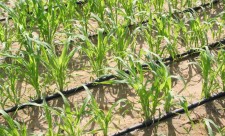
Balaasins do it yourself Ladder
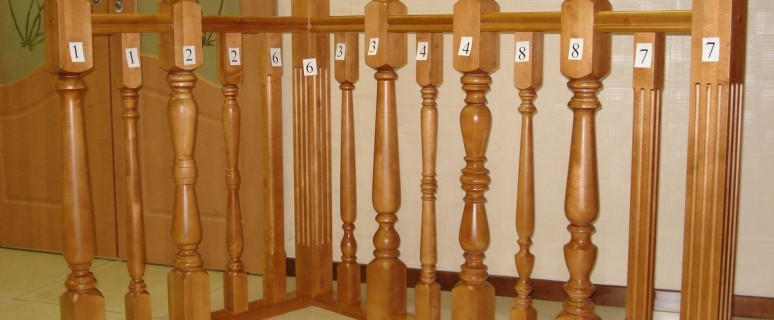
In order to correctly mount the staircase, you need to pay attention to all its structural elements, among which railing and balusters occupy not last place. The latter are vertical support racks, and, in fact, are the main details of the railing. These supports perform several functions. First of all, they support the railing. In addition, ensure the safety of everyone who moves along the staircase march, and are an element of the decor of the room. By itself, the baluster itself consists of several structural elements: Pinta is its base. It is a rack that is attached to the step. As for the central part of the racks, they mainly perform only protective and decorative functions. For their manufacture, wood, metal or concrete usually use wood. Nevertheless, today, decorators began to apply glass, PVC and polyurethane for this purpose. Balacine dimensions can be different. We will tell more about this part of the stairs further.
Content
Wooden bales
Production technology
For the manufacture of these racks from wood, three different technologies are used:
- The most common species are accurate bassines, i.e. Products that are covered with enviable accuracy on the lathe.
- Other technology implies milling. On the racks of this type there are various decorative elements in the form of cutting.
- Thread. It is often done on wooden balusters, not manually, but on special programmed machines.
In cross section, the product usually has a square or round shape. In addition, the flat options are made of racks that are actively used not only for stairs, but also for other designs. Such elements can be installed closely, and as a result, it turns out a single figure. This approach allows you to make enough complex ornaments, and quite large sizes. By the way, this will not work with metal balusters. After all, they are made strictly on a given template.
The production of flat wooden balasine begins with the preparation of the blanks of the desired size. In addition, it will be necessary to choose a suitable pattern, and then on the basis of all this is a sketch. Then the contour on the sample is applied to the workpiece. Next, the shape of the workpiece is fixed on the previously made electroller markup. Then proceed to finishing with the help of cutters. Thanks to them, all decorative elements can be treated so that they take a symmetrical form. When it is done, the products are glued, the handrail is mounted and varnished.
Selection of material
From the correct selection of the material will depend both the cost of the product and its operational properties. Poles and stairs for the stairs are recommended to do from one wood breed. This makes it possible to prevent possible deformation in the future.
Consider the main types of wood used for the production of Balyasin:
- To make wooden racks best use solid wood arrays. For example, the oak is perfect for this purpose. This breed of wood is primarily known for its high strength and resistance to wear. It is resistant to rotting, due to which the service life is quite long. In addition, oak products are not cracking and is not deformed that for balusne as for the decorative element is quite important. Due to the dense structure, the oak array makes it possible to make parts of a rather complicated form.
- Almost the same sturdy products from beech. At the same time, they are very plastic when installed, it is easily processed and bent. This wood is easily soaked in various compositions, which increases the service life of varnish or paint surfaces. Of the disadvantages of this material it is worth noting the fact that it is susceptible to rotting and dryly is strongly deformed. Therefore, when using a balasine of this type, it is best to maintain a low moisture level. The beech is often used to simulate such expensive rocks like a red tree and nut.
- An ash can be used for the manufacture of bassine. Externally, this wood is similar to oak, but less durable and firm. The structure of the ash is rather elastic and dense. It is good because the racks to rotting, which significantly increases its service life. The ash has a beautiful structure of a yellowish shade with light and dark splashes.
