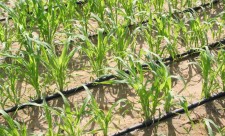
Grinding machine on concrete. Purchase and Application Features Instruments
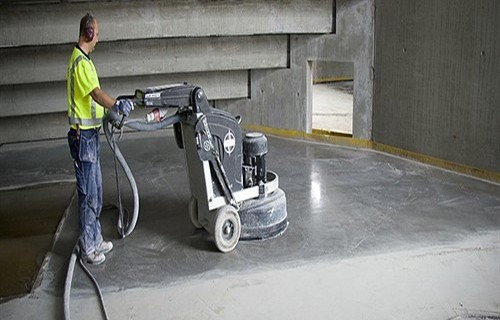
Currently, the choice of the grinding machine along concrete, the price of which is not small, complicated by a huge assortment of various models, no different look at first glance. However, each model of grinding equipment is characterized by other models with performance, weight, functionality, destination area and other characteristics, so before such an important acquisition should be first familiar with the main indicators of the aggregate.
Content
Purpose of grinding machine
Quite often, when conducting a major repairs or execution of finishing works of a small volume, a flooding of the floor or walls made from a conventional, reinforced or decorative concrete is required. Since concrete is a very hard material, it is not possible to poll it to the perfect state manually. Solving problems related to the processing of concrete surfaces, lies in the use of special grinding machines on concrete, which can be used in any construction or specialized store.
The functionality of the grinding machine allows:
- Qualitatively and in a short time to polish the concrete surface of any area.
- Removertically remove the top layer of concrete, which has lost its strength quality during operation.
- Align the surface to perform finishing works, removing the elevation or smoothding the bevelled areas.
- Create a certain degree of roughness needed to improve concrete adhesion with adhesive composition, putty and other materials.
Thus, the grinding machine will be an indispensable assistant when preparing concrete bases of any configuration to the finishing finish.
Benefits / Disadvantages of Grinding Machine
Despite the diversity of the functions performed, various grinding machines are not deprived of certain advantages and disadvantages, most of which are detected only during operation.
Advantages:
- Wide range of units for household and professional use.
- High speed and quality surface preparation for further finishing works.
- The maximum level of error in the grinding process of concrete does not exceed 2 mm.
- Easy to use machines that do not require special skills or knowledge.
- The manifold of nozzles that allow to obtain the surface of varying degrees of smoothness.
- Long service life.
The most significant drawbacks should be attributed:
- The formation of a large amount of dust in the process of surface treatment.
- Improvest costs of consumables.
Depending on the type of machine, the list of advantages or disadvantages will be supplemented with new sub-clauses, since each model has certain operational characteristics.
Types of grinding machines
The functionality and area of \u200b\u200bdestination of the grinding machine is largely determined by the model to the model to one or another type of design. To date, grinding machines are divided into:
1. Angle - are used for cutting, coarse processing or stripping metal, concrete, stone and other solid materials. Small dimensions of the corner-glasses allow you to qualitatively perform work in hard-to-reach places (for risers, under batteries). Units not equipped with a system that allows you to adjust the circle rotation frequency well coped with a sharp solid materials, but are intended only for some types of grinding. Separate models are equipped with a disk auto-balancing function that excludes the vibration of the tool, which occurs during uneven wear of the consumable material.
2. Ribbon - used for coarse processing or stripping solid bases with not very dense structure before further operations. As a consumable material, there is a ribbon of coarse sandpaper, which makes it inappropriate to use grinding machines of a ribbon type when processing concrete surfaces of a large area.
3. Vibration - characterized by good instrument maneuverability, low weight, as well as an acceptable cost of consumables. In most cases, vibratingrene machines are used in the processing of small areas before finishing finish. The processing of the concrete surface is carried out due to the reciprocating movement of the flat working surface. The fasteners of the consumable material in the machines of the vibration form occurs by means of velcro or special clamping devices. Fastening the consumable material with velcro relatively expensive option, but significantly reduces the time to replace it during use. Fixing the consumable material by means of clips, although it takes some time, but it is much easier to choose a replacement than on velcro.
A variety of vibration devices are delta-grinding machines, the working sole of which is performed in the form of an iron, speaking outside the body, which contributes to the processing of surfaces in hard-to-reach places.
4. Orbital (eccentric) - concrete grinding occurs due to the circular motion of the working disk, as well as a reciprocating course provided by the displacement of the orbit by 2-6 mm. At the same time, the greatest stroke of the eccentric is used for coarse processing of concrete bases, while the low amplitude of oscillations is designed for a thinner work. In expensive models there is a function of adjusting the stroke of the eccentric. Fixation of consumables is carried out similarly to the vibration type machines. Orbital-eccentric machines are available in different power, which facilitates the choice of the device both for life and for professional work. In almost all models of machines, the vibration effect on the body is provided by including vibration stabilizer. However, the processing of the corners of the room and other hard-to-reach places of this type of machine is possible, since round discs are used as a consumable material. In most cases, various devices are equipped with a dust bag with the possibility of connecting a vacuum cleaner.
5. Mosaic-grinding machines for concrete - are intended for carrying out operations on grinding, alignment, as well as polishing a monolithic base from a conventional, decorative or reinforced concrete. Mosaic-grinding units are used for the initial preparation of the floor surface, walls to apply protective coating on them. Mosaic type machines belong to the most expensive category of grinding devices, as they are used to perform a more subtle work. Regarding other types of grinding devices in concrete, the details of mosaic machines are better protected from dust, and some models are immediately equipped with a vacuum cleaner. However, all the advantages of mosaic structures are affected both at the high cost of the machines themselves and the consumables associated with them, which are accepted by cases of carbide elements or diamond segments, diamond cutters, as well as abrasive segments.
Thus, when choosing a type of grinding machine, it is necessary to estimate the need to have different functions that increase the cost of the machine, the possibility of fastening a different type of consumables by which the concrete surface acquires various degrees of smoothness, as well as a number of other criteria affecting the performance of the machine.
Criteria for selecting grinding machine
The quality of treatment of concrete walls, gender and other surfaces depends largely on the design of the machine and the consumable material suitable for it. Therefore, when buying a grinding machine, it is necessary to take into account a number of factors, knowledge of which will help to make a choice towards the most suitable grinding machine, based on the conditions of future operation.
Universality
Based on the functionality, grinding machines are:
- Non-specialized - allow you to perform either coarse processing, or the finish grinding of the coating of a certain type of material. As a rule, for highly specialized devices, it is possible to use only a certain type and size of the consumable material.
- Multifunctional - differ in a more complex design that allows grinding, polishing and other operations associated with the treatment of concrete surfaces. In addition, the use of several types of consumables is provided in multifunctional grinding machines.
Methods of grinding
The grinding process can be carried out in 2 ways:
- Wet - in the process of surface treatment, directly into the grinding zone, water is constantly fed, which extends the life of consumables, and also facilitates the grinding process, reduces dust formation. In most cases, wet grinding is used in the processing of mosaic and marble coatings.
- Dry - in the process of dry grinding a large amount of dust is formed. However, the operator can eliminate the shortcomings on time, because with a dry way the visibility of the surface treated is much better.
Management type
All variety of grinding machines on concrete is divided into 2 categories:
- Manual machines - designed for a small amount of work. Surface processing and the movement of the unit occurs with the operator without visible effort. In general, manual grinding machines on concrete are characterized by an acceptable cost, as well as the simplicity and ease of control.
- Self-propelled installations are more suitable for large scale work, since concrete processing is carried out by means of built-in automation that does not require the availability of the operator. For unhindered movement at the construction site, self-propelled machines are equipped with chassis. However, all these amenities and many additional functions increase the already high cost of robotic machines.
engine's type
Depending on the installed engine, grinding machines are:
- With gasoline drive - indispensable in conditions of limited, or remote access from the electrical network. Machines of this category are characterized by high power, therefore apply in the implementation of large-scale work. However, during the operation of gasoline drive machines, a constant inflow of fresh air is required.
- With electric drive - characterized by less power than gasoline, the ability to connect to a voltage to 220, 380 V, a small level of noise during the performance of work, as well as the possibility of operation in closed rooms. The only condition is the presence of constant voltage in the power grid.
Power
The performance of the grinding machine is directly interconnected with an indicator of power.
The low-power (800-1400 W), compact, at an acceptable cost of the device are more often used in everyday life. This is due to the lowest duration of continuous operation, component of 2-3 hours per day, as well as the minimum set of additional functions.
Powerful units (1400-5500 W) are a professional technique equipped with a number of additional functions and able to withstand multiple operation in intensive use mode. However, the cost of such machines increases commensurately their functional capabilities and brand affiliation.
Disc rotation frequency
The speed of rotation of the consuming can reach 300-48000 revolutions per minute. At the same time, the treatment of concrete at high speed is made by discs of a small diameter for a more accurate stripping. A small speed with big discs is necessary to obtain coarse processing, stripping seams.
The most optimal option when the grinding machine has a built-in speed adjustment system.
Expendable materials
When grinding any solid surfaces, as the main consumables are:
- grinding discs;
- cups with diamond segments with durability to various types of pins, nails and other fittings, which protruding from concrete base;
- bowls having carbide attacks are somewhat inferior to the previous option.
In addition, the size fraction of consumables directly affects the quality of processing. For the finish grinding, a disc with fine-grained inclusions is suitable, and for rough-bowls with large diamond segments.
Maximum disk diameter
The relatively inexpensive model of grinding machines involve the functioning of the unit with the consumable material in the form of a certain size disk, varying in the range of 100-230 mm. Small discs (up to 125 mm) are used for thin processing of solid materials, large (over 230 mm) - necessary for coarse grinding, medium (150-180 mm) - more suitable for stripping seams, imparting surface roughness.
Thus, when choosing grinding equipment, it is worth considering not only the fundamental characteristics of the model, but also its functionality.