top of the lever are made from the same profile pipe. As soon as they are ready, they are welded to the bottom. Holes are made in supporting structures and nuts are welded for clamping bolts.
- Now the lower part of the lever can be installed in place. The bearing dresses on the pipe, to which the lever is put on top and is fixed by bolts. As a result, the lower honor of the lever can rotate around the rack of the bed.
- Next top is welded the table of the bed.
- Now you can proceed to the manufacture of the top of the lever. It is produced from the profile pipe of 45x25 mm with a length of 1 m. It consists of the upper part of the handle and the working head, which is welded to this handle. The head is a welded metal structure with a tailored piece of pipe or circle for the installation of bearings.
- In parallel, the knob is installed behind the stapper. It will be responsible for gliding the lever on the table surface. Perpendicularly mounted 2 pressure bearing, which will directly press the workpiece to bring it up. Bearing sizes are selected individually. The top of the working head is better to strengthen with the help of the corner so that it does not get bent. Next, the removable part of the lever is adjusted and calibrated in the workplace.
- The next step in the surface of the table it is necessary to make holes for the installation of mandrels. To do this, you need to attach every mandrel to the surface of the bed and outline the location of the holes. Apply in such a way that its center in which the workpiece is inserted, accounted for the center of the table. Holes are drilled with hand drill. Their diameter should be 0.5 mm more than the diameter of the knob of the mandrel so that they are installed freely.
- After that, all the details of the machine should be projected and painted. Now you can start work on the cold metal forging with your own hands.
Machine for cold forging with her hands: photo