- Less often for the manufacture of wooden balasine used birch. This breed has average density characteristics. At the same time, she has a good viscosity. However, this wood has a tendency to the appearance of cracks. In addition, it is susceptible to rotting. Nevertheless, birch is quite good to process, easily glued, polished and painted.
- Balasins can be made from larch. In the finished form, these products have a brown and brownish shade. This breed is less solid than oak. Nevertheless, it is more durable, and over time, the strength is only increasing. The larch is almost not deformed over time, but when drying is possible, the appearance of internal cracks.
- Wooden balasins are also made of such soft wood like pine. It is good because it is easy to handle and grind. Balasins from this material are immune to the temperature difference and racks for the appearance of fungus. From the disadvantages it is worth noting that due to inhomogeneous porosity, the paint is absorbed into it unevenly, and this reduces the quality of the coating.
How to make balesins
Different forms of Balyasin require a different approach to their manufacture. And each production technique has its subtleties.
For example, flat bales are performed from polished boards or bars. The finished board first is cut into pieces, after which it is cut with a jigsaw contour by the template. It is usually more convenient to fold together the bars and on the upper part of them to draw the edging of the balusters. After that, there are several blanks at once on the marked circuit. Now it will be necessary stencils, with which the drawing of the future thread is applied. After that, using the edge cutters, the resulting pattern is carefully processed and cleaned with sandpaper.
Another option for the manufacture of flat balasine is that the common form of the product is given to the bruster of the required thickness. After that, it is cut into narrow boards, which already have ready-made contours. The further process is the same as in the previous method.
For the manufacture of square balasine, the timing of the desired section is first selected, which is then cut on the blank of the desired height, processed in the future manually. The most difficult thing in the process is to apply a drawing with the help of cutters. This work can only make a person with the necessary skills and knowledge.
As a blank for round products, bars are used, cut by specified parameters and manually processed or using a machine. Obviously, manual processing is more laborious. Therefore, more often the workpiece is processed on the machine. When everything is ready, it is manually applied to wooden sketches, if necessary, an additional picture.
Balesna from concrete
Product characteristics
Concrete balasins from the point of view of the building element are nothing different, as an artificial stone, which was first pressed in the forms, and then weathered with the desired mode. The process of manufacturing a balasine from concrete itself is mainly in a steam hardware.
Himsostav material used for the manufacture of bassine is similar to the polymer concrete structure. But in contrast to other similar products, there is a slightly different method of pressing and processing conditions.
In the industrial production of BALASIN, plastic forms for future products are required, the cement bunker, as well as a concrete mixer. In addition, you need such equipment like vibrotole and wooden pallets.
However, in the presence of certain skills, concrete balasins do with their own hands easy. For example, you can make products having a round shape. One of the methods of their production is an industrial casting. About this method will be more written below.
Method of production
For the manufacture of the model, a special form is made. It serves to cast the finished product. Molding for the model can be made of rubber, gypsum or plastic. It is manufactured using pulling or pulling techniques on a turntable technology machine. After processing inside, a dense rod remains, which can be easily removed. If the turntable is needed only at once, then it is wiser to make it out of wood. For industrial production, it is made of steel.
We will analyze a little more design and technique of operation of the machine to create molds:
- It consists of spindle, which has a rod and a handle placed on two handrails. At some distance from them the polished board is nailed. It has a dense one. Everyone assembled to a reliable workbench.
- At one end, they make special round necks. It is due to them that the rod can rotate. On the handrails of spindles do, or rather cut out, ears. They must rotate along the central rod.
- A layer of gypsum is superimposed on the spindle, which should be resistant after cooking for a couple of minutes so that it thickens. After that, turn the handle completely, cut off the extra plaster.
- Another portion of the gypsum is superimposed on unfilled voids of the mold and the full turnover is made again. When moving the polished board on the surface of the model, a rough coating is formed.
- In some places, the model is required to wind the packles moistened in the gypsum solution. This is usually done there, where the thickness of the plaster layer is at least 25 mm.
- When the template is moved over time, the model acquires a smooth coating. The product will be prepared ready when its surface will be completely even. For now, do not achieve, the model pulling continues.
- If necessary, it is added even a solution in a small amount. When it becomes a solid, the template must be stretched over the surface again, cut off the extra sections. It is required because the gypsum has a property of hardening when expanding, which is why the diameter of the baluster becomes greater than necessary.
