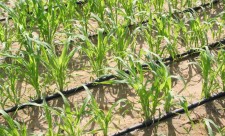
Rollers do it yourself Instruments
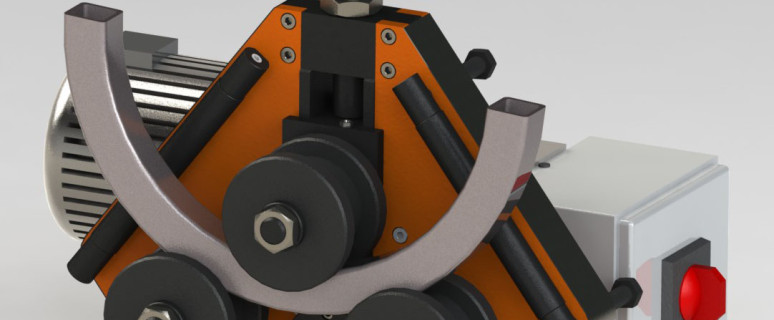
In the list of the most popular devices in any metallurgical production, the rolling machine (rollers) is leading. With the help of rollers, it is possible to bend a metal sheet, bend the pipe, any oval or other parts of the part. The rollers and in jewelry manufacturing are used for the right and neat bending of jewelry.
Content
Description of rollets
The main working mechanisms of rollers are rotating cylinders. The hotbeds of the metal are passed through cylinders and, thus, a metal bending occurs. Rolling machines, depending on the purpose, have from 2 to 5 cylinders, and the highest distribution received 3 and 4 roll models.
For the bend of parts, the third rear shaft is responsible, and the radius of the roundabout, in turn, is determined by the distance between the rear and the upper shaft.
Because of the sometimes very large loads, the rollers for metal can break, which leads to a frequent replacement of machines. While working with iron, it must be repeatedly heated, after the roller machine, iron layers are sent to the furnace, they split and repeat rolling again. Then again heated iron bars are sent to the varietal machine.
Passing through the rollers, the cross section of the metal decreases and it is lengthened. Such an action has a high heating temperature of metal products and the degree of pressure on them.
In order to make a product of a cylindrical form, you need to configure the rear shaft parallel to the front. When making a metal cone, the rear shaft must be installed at an angle relative to the front.
There are models of rolling machines much easier, the metal processing can be performed by installing on the table. Such models are less functional, since the device during operation is constantly kept in place. However, you can use fasteners - it is much simplified the rolling process.
The smaller the dimensions of the device, the lower its cost. When choosing a roller machine, the size of the greatest part, which is to be processed, and its thickness should be considered.
Modern rolling machines are capable of performing such functions:
- bending pipes up to 180 °;
- working with metal pipes;
- deformation of pipes of different diameters.
Scope of application
Calcular machines were found in the production of air ducts, drains, ventilation systems, pipes, chimneys.
Small sizes of cars allow you to use them anywhere and directly on a construction and installation object. Manual rollers do not spoil the polymer sheet metal coating.
The food industry uses crushing rollers, for example, in the production of flour. In the chemical industry, you can find sheets, refining, leafy rollers.
The latter have a number of explicit advantages, such as: reliability, simplicity in maintenance, high performance, a system for adjusting the stroke of a metal sheet.
Rollers for metal
To give the cylindrical shape to the sheet metal, it is simply impossible to do without a roller machine. Pipe rollers are most often used in the manufacture of water supply systems. Rocking machines with forging cylinders carry out cold flexible metal blanks and belong to the category of rotary models. This equipment can be used to work with thin-sheet steel, from 0.1 to 120 mm thick. You can also perform processing of plastic metals, rubber mixtures and plastics.
The rolling machine is selected depending on the thickness of the materials. Double-color rollers consist of two parallel shafts. The upper with a small diameter of the section is often made from high-strength steel, and the lower, with a large diameter of the section, consists of steel with a rubber coating. From how power will be the pressure on the pipe, its output diameter depends. The rollers are trivial are pyramidal, that is, symmetric, and asymmetric. Today they are very in demand at the production of ventilation air ducts, drainage rates of round forms, radius parts. Tremchal folders are used for processing copper, iron, steel, zinc and other materials.
Pourbiles have an additional roll at the bottom that simplifies the rolling process.
A sheet of hot metal, the front part of which is made using a bending shaft between the upper and lower cylinders are placed. In the process of folding sheet metal gradually spinning.
The most used rollers - 3 and 4 rolls, have each difference between them:
- Treblakoy.
- sheet thinner slightly slips between shafts;
- metal sheet rolling speed should not exceed 5 m / min;
- the clamping point of the sheet does not have accurate coordinates due to which the machine to control the machine is more complicated;
- low cost.
- Pour collection:
- all rollers provide a reliable clutch and the probability of slipping sheet minimal;
- rolling speed can be more than 6 m / min;
- the process of operation is automated, the operator must only enter the operation parameters of the machine;
- overcharge.
By way of flexion, the rollers are divided into:
- dornish. They are able to perform deformation of thin-walled pipes;
- segment. Pipes are bend under the action of a separate segment, which pulls the pipe;
- spring. The presence of a spring, which bends plastic without its deformation. This is a manual method of processing materials;
- arblet. They are intended for pipes of a certain diameter.
Types of rollers
Machines are several types:
- Manual rollers are the most convenient and practical device for deformation of materials. Difficulties in working with the device does not arise, in addition, such machines do not need to be connected to the network. Clamps and feed rollers operating with a chain transmission are fixed on the main bed.
Profile rollers with manual drive are most often used for single production, and not for a trap. Such devices allocate a number of advantages:
- durability, reliability of the design and simplicity of working with it;
- small sizes of the roller machine, due to this, it takes little space;
- simple adjustment of the lower and rear rotating shafts;
- the upper shaft is removed;
- low price of the machine.
Walves jewelry manual are widely used by jewelers to perform rolling and rolling of flat blanks and wires from metal, to give them the desired form. As part of the working cylinders of jewelry rollers wear-resistant carbon alloy steel. Such rollers have a powder coating that protects them from corrosion.
It is necessary to use additional efforts to work with the rollers of manual fixtures, since manual machines do not work from electricity and the main guide mechanism in them is a special pipe. For processing on such machines, small metal products will rise.
- Hydraulic rollers - hydraulic drives are characterized by high power. The rolling machine is estimated by professionals as the most high-quality and high-performance unit. However, he is pretty weighty, and setting it once, it is unlikely to be independently moving the machine from place to place without help.
- Electric rolling machines have the greatest performance due to the operation of the electric motor, which allows you to quickly deform the pipe between the rollers. The principle of operation of this model resembles manual, but there is a motor here. Such equipment is often used in industrial production and has many positive feedback from consumers. The only minus is an overestimated price of electromechanical equipment.
Rolling machines in the home workshop or garage should be:
- mobile. Such a machine should be easy by weight for ease of movement;
- occupy a little place;
- low-power and saving electricity. The machine for 20 kW makes his work very quickly, but it consumes a huge amount of energy. His work simply may not withstand wiring in the house. As an option at home, you can use rollers with a capacity of up to 1500 watts, as well as manual.
If you, for one reason or another, does not fit any of the above options for rolling machines, then you can also make the rollers with your own hands, because few of the major repairs can do without this machine.
Purchased or homemade machine
Of course, not to spend your time and effort on the manufacture of a home machine, for calculations of rollers and loads, it is much easier to buy it. However, the stumbling block in this case is the price of the finished purchased equipment, which varies in the range from 20 to 35 thousand rubles.
It is possible that the design that you are going to erect using a roller machine, it is much smaller than the device itself.
And if it's not in your plans to build an openwork fence or gazebo, then such expenses for the acquisition of a professional roller machine at all. Try to make the machine with your own hands.
If you managed to create a device for deformation of metal products, then applying it in practice, take care that the following defects are not allowed in work:
- the appearance of cracks on the metal profile. Otherwise, the detail must be thrown out;
- avoid compression and stretching the surface at the load point on the structural element;
- compression or deformation details before rolling.
If you decide to make the machine yourself, then for the further convenience of working with it, it is advisable to combine its work with an electric drive. For this, any motor with a gearbox will be suitable, which will simplify the process of performing metal deformation. With a steel pipe that is mounted on a regular jack, make a clamping device for the profile. Thanks to such uncomply add-ons you can get high-quality finished products.
Rollers do it yourself
When self-assembling rollers, it is important to comply with some sequence. There are also certain mechanical skills.
Before making the rollers with their own hands, you need to prepare a set of desired materials, details, as well as plan the drawing of future rollers.
Walts assembly stages:
- The manufacture of rollers begins with the mounting of the main bed. To do this, you can use a curved profile or frame of pipes.
- For vertical support, use a P-shaped profile. In its upper open part, set the deforming element of the rolling mechanism. For its attachment, you will need a carbill clamp. The lower part of the support is attached under the bed.
- To assemble the rolling mechanism you will need a gear ratio.
- After installing the chain on the asterisk, it must be pulled, then check the simplicity of the stroke and start mounting the feed handle.
- For the manufacture of rollers, hardened steel is best.
- In the finished roller machine, refer to the radial adjustment, which will change the size of the gap between the working rolls.
- With the help of rolling bearings, fasten the rollers to the beds.
Jewelry rollers do it yourself
The rollers for jewelry work are performed in this way:
- Using the lathe, turn out two shafts. To do this, the alloy steel SHH15 is suitable.
- Treat holders for rollers on the milling machine, they may be non-calennic steel. Insert the gaskets from brass or bronze for a good slide roll.
- The lathe and the cutting machines will help you to pull out and harden the gears that are necessary to transmit rotation from the handle to the rollers. For gear, carbon steel X12 is suitable.
- Set of jewelry rollers ready. At the end, it is necessary to clean all the details, polish them and collect them.