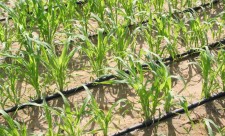
Cutting sheet metal: features of the technological process Instruments
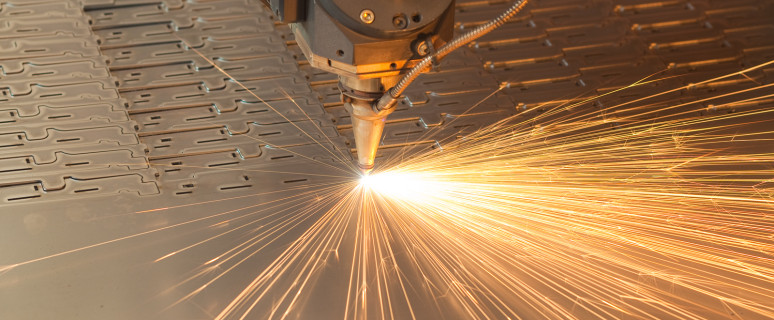
The process of cutting metal provides a number of manipulations, such as punching, cutting, cutting, cutting, cropping material. The purpose of performing these procedures is the manufacture of various parts and blanks. Cutting is carried out by exposure to the cutting tool on the material. There are several ways to cut metal sheets. Consider the two most productive and sought after.
Content
Cutting sheets by means of laser radiation
One of the methods of cutting a metal sheet is a laser cutting, which has become one of the first approbations of laser radiation. This method allows you to process parts with high accuracy, in the lowest time and at the same time get a qualitative result. With the help of laser cutting, you can take the cutting of almost all types of sheet metal. The exception is a material that cannot undergo this processing due to non-corresponding thickness. Through this method, you can also make engraving on sheet metal.
Principle of operation
The essence of this processing is as follows. The surface of the material is heated at certain sections with a beam, which focuses at the desired points. The process controls the computer on which a special program is installed. The effect of high temperature allows you to paint fragile and thin metal sheets without damaging their integrity. This method allows you to process various types of non-ferrous metals. For example, steel, aluminum and its alloys, etc.
Using a high concentration of energy provided by laser radiation, alloys can be revealed with any thermophysical qualities. In this case, the thermal exposure zone is minimal. The operation of laser installations provides auxiliary gas, which, together with the radiation, enters the processed area. Under the influence of the beam, the material heats up, melts, after which evaporates along the cut line. Next, using the auxiliary gas, destruction products are eliminated. This method of cutting has a number of advantages that increase its performance.
Advantages of the application of a metal cutting laser
- The cost of laser processing is sufficiently affordable.
- Through the effects of radiation, you can also process even the hardest types of metal.
- The impact of the laser provides high performance performance, while preserves good quality cut. This result is explained by the high density and radiation capacity of the laser.
- High speed process.
- In the course of processing, there is no mechanical contact with the material. This makes it possible to paint the fragile types of metal, which are difficult to cut in another way.
- The outline of the cut can be any complexity.
- Economical consumption of material. Billets on a metal sheet can be positioned quite tight, the cost of the final product is reduced.
- Details made in this way do not need further processing.
- Laser rays are quite easy to control. This makes it possible to perform cutting material on a complex contour.
- The thin line of the cut is from 0.07 to 0.1 mm.
Recommendations for revealing with laser radiation
- It is not recommended for the laser cutting of the metal to paint the poor-quality metal - rusty or having traces of corrosion, since the quality of the cut in this case will be noticeably worse than in the case of the use of high-quality materials.
- It should also not use sheets having significant irregularities.
- The end result depends, including on the location on the sheet of parts. The distance between them should not be less than 5-10 mm. And from the edges of the metal parts should be placed at least by 10 mm.
- Improve external parts indicators can be used by rounded corners. In this case, the machine in the process does not reduce the speed of the cutting head.
- The cost of cutting with the help of laser cutting is determined in particular and the number of contours. To perform each circuit, the machine makes the cutting into the material near the line, which requires extra time. This explains the higher cost of such treatment.
Plasma cutting metal
With this method, cutting sheet metal cutting tool is a plasma jet. Plasma is air heated in the form of an electrical arc to a large temperature and in an ionized state. The ignition of the arc occurs between the working metal surface and the electrode. The plasma is formed by an arc of gas delivered to a nozzle under certain pressure. Temperature indicators of the formed jet reach 30000 ° C at a speed of 500 - 1500 m / s. With the help of such a plasma jet, you can cut a metal with a thickness of up to 100 millimeters.
Principle of operation
- The arc is lit as a result of a high-frequency pulse or short circuit between the material and the sprayer. Cooling the sprayer is carried out by a gas stream.
- The medium from which the plasma jet is formed is divided into an active and inactive type. The first includes oxygen and air. These gases are applied with row of ferrous metals. The second type includes hydrogen, nitrogen, water vapor and argon, which are used to obtain billets from non-ferrous metals or alloys.
- The cutting arc of plasma converts electricity to thermal energy. Its voltage is determined by the dimensions of the plasma torus, the current force, the composition of the gas plasma and the space from the nozzle to the working metal surface.
- The temperature along the arc axis and the cross section of its pillar is non-permanent. The temperature indicator is determined by the same parameters as the voltage, as well as the diameter of the arc pillar.
- Due to the high temperature of the arc, almost instantly crashed into the material. Subject to the optimal ratio of the power of the arc and the thickness of the metal, the cutting arc penetrates through the thickness of the material. As a result, the edge of the cut is obtained vertical.
It is necessary to ensure that the speed does not exceed the required level, as this may cause not a complete teething of the metal.
Advantages of metal cutting plasma arc
- Plasma cutting is characterized by universality. Through this method, you can cut different types of metal.
- Work is performed at high speed.
- The result of this cutting is high-quality cuts that do not require subsequent machining.
- The shape of the cut parts may be any, even the most difficult.
- When applying the plasma, there is no need to use expensive gases, such as propane - butane, oxygen and acetylene. This makes the process economical.
- The procedure for using plasma is characterized by safety, since explosive gas cylinders do not apply during the work.
- Environmental environmental safety.
- The material being processed during cutting is not deformed.
- In the case of work on painted surfaces, there is no need for preliminary preparation. The appearance of the surface will not be spoiled, since paint processing will be minimal.
- Plasma time on metal minimum.
Process technique
As a result of plasma application, the temperature is influenced by a temperature of several tens of thousands of degrees. This allows you to carry out the processing of metal sheets of any type. Plasma cutting technique Next:
- The cutter is located near the edge of the material. The activation of the switch button is activated first the duty arc, then the cutting. At this stage, the cutting procedure goes into an active stage.
- During the process, the support of a permanent distance between the end of the cutting arc tip and the surface of the material used is important.
- The arc should have the lower direction, and the angle of its location relative to the working surface should be direct. The cutting arc smoothly moves along the cut line.
- The speed in this should be such in which the sparks are visible from the reverse surface of the material. If there are no sparks on the reverse side, it suggests that the metal is not cut through. There may be several reasons for this:
- insufficient current;
- plasma direction does not correspond to direct corner;
- the set speed is too high.
- Properly installed current and the arc speed are determined to obtain a high-quality cut without any deformations. To determine the appropriate level of these indicators, a test section should be performed using a higher current. Next focusing on the speed of movement to adjust it in the right direction.
Conclusion
Cutting metal is a technological process that allows you to get metal blanks or parts of the necessary form and sizes. To date, there are several methods for cutting metal sheets. Among them, plasma cutting and processing on a laser metal cutting are occupied. These methods make it possible to carry out the processing of any types of metal and receive a high-quality result in the shortest possible time. At the same time, the procedure is safe, economical and does not harm the environmental environment.
Washing sheet metal on video: