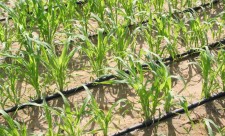
Formwork Shields: Mounting Features Construction

If you like to work with your own hands and want to proceed to large-scale construction of anything - a garage, foundation, massive fence - you need to explore the specifics of the formwork of the formwork. Shields are needed to keep building materials and creating smooth neat structures. In this article we will tell you everything you need to know about the device and installation of formwork shields.
Content
Design characteristics
The formwork is called a special auxiliary design, which creates the desired form of a concrete object, geometry and its position in space. There are many types of formworks, what you will make sure very soon, but all of them have common components: fasteners, supports and shields. It is the latter that are responsible for creating even forms and the proper quality of the whole design.
The formwork "works" is very simple - the shields are installed in the desired position and poured into the formed "ditch" concrete solution. When it hardens, the shields are dismantled, resulting in a solid and sustainable structure. In order for the design to be reliable, the formwork must comply with certain requirements - to be strong, not deform from loads, its deck (trim) should not strongly absorb liquid. Otherwise, all the water from the cement-sandy mixture will go into shields, and the concrete object crouches.
In addition, the formwork must be monolithic, that is, without cracks, otherwise the concrete will come out. Ideally, shields can be used repeatedly, but it only applies to the removable formwork. This moment we will touch later.
Types of opaling
For the entire practice of industrial and housing construction, many kinds of formwork were invented and worked out. Conditionally, they can be divided into two categories: removable and non-removable.
Distinguish the following types of formwork:
- collapsible-stopped;
- block;
- lifting-stopped;
- sliding;
- horizontally driving;
- non-removable.
For the manufacture of such structures, illiquid wood - boards, faeer and other materials remaining from the construction of other objects are used. Usually they do in everyday "home" construction to save money. In the industrial sector and during the construction of multi-storey residential buildings use steel or synthetic formwork. The rational means to make combined options, combining the carrying parts from the metal with shields from lumber, plastic or hydrophobic plywood. However, fully metallic formwork shields are in demand, since it allows you to get an ideally smooth surface and have almost unlimited service life.
Specificity mounting
The varieties of formwork exists practically as much as the types of objects of objects, and each of them has its own characteristics of the installation. Consider in more detail how to mount various types of panel formwork.
Collapsible-stopped
One of the varieties of removable formwork, consisting of shields and supporting parts. When working at altitude, single or complex supporting racks with connections and disconsets - scaffolding is substituted.
The process of using formwork:
- Shields put and fixed in position according to the project of the building.
- Paste the reinforcement and poured cement-sandy solution.
- After the concrete drying, the shields are removed and mounted on, extended object.
There is a large and small formwork. The first consists of large shields 2 m² of 20 m². Shields can be filled with each other throughout the edges, and if necessary, they can be supplemented with smaller shields of the same quality. Material for construction serves moisture-resistant plywood or metal sheets.
The small formwork consists of shields from 1 m² to 2 m² of frame or without it. Today, versatile structures made from universal parts, fasteners and mechanisms are most often used. Typically, the dimensions of the formwork shields are always the same - 30 cm wide and 10 cm - height. It is needed for the construction of tape foundations, walls, towers and even bunkers. Such versatility is explained by the fact that the shields can be connected on all grade.
Depending on the characteristics of the object, different types of collapsible formwork use, which should be made in a strict sequence:
- Wooden shields of formwork are used