- When the BALASIN model is ready, it is removed from the supporting cones. After that, it is necessary to cut her ends at right angles (for example, hacksaw). To increase the service life, the model is perfectly dried, covered with oil and varnish.
Next, you can begin the manufacture of balusters using the resulting form:
- First, the model is prepared and the round shape (35 mm) tile is cast. Ends are cut off.
- Next, it takes a slightly adjacent tiles to the ends of the balusters (for example, on the gypsum solution). When two face slices are laid, there are marking on three parts on the baluster. In order for them after bookmarking, they knew in the right place, marks are made.
- When this is done, the model with shares is put on the workbench, where sides from clay are made according to the longitudinal lines. They form a peculiar container for booking a third share.
- Little side parts of the baluster are covered with lubrication. After that, a gypsum solution is prepared, which is poured into the tank formed by the side. Next there is placed steel loop and fittings. It will play auxiliary role when lifting a piece after the casting of the baluster.
- When the gypsum hardens, the piece is removed, its edges are cut off, and the wells are arranged on them and a piece is placed in place. Then the model must be put in such a way that it is located on one of the fractions. The rest is divided into two equal halves. Thus, a new container is formed. Moreover, its internal parties are coated with lubrication solution.
- Further, a solution of plaster is prepared for laying a fourth piece, reinforced. Then the loop is inserted inside the same technology. When the gypsum hardens, then this piece must be removed from the model, trim the surplus, remove the wells, put in its place.
- Next make the fifth part along the same technique. The product is rounded the product with equity pieces. Then all parts from the BALASIN model are removed. In one of them they make a circular hole with a diameter of 55-65 mm.
- After that, pieces are going. It is important that they keep tightly to each other. To do this, they are associated or put on the form "Cap" from gypsum. So that each part is in its place, the corresponding marks are made on the details.
- On both sides, firefights are formed from clay, one part is covered with lubrication, and the space between them is poured with a solution of plaster. So the first half of the "Cap" is laid.
- After soaring the plaster, this half is removed, the edges are trimmed. In order to make locks for the second part, the wells are drilled. After that, half of the casing should be put in place, cover with lubricant, prepare a gypsum solution and pour it into the open part of the mold. As a result, we have the second half of the "Cap".
- After, parts of the form and the "cap" reinforced. At the same time, it is attached for the convenience of mounting steel handles. In order to prevent the discrepancy of the casing during the casting, both halves are fasten with ropes, and bar is inserted between them. If there is no rope, you can use steel clamps.
If you remove all content from the form, it can be used to cast a balaasine from cement. The finished molds succeeds, after which is covered with varnish. Before drying, you can treat it with oil. Casting can also be performed in crude form, but in this case the product is most likely deformed and not suitable for future use.
If the dimensions of the balaasine exceed one meter, it is recommended to lay eight pieces of eight pieces instead of three. The process itself is performed in the same sequence. In particular, the number of parts of the housing will not change, i.e. There will be only two of them. Each of the pieces need to be reinforced, and insert a loop into it, with which it will be removed from the finished baluster. At the same time, do not forget to make the necessary labels in the casing.
Industrial casting Balyasin
As mentioned above, one of the ways of manufacturing a bassine is the method of casting in finished industrial forms. When using it, the upper part of the mold is made as a cover with a hole. Through the recess, the form is filled with a solution. After filling out the shape, it closes the plug. In order for the solution evenly distributed through the walls, the mold begins to rotate in the horizontal plane. It continues for about an hour, after which the form understands, and the casting is removed. The resulting product then need to be securely secured in a vertical position. And it should be sinking about a day. Then it is laid out horizontally on wet sand.
Balaasins from stone
Balaasins made of stone will decorate any interior. This luxurious material has a number of advantages, among which strength, durability, wear resistance, attractive appearance.
For the manufacture of stone products, the following breeds are used:
- Granite.
- Marble.
- Sandstone.
Often comes to replace these materials, artificial stone, which costs much cheaper.
The method of manufacturing a balasine from stone is similar to the technology of concrete products. For this, the method of casting is used. Initially, the billet from the tree is cut, according to its template there is a form of plaster. And directly in the gypsum mold is already a solution that, after drying, takes the form and texture of artificial stone.
Balaasins: photo