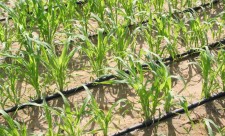
European technology screed Floors
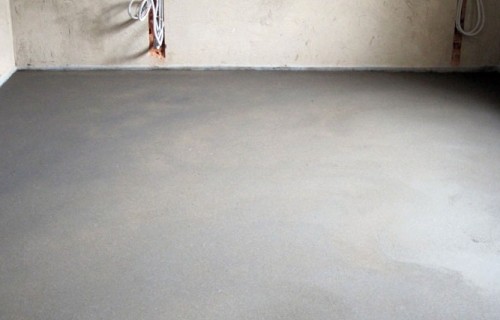
Floor screed is a layer designed to provide a layer between the main concrete overlap and clean floors. There are several types of screed: traditional sandy-cement, dry and liquid self-leveling mixtures.
Content
In his desire to optimize the process of laying floors and simplify the technology of laying a screed, builders often began to use the so-called "European" technology. It is a method of applying a semi-dry tie, with a decreased amount of water. Such a combination made it possible to obtain certain advantages, which will be discussed further.
Which is a semi-dry screed
The technology of a dry screed has its own definite disadvantages, but at the same time she gave an impetus to the development of semi-dry. There is nothing significantly new in the latter. The semi-dry screed is an ordinary cement and sand solution, when he is kneading a smaller amount of water. In this case, the consistency of the mixture allows you to fall asleep, and not fill. Thanks to this method, the arrangement of the floor is significantly faster and less expensive both by means and consideration.
Often, such a semi-dry tie serves as a stove for the foundation of industrial buildings, by analogy with mixtures for the draft base. So that the resulting mixture had additional strength, it is recommended to use reinforcing polypropylene fibers. The resulting additive from fibra will significantly increase the strength of the base.
Advantages and disadvantages of this method
Floor screed device technology for semi-dry techniques implies a reduced amount of water. Due to this, it was possible to achieve certain advantages:
- the finished mixture dries down much faster, due to which the time is reduced to the preparation of the floor under the finish coating,
- it is not necessary to use waterproofing materials, since the screed itself excludes the possibility of leakage. Moreover, the decrease in the amount of water in the composition led to an increased density of the material. In this case, there will be no extra voids and pores, which are formed during the evaporation of moisture,
- the semi-dry screed does not forms the shrinkage of the material, which is another advantage,
- the full cycle of drying the surface is only three days,
- the absence of dampness and dirt facilitates the work process,
- low price of the finished mixture, its lower weight compared to morally outdated fill methods,
- semi-dry screed ready for laying on the surface with a slope or with irregularities,
- a dumping screed when recpeding forms a perfectly smooth surface.
The technique itself is relative to Nova and often around it arise with wisdom disputes. Moreover, it has a number of significant drawbacks:
- since the mass does not have the fluidity, it is difficult to knead it,
- with insufficient seal, the screed may begin to crumble,
- with a lack of water, the process of cement hydration will not be completed, therefore further growth of cement crystals are possible. This is capable of determining the coating.
Semi-dry screed - the method is still quite new. It has significant advantages and due to skill, work on the arrangement of such a variant of the floor will not take a long time.
Process technology
The process of laying a semi-dry tie does not have significant differences in relation to wet. All work is conditionally divided into several stages:
- preliminary surface preparation
- laying of waterproofing layer,
- installing beacons and marks for leveling levels
- kneading the solution and applying it to the base,
- alignment of the applied screed and its subsequent grout.
Each of the steps is technically simple, but still you need to have an idea of \u200b\u200ball intricacies.
Preparation of floor base for tie
The surface preparation begins with the removal of an old screed, if any. After dismantling the old coating, the base surface is purified from dust and dirt. If desired, the purified surface is ground, but it is more voiced as advice.
Next, the calculation of the required amount of the solution under the damage is made. On the walls with the help level are drawn marking marks. Next is determined by the horizontal level. If possible, the laser level is used. This device is convenient because the laser dots on all walls are displayed. This greatly facilitates the process of placing the horizontal level and applying marks. Also correctly exposed the level will allow determining the amount of the desired solution. For example, for a standard room at 20 m2 with a height drop for each 1 mm, 0.032 m3 semi-dry mixture of screed, the cooking technology will be disclosed on.
Screed
To independently prepare a semi-dry mixture, it is necessary to prepare such components:
- portland cement,
- washed career sand,
- water,
- polypropylene fibers for reinforcing the mixture.
According to the requirements, the lability of the sand fraction should not exceed the mark of 2.5. The natural moisture content of the material is recommended, but since the exact values \u200b\u200bof the percentage of moisture in the sand is not, then you will have to determine the eye.
It is recommended to use portland cement 400d20 brand, in intact packages. If the operation of the coating assumes frequent load, for example, the floor covering of trade and exhibition premises, then in this case it makes sense to purchase a brand 500D20.
An ordinary tap water is suitable for kneading sand and portland cement. It is desirable to visually control the quality of water.
If there is no possibility to get a concrete mixer, then quite bye forces to build a container for the mixture with your own hands. For this, plywood or sheet of OSB is taken, from which the components are cut for plywood box. Next, they are connected to each other with metal corners and from the inside are coated with construction polyethylene to eliminate the mixture on the walls. The thickness of the sheets should be at least 8 mm to prevent excessive pressure on the walls.
The mixture itself is prepared in this way:
- three shovels of sand and one shovel of cement are alternately falling asleep in the container, while forming a slide of material,
- next, dry components are evenly mixed with each other,
- in advance prepared water, the reinforcing fiber fiber is falling asleep, at the rate of 80 grams of fibra on 10 liters of water,
- in a dry mixture, water is added to obtain the necessary thickness of the mixture. It is easy to determine the desired proportion to the eye. The semi-dry screed eventually should turn out to be sticking. In the compression in the cam made of the mixture, moisture should be released, while the mixture retains the resulting form,
Since the most common error in the preparation of a semi-dry mixture is excessive addition of water, it is necessary to gently add it to the mixture. Otherwise, the excess water will lead to the discharge of the mixture.
The process of laying a screed on European technology
After the surface was prepared and cleaned from various kinds of contaminants, it is necessary to begin this stage of work as the preparation of the hydro and heat-insulating layer.
As a material for the base, it is often recommended to use an ordinary construction film of dense polyethylene. The bands are stacked by peaks on each other, overlapping the joints of the edges. The edges of the film should start on the wall and rise above the stacked finish layer. The thermal insulation material is further fitted on top of the film. More often, fading the surface of the surface with a clamzite as a heat insulator. This superb material in its characteristics has the same non-aggression, environmental friendliness and low price. When dripping, they advise to mix varieties of different fractions - from rubble to clay sand to fill all emptiness.
The technology of semi-dry screed does not require additional reinforcement or strengthening of the structure. After frustration of the ceramisite or laying any other thermal insulation material, the basis is ready for a semi-dry tie. Next, the process will require the installation of signal beacons to place a level. Since the semi-dry screed has a higher density, the requirements for beacons are characterized by greater rigidity. Specialists recommend applying special T-shaped beacon profiles that are characterized by good structural rigidity. The first such profile is placed at a distance of 30 cm from the wall, the following are placed at a convenient distance. Lapered rails are fixed on the same cement solution that is used for the screed. All work should be done with the assistant, since the reduced amount of moisture in the prepared solution led to its noticeably faster drying. Due to this, all stages of work must be produced quite quickly. Ideally, the front of the work is distributed so that one person makes laying a semi-dry mixture in the space free between the beacons, and the other at that time was prepared a new portion of the solution.
The mixture itself is initially distributed around the perimeter between the beacons. At the same time, with the help of the rail, it is spilled and tamped. The mixture should fill out all the space on the floor, including beacons, which, after the fill, remain on the floor until their direct removal after the grout.
After the alignment, the grout stage of the prepared surface occurs. Experts recommend using a disk grinding unit for this stage. Its use will significantly reduce the cost of time, while the effectiveness of work itself will increase significantly.
In the event that there is no suitable tool at hand - a simple circle is used for grouting. With its help, the circular motions produce the surface to grow, while removing the remains of the semi-dry mixture and its influx.
The mixture is grabbed after 12 hours, while it is already able to withstand the load. At this time, the signal beacons and voids are removed using a more liquid cement solution.
The final strength of the semi-dry screed acquires 4 days later, after which you need to start the finish finish of the floor. The technology of the floor tie device itself does not have significant differences in relation to the fill methods of more liquid mixtures.
Finish work
As a rule, under the finishing works, the direct laying of the floor covering is implied. If all the stages of laying semi-dry mixture were made in compliance with the subtleties of the technological process, there should be no problems.
The perfectly smooth surface is suitable for direct laying of the floor covering on it.
As coatings, such types are usually used:
- linoleum is inexpensive and easy to install. Roughly speaking, often just roll out the linoleum roll on the room and the coating is ready. Modern varieties of linoleum differ in better ecology and texture. Given the low cost and the weak aesthetics of the linoleum, it is well suited as a budget option,
- laminate is good in that it simply imitates the texture of natural wood, creating the effect of laid outdoor coating from a natural tree. Among the competitors, the German company Egger is allocated among the competition, which provides a guarantee of 25 years even on simple lamella models, so at the same time noticeably surpassing competitors in terms of aestheticism and prices. It is difficult to find another option at a price and with such a wide range of characteristics. Unlike linoleum, solid floor coverings do not tolerate height drops. The same laminate allows deviation no more than 2 mm per 1 m2. Otherwise, when exposed to the load, the lamellae will be fed up and the damage to the connecting locks is quite realistic. That is why special attention should be paid to the finishing grout of the semi-dry mixture,
- parquet was always considered a symbol of wealth, since this material is different thanks to its naturalness and high price. In addition, the parquet board is rather demanding of care,
- carpet is a carpet imitation and is often used in the bedroom and living room. Like linoleum, carpet is not so required to the perfectly smooth surface, as a soft lifting structure allows you to hide disadvantages and surface defects. It also easily placed on the floor and often does not require additional fixation,
- ceramic tiles primarily apply in rooms with high humidity. In particular, in the bathroom. The tile is most complicated in the installation, since its laying should be made on the perfectly smooth surface. Otherwise, the drop will be easily noticeable at the jacks of tiles.
Of all floor coverings, this is the most expensive and complex, while the tile does not have due convenience and without subsequent coating can often be a trauma. Therefore, non-slip rugs are often placed in the bathroom.
In essence, each of the coatings requires a carefully conducted laying of semi-dry mixture.
Useful advice
To prevent the appearance of cracks on the surface of the finished screed, at the time of its arrangement it is necessary to cut special shrinkage in the material. They allow you to avoid the appearance of faults and cracks in a deep surface. The depth of shrinking seams should be at least a third of the entire labeled layer.
After laying, it is necessary to cover with a plastic film to save the necessary microclimate under it longer.
Another way to maintain the necessary humidity will be the periodic deposition of moisture on the finished surface of the semi-dry screed.
It makes sense in advance to consider the subtlety of the workflow and prepare all the necessary tools and equipment, since the semi-dry mixture begins to stick after 45 minutes. For this reason, the leveling of the surface and grinding should occur fairly operational. Floor screed, video styling technology: