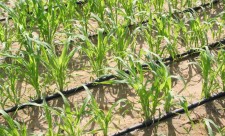
Device epoxy floors Floors
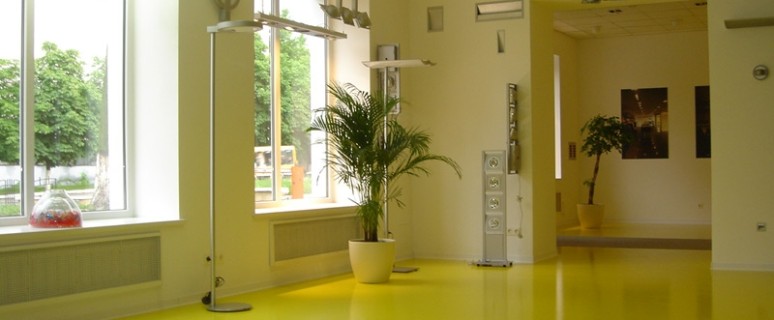
Epoxy floor is a modern coating, the distinctive features of which are strength, seamlessness, elasticity, high duration of operation and stability stability. About what qualities are polymer epoxy floors and how to make such a coating with their own hands, we will tell in this article.
Content
Features of bulk epoxy
Epoxy coating, also called two-component, is a mixture of two substances: epoxy resin and hardener. Sometimes other fillers are added to the solution, such as latex and casein, which attach additional elasticity and make it more resistant to damage. So that the floor has any tint, inorganic dyes are also added to it, and the epoxy floor with an admixture of polyurethane is considered the most durable and durable material.
The gender considered by our positive qualities is distinguished by many positive qualities, among which such:
- Monolith. The absence of seams is not only aesthetics, but also the key to the fact that moisture will not fall under the floor covering.
- Elasticity. This quality gives the floor high strength, abrasion resistance, temperature effects.
- Good adhesion ensures a reliable coating clutch with a base. The epoxy floor does not exfoliate from the surface.
- Hygienicity suggests that the coating is very easy to care.
- Resistance to chemical impacts allows the use of material in various fields, including in the chemical production.
The sphere of applying epoxy is quite wide and includes the premises of the most detailed destination. Such a coating can be found in residential rooms, laboratories, manufacturing workshops, enterprises, shopping centers and shops, in educational institutions, in hospitals, etc.
Despite the large number of advantages, the epoxy floor has disadvantages:
- Installation of coating is rather time consuming and lengthy, requires a very thorough leveling of the working base.
- The cost of epoxy floors is high, if you will attract specialists to apply material, financial costs will increase even more.
- If you do not comply with the right work technology, the floor can be buried.
- It is difficult to repair such floors, since it is not possible to choose the composition that perfectly suitable in color.
- Epoxy dismantling also not easy, it is much easier to lay a new material on top of the old floor.
Types of epoxy flooring
There are several main types of epoxy floors:
- Thin layer floors are most often used in residential construction. They create a polymer layer with a thickness of approximately 1 mm on the surface, which, nevertheless, perfectly copes with mechanical loads, protects the base from moisture and other adverse factors. The price of such epoxy floors will be relatively low because the consumption of the material is small.
- Tolstoneal floors can consist of several levels. As a rule, the thickness of each layer in such a coating also does not exceed 1 mm, but the largerness of the floor provides it with better strength and endurance. Tolstast coating are not terrible mechanical and chemical impact, moisture, high and low temperatures.
- Quartz epoxy floors are in their composition filler - quartz sand. This filler has increased adhesion and durability, transfers the load of any strength, is distinguished by a long service life.
- Industrial epoxy floors are considered the most durable among the analogues. The scope of their application is very wide. Epoxy industrial floors can be found in workshops and bakeries, in chemical industries, at the facilities of the transport sector, in pharmaceutical laboratories, in warehouses, as well as in public areas: in hospitals, schools, kindergartens, shopping centers, canteens, etc. Such coatings can withstand the strongest physical and chemical loads. They consist of one or more layers, they have different colors and textures, perfectly joined with any base, differ in hardness and durability.
Epoxy Floor Device With Your Hands
Requirements for the premises and preparatory work
Unfortunately, it is not possible to make epoxid sex in each room. To create a durable and reliable coating, the ambient temperature should be maintained at the level of 5-25 ° C heat, and this applies not only to air, but also the floor itself. The temperature of the polymer material, in turn, should be 15-25 ° C above zero. The humidity of the air should not exceed 80%, and the humidity of the base should be not more than 4%.
Check the humidity of the floor is easy, it will take a polyethylene film and tape. Fragment of the film should be glued to the base and leave for 24 hours, after which it was to see if condensate was formed from the inside. If the film was covered with water droplets, and on the floor there was a dark stain left - such a base cannot be coated with an epoxy mixture.
If the room complies with all the necessary requirements, you can start the installation of epoxy floors with your own hands. To begin with, the surface must be prepared:
- After necessary, the old coating is removed, the floor is aligned with a suitable way. For this, on the working basis, all cracks close up or simply poured a layer of a concrete screed. After drying, the surface is grinning and purified from construction dust and garbage. For grinding it is convenient to use a grinder with a diamond nozzle or grinding machine.
- After cleaning the floor, it is covered with a disinfection composition, and the primer. The primer will improve the grip of the polymer with the surface and will allow the material to go to the smooth.
Most often, epoxy formulations are applied to the concrete base. The wooden floor is considered not the best surface for applying liquid polymers. Wood absorbs moisture, which subsequently can affect the quality of the coating. However, sometimes the epoxy mixture is poured and wooden floors. To do this, they are cleaned of paint, polished, and in places, the floor connects the floor with the walls with a deformation tape. The polymeric solution itself is poured over the reinforcing grid.
Epoxy can be covered with ceramic tiles. First you need to dismantle the destroyed elements and replace them with a layer of concrete solution. After that, the floor should be projected, dried and coated with epoxy solution.
By performing primer application work, some subtleties should be taken into account:
- The primer can be applied only on the dry floor. If you collected dust something wet, the surface is better to leave for 2-3 hours until complete drying.
- As a rule, the primer is bred by water before use. The exact proportions of the components are indicated on the packaging of the goods.
- Conducting primer need the entire floor at once. In the work convenient to use a large soft roller.
- The type of solution should be chosen depending on the type of coating, which will be applied to the floor.
- It is desirable to give preference to the compositions that they have antiseptic properties. They need to be applied to the base 2-3 times, waiting for the drying of each layer.
Installation of epoxy coating
- The first stage of the device of the seamless polymer floor is the application of the base layer. As such a layer, it is the so-called epoxy soil, to prepare which is completely simple. For this, both components of the composition are mixed, leave it for 3-4 minutes, after which the solution is poured into the floor.
- A wide flat spatula of the soil is distributed over the workforce, trying to create a uniform layer with a thickness of up to 1.5 mm. Such a layer will dry at least 18 hours. Its main purpose is masking small flaws on the surface and liquidation of pores. The material consumption in this case will be about 400 g per 1 m² of the area.
- After 20 minutes the floor surface is covered with a layer of sand, its amount should be about 1.5 kg per m². To move on a flooded epoxy surface, the plane access is used. When the work is completed, you need to wait for a complete drying of the material, which will leave from 12 to 24 hours. During this time, it is categorically impossible to walk on the floor.
- With the hardened surface of the sand surplus, you can remove the brush. Cleaning the floor from sand and dust, it is once again coated with a layer of epoxy composition.
- On the base coating, you can apply a special film with a pattern or use any other decorative materials.
- When mixing components for filling the finish layer, a high-power mixer is used. Each subsequent batch of solution should be poured on the floor no later than 40 minutes after the previous one.
- When installing the finishing coating, it is desirable to provide deformation seams, the layer thickness can be adjusted using Raklie. In the process of work, it is also necessary to remove air bubbles from the thickness of the solution, for this use needle roller.
- The thickness of the finishing layer is 1-2 mm, and the time of mass of mass is 12-24 hours. You can walk on the finished floor no earlier than in 3 days.
Epoxy floors, photo: