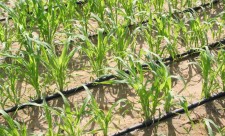
Liquid waterproofing of floors with their own hands Floors
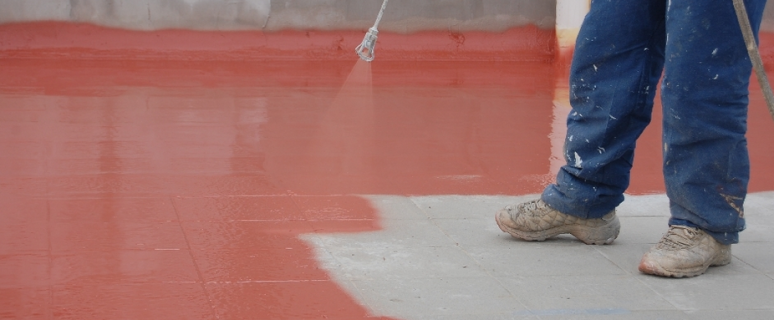
Make a dwelling dry, warm and cozy will help qualitatively performed floor waterproofing. The modern building market offers a huge variety of materials with which the floor can be protected from moisture. Liquid waterproofing means are very popular today, which create seamless, reliable coating and penetrate even in hard-to-reach corners of the rooms.
Content
Liquid waterproofing floor in the apartment: advantages and properties
All moisture proof can be divided into 3 large groups: rolled, mastic and liquid materials. The last option is becoming increasingly popular thanks to this advantage:
- First, liquid compositions are distinguished by high elasticity. This means that it is possible to use them even in the newly built house, after shrinking the building, the moisture protection layer will not suffer. Due to its flexibility, the material is able to withstand a significant water pressure reaching 25 atmospheres.
- Liquid waterproofing for the floor is not afraid of groundwater, ultraviolet and many other negative surrounding factors.
- Similar materials are environmentally friendly, they can be used without fears in residential premises.
- In contrast to mastic, in the component composition of liquid waterproofing there are no volatile substances that evaporate in the drying process and reduce the thickness of the moisture protection layer.
- Working with similar substances is much easier than with rolled and mastic counterparts. The liquid compositions are easily applied to the surface and penetrate even in hard-to-reach zones: angles, seams, slots, etc.
- It is possible to cover with such waterproofing with absolutely any types of bases. Moreover, the membrane layer will protect the structure not only from water and moisture, but also from corrosion and temperature fluctuations.
- Materials drying time is very short.
- Despite the fact that the price of liquid waterproofing of the floors is relatively high, long coating service life will justify all costs. In addition, it is possible to apply insulation. Firstly, it is quite simple, and secondly, it will save on the wage of hired workers.
- You can use liquid compositions in any rooms and in external finishing works.
Liquid waterproofing of floors with their own hands: types of materials and methods for their application
Hot waterproofing
This type of work involves the use of special materials heated to high temperature. Two types of hot insulation are distinguished: asphalt polymer and asphalt. Substances that are used in a similar case are bitumen, asphalt or pec. After soaring, the materials acquire good elasticity, strength, resistance of bending. The coating is durable and reliable, although it is not so often to meet it in apartments. To a greater degree, hot cast waterproofing is used in private houses.
Work on the application of hot bitumens on the basis can be described as such a sequence:
- From the floor first remove all the garbage, dust and other pollution.
- The surface is then carefully examined for defects. The junctions between the plates, cracks, gaps and other deepets are necessarily sealed.
- Paul leave until he finally dike. To speed up this process, it is often resorted to the help of heating devices with high power, for example, use infrared heaters or gas burners.
- The dried surface is necessarily ground. For this purpose, hot bitumen is used, which is applied to the floor with a thin layer.
- If the waterproofing will cover only part of the room, the working area is separated from the rest of the area using the formwork.
- When preliminary works are completed, the selected material is warmed up to the desired temperature. As a rule, such information is indicated on the packaging with the goods.
- Then the preheated composition is poured onto the surface and distribute it to the wrath, forming a uniform layer.
- Hot composition is allowed to completely frozen.
- If you need to do several layers, after solidifying the material it is covered with another portion of hot bitumen and in the same way align the surface of the rocket.
Cold waterproofing
You can protect the floor from water and moisture using cold cast waterproofing. Materials that are used to carry out similar works can be divided into 2 main types: liquid glass and liquid rubber.
Liquid tires is a material that is manufactured based on bitumen and includes various polymer additives. These additives give the finished coating greater elasticity, wear resistance, strength and durability. Calcium chloride is added to bitumen-polymer mixtures - it reduces the density of the substance and makes it possible to apply insulation by spraying. By entering calcium chloride into liquid rubber, it is pre-bred by water in the proportion of 1:10, after which they are stirred with the rest of the components.
It is possible to work with liquid rubber at a temperature not lower than 3 ° C and on a thoroughly prepared base. Since the material is produced in different consistencies, then there are several ways to apply it:
- A bulk method is considered the easiest and fast. It does not need special equipment for its implementation, and liquid rubber when pulling it into the floor is fill with itself all the pores, cracks and cracks. The finished coating is flat and smooth.
- Liquid rubber can be applied by spraying, but for the implementation of this method it is necessary to acquire special equipment. The coating created by spraying the material to the surface is obtained by the highest possible, since the substance is supplied under high pressure and fills even the smallest pores.
- Rubber applying in a coating method is the most affordable and common option. To hydroize the floor in a similar way, you should purchase material with paste consistency.
Consider the benefits of liquid rubber as water repellent:
- such a composition is perfectly connected with any surfaces;
- he is not afraid of the effect of aggressive chemicals;
- the water-repellent layer is obtained seamless, the moisture will not be leaked through it anywhere;
- even old floors can be waterproofing liquid rubber, only they need to be cleaned;
- rubber is characterized by good elasticity, shock loads and temperature drops are not terrible;
- it does not have a sharp smell, environmentally friendly, suitable for use in closed residential premises;
- the material has a long life.
The technology of waterproofing floors of liquid rubber can be described in the form of such steps:
- First, the work surface must be prepared. To do this, the floor is equalized, the slots, chips, dents and other deepeners, are shuffled in it, and the protrusions are cut and grind. Then the base is purified from dust, dirt, garbage.
- Then the surface is opened with primer. To work with liquid rubber, it is better to use the primer close to the chemical composition to the waterproofing material. This means there may be a polymer-bitumen solution that will ensure good grip of the material with the floor. The primer is the most convenient to apply a large brush or roller, after which she needs to give time for complete drying.
- The next step is the surface coating with liquid rubber. If the waterproofing is carried out by spraying, you need to get a compressor installation. Such a device connects the containers in one of which contains a bitumen solution, and in the other - calcium chloride. In the process of operation in the compressor installation, both substances are traded simultaneously, which are under high pressure on the floor and create a solid elastic film.
- If liquid rubber is applied with a liquid method, then the desired amount of the solution is simply poured into the prepared surface, and then roll over its ox. After that, on the floor passing a needle roller to remove air bubbles from the strata material.
- The substance freezes about two days when the floor is ready, you can start laying the finishing finishing materials.
Covering floor liquid rubber, it is also desirable to process the lower part of the walls, tap pipes and nozzles.
The second means for cold waterproofing is liquid glass. According to its consistency, the substance resembles the previous analogue, but the glass includes other components: soda, potassium or sodium silicate, as well as quartz sand. Waterproofing floor with liquid glass has a lot of advantages:
- Such material has antiseptic properties, it means that fungi and mold will not be installed in the room.
- The treated surface has excellent water repellent characteristics. In addition, it turns out smooth and seamless.
- Another plus of liquid glass consists in its antistatic properties.
- The material does not just protect the floor from moisture and water, but also gives concrete additional hardness and durability.
- Good adhesion and ability to penetrate the smallest pores of the base should also be attributed to the benefits of this means.
- Liquid glass can be applied not only on concrete, but also on wood.
- Often, the waterproofer is added to the composition of liquid concrete, to improve its water-repellent characteristics.
- The indisputable pluses of this material can be considered its affordable price and economical consumption.
Consider and some minuses of liquid glass:
- A layer of such waterproofing requires the mandatory arrangement of decorative coating, otherwise the glass collapses for 5 years.
- The material is not used to apply onto the brickwork, as it spoils it from the inside.
- Glass is a fragile material that does not tolerate shock loads. This reason confirms the need to arrange the finishing coating.
- It is necessary to work with such a means quickly because the composition solidifies in a matter of minutes.
We describe in detail the process of using liquid glass as a water-repellent material:
- Liquid glass is used in two ways: as impregnation for already frozen concrete and as a component of fresh cement-sand mixture. In the first case, the consumption of substance will be approximately 150-250 g / m². The glass is bred by water to the desired consistency, then apply to the surface in 3 layers. Thus, the composition penetrates into the pores of concrete to a depth of 10 cm and creates a waterproof layer.
- When adding a means to liquid concrete, it is brought to the solution in the proportion of 1: 8 or 1:10. Subsequently, concrete is used as a waterproofing agent, applying it to the floor with a coherent way.
Penetrating waterproofing
Liquid waterproofing of the floor can be performed using impregnating materials. They fill themselves all the pores and holes on the working surface, penetrating into its thickness to a considerable depth. The floor treated with this method becomes durable and waterproof, cracks and supremes are not formed on it.
The construction market offers consumers a lot of various means of penetrating waterproofing, we will look at one of them - the mixture of Penetron. This product is a combination of cement, quartz sand and special chemical additives. Penetrated into the pores of concrete, Penetron crystallizes inside and creates waterproof barriers. The penetration depth of the substance comes to 50 cm, which is considered a very high indicator. Before applying the means, the floor is carefully moistened, and the better it will be moistened, the faster and the crystallization process will actively happen.
Penetron is sold in the form of a powder with a homogeneous structure that does not contain impurities and lumps. This powder is bred in water in accordance with the instructions. Then the mixture is applied to the surface and give it to dry. Penetron begins to capture 40 minutes after dissolving in water, and finally freezes after 3 hours. It is possible to start the finish finish of the floor not earlier than 14 days after the waterproofing of the floor by this material.
The surface covered with such a means becomes stronger, acquires waterproof qualities and is not afraid of the effects of acid and alkaline chemicals. Penetrating impregnation does not hydroize brick and stone masonry, as well as foam concrete and wood. Such formulations apply only for moisture protection of concrete grounds.