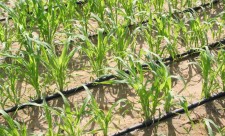
Stone cutting: description and methods Useful advice
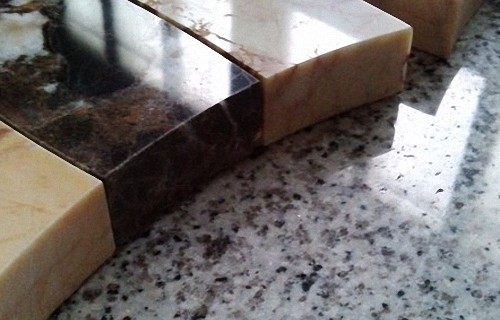
Most natural stones have a formless and massive breed, so they need to be processed. One of the easiest and most common ways to work with stones is their cutting. There are several ways to perform this process, which and talk further.
Content
Stone Treatment: Methods and Technology
In the mechanized type of stone industry there are many technologies that allow processing stones and make their surface textured and attractive. We offer to familiarize yourself with the most common stone processing methods in industrial conditions:
1. Sawing - This method is carried out in the process of cutting stone. For operation, machines are used on the saw frame of rectilinear disks. They are equipped with ribbon and rope saws. After the piece of cutting, the surface acquires a small roughness, and the deep grooves do not exceed 5 mm. This stone will become excellent material when performing platform pavements, roots in the garden, facades, etc. Also these products are subjected to fine-handing in the form of grinding or polishing.
2. Grinding - stone processing with a grinding circle on specially intended machines for these purposes, which can be grinding volumetric blanks. The stone becomes uniformly rough, irregularities on its surface have drops of 0.6 mm. This method of processing is perfect for a light shade stones that do not have a pronounced drawing. If you use it for a dark stone, then the drawing is instantly branded. The grinding stone will become an excellent material in the decoration of stairs, floors and streets of the street type. The stone significantly reduces slip, so boldly used in the data finish of the elements, as well as pools.
3. Achievement of the gluing product texture is carried out in the process of using a grinding wheel, which has a coating of micro grinding powder, usually diamond. Stone acquires a smooth, but not hazard surface. The product texture becomes more noticeable. This stone is perfect for facing the facade of the building.
4. Polishing - a stone processing procedure, in the process of which the withdrawal surface is polished using conveyors with circles having powder sputtering. Next, the material is processed with circles from felt or special matter. The use of chemical compositions helps to achieve a certain shine for stone. Its color becomes more saturated, and the drawing is completely revealed. The processed stones are used in the process of finishing the inner parts of the room, for the construction of tabletops, etc.
5. The use of shell processing helps to achieve a certain kind of depression not exceeding 4 mm. The stone becomes more attractive and acquires a certain sophistication. The material is applied in the external finish and when performing special design solutions.
6. The use of thermal technologies helps to achieve the effect of molten stone. This technology is carried out using a thermo-gas-jet machine. In this case, the color and texture of the stone appear very well, and its surface seems a bit melted. This kind of material is used in the process of decoration of steps, facade parts of buildings, etc.
7. Creating a rocky texture allows you to imitate coarse processing of stone, while the depressions and protrusions range from 5 to 10 cm. This effect is achieved by the creation of certain rock rocks. The material makes it possible to emphasize the importance and importance of the building, used when finishing the facade sections.
Cutting stone - features and types
Stone treatment using modern technologies involves their division into two types:
- mechanical;
- mechanics and physical.
The first category includes one of the most common ways - in the form of cutting, rocking and shock destruction.
In the process of the cliff, it is possible to achieve an invoice that makes a stone look like a rock.
Stone cutting - is the most popular way to process it. It uses technology that assumes sawing disk, cable or string type.
Disk technology sawing implies the use of disk mechanisms in the process of cutting. This technique is characterized by high prevalence, it is divided into such types:
- standard disk;
- diamond disk;
- cold.
The cable method of sawing allows the cutting of any kind of stones, regardless of their density and structure. Severe 3 main methods for performing this cutting method:
- cable using abrasives;
- cable-diamond;
- the use of fortified washers made of solid alloys.
In the process of the production of products of the tested type, the widespread is a shock method of cutting. It allows you to achieve the exact texture of the manufactured product and is used in the process of cutting certain parts, such as steps on the staircase.
Another common way to process the stone is the use of ultrasound devices and an abrasive medium. The process requires a large amount of time, but the processing has the highest accuracy.
Physical and mechanical processing methods involve the use of high-frequency current or thermoactive gas burner. They are widespread in the process of manufacturing monuments from stones that have particularly high strength.
Stone cutting at home
Considering the degree of complexity of working with stones, they are divided into products with a solid or soft structure. Soft stone is easy to handle a tool that is available at home, and is used to work with metal products. For hard stones processing requires a special tool.
For the processing of stones at home, a special room has a venge-type ventilation system. Since the cutting process highlights a huge amount of stone dust, which bears harm to human health.
Cutting at home must be accompanied by a constant supply of water, which contributes to the cooling of the cutting tool and reduces the separation of stone dust.
To perform a coarse cutting, it is enough to use a grinder with a special nozzle in the form of a disk by stones. For more accurate machining, a machine is required for cutting a stone having a metal moving platform.
The easiest way to process the stone at home is abrasive, that is, stone cutting with water. It consists in begging on the surface of the plate made of cast iron, a special powder that is poured with water. Next to the surface put a stone and perform friction until the stone acquires the desired shape. Please note that the stove must be made exclusively from the cast iron, since it is this material that helps produce stones.
Before dragging, preview the stone for the presence of defects, try to highlight areas having a more intense and beautiful pattern. You should not throw out stones that have other inclusions, with the help of the correct processing they will look more natural and unique.
To facilitate the processing process, special machines are created, which are based on electromechanical drive. It appears in the form of an electric motor having an elongated axis with a capacity of 0.3 kW. If there is a necessary, produce a nozzle of a grinding stone, a disk saw, felt or polishing circle to the axis surface.
To implement direct cutting, an additional installation of the bath and a table will be required. For their manufacture, the tin is perfect. The bath will collect water that cools the mechanism during the cutting process. A stone is installed on the box that will be subject to cutting.
On the surface of the bath, you need to install 4 metal corners having holes. The bottom corners contribute to the fixation of the bath on the surface of the bed, and the table is attached to the top corners, on which there is a slot. In order to reduce the splashing of water during the cutting process, a special visor should be attached to the table. For its manufacture, it will be necessary to tin 1 cm wide, and 10 cm long.
To carry out water supply to the bath and a circle, it will be necessary to install a special pipe, with a diameter of 0.5 cm, and up to 1.5 cm long. It is put onto a rubber hose connected to the water supply.
At the other end of the pipe, a polyethylene tube is installed, which slightly concerns the circle during operation. Thus, the supply of coolant is carried out directly on the circle.
In the bottom of the bath, the steel tube is soldered, the diameter of which is 0.5 cm, and the length is 1.5 cm. The main function is the removal of water and slag, which was formed during the cutting process.
Assembly procedure as follows:
- the bath is installed on the bed, but not fixed on it;
- the axis dresses the cutting circle of diamond type, the diameter of which is about 10 cm, nuts are used to fix it;
- next, a table is fixed on the surface of the bath;
- circle and baths are made in relation to the cutting circle;
- make sure that the circle does not touch the edges of the slot;
- next, the bath is fixed with bolts;
- water is connected and the performance of the mechanism.
To carry out cutting, keep the stone exactly, gradually bringing it to a circle. Please note that it is better to mark the cutting line with a marker to produce accurate cutting. Since with a large battery, grinding will take a lot of time.
For cutting of a hard stone, a diapering hacksaw is also used to be installed with a diamond spraying wire. When carrying out such a cutting, constant water supply will also need.
Another way to cut the stone at home is to saw it. Buy a saw cutting saw - this tool is a modern, upgraded device used in construction. In the ratio with the principle of operation saw for cutting stone there are:
- manual;
- diesel;
- electric.
In the ratio with the scope of application they are divided into:
- jewelry devices;
- construction installations;
- industrial machines.
Hand saws are cheap and suitable for home use. Their cost is quite low compared to industrial installations, and for cutting it will be necessary to make considerable physical efforts, therefore, with a small amount of work, their purchase becomes quite justified.
A saw having an electric drive has the highest performance. If necessary, the highest power is better to use a gasoline saw blade.
In addition, the saw cutting saws are stationary and manual. The first option consists of a frame, engine, transmission and tool that performs cutting, is used in professional stone cutting. Differs reliability and durability. Manual saw is convenient in domestic use. It is mobile enough and has high maneuverability.
Each of the saw cutting saw has a special disk, which is based on the use of a metal case having a segmented edge from a diamond spraying. It is the presence of a diamond spraying that makes the device more productive and contributes to improving the quality of cutting. The speed with which the drive rotates depends on the type and power of the equipment itself. Note that with increasing the number of revolutions increases friction between stone and disk, and, accordingly, the saw is heated faster, during the heating process, the quality of the diamond spraying is reduced, which leads to the need to replace the disk.
Hydroabrasive Cutting Stone - Features and Benefits
The hydroabrasive method of cutting involves the use of aqueous solution, in which certain abrasives are present for cutting stone. This method implies the supply of a high pressure mixture. In the process of performing cutting, dust is practically not excreted, as it is mixed with water.
This cutting technology is based on the principle of erosion, natural destruction of stone with water.
Among the advantages of using this method, cutting should be allocated:
- high sharp cutting;
- the presence of a perfectly smooth edge of the surface;
- the ability to carry out art cutting stones;
- full absence of cracks or chips;
- lack of need for thermal impact on a stone that helps reduce its strength;
- in the process of cutting, the number of waste materials is reduced;
- the ability to cut the stones of different thickness and fraction;
- full explosion and fire safety cutting;
- environmental Safety;
- getting high-quality cuts.
Among the disadvantages of this method, cutting is distinguished:
- low speed of work;
- high cost of work;
- limited operation of the tools performing cutting.
Characteristics and advantages of diamond cutting stone
One of the most common and highly efficient methods of cutting stone is diamond cutting. With it, perfectly straight cuts are performed. Diamond disks will easily cope with the most strong rocks of stones, in the form of granite.
Two types of diamond cutting are distinguished:
- dry;
- wet.
The second method is more acceptable, since the dust formed during the cutting process is washed off with a liquid substance in the form of water. Thus, it does not settle in the air and does not bring harm to a person.
The stone cutting disc performs the function of cutting material. It has special sections having a diamond spraying. There are two types of diamond disks. The first implies the application of diamond spraying only to the surface of the teeth, and the second is on a holistic surface.
The diamond cutting procedure implies the gradual grinding of the stone, thanks to which it is not able to break or crack.
Among the advantages of the use of this method, the cutting should be noted:
- speed of work;
- high efficiency of the result obtained;
- accuracy of diamond cutting;
- lack of damage to chips or cracks;
- low noise performance.
Diamond method of cutting stone is characterized by such disadvantages:
- the inability to cut the enameled surfaces of the stones, since in the process of cutting, cracks occurs;
- cutting exclusively in a straight line;
- the need for recycling cutting line.
Cutting stone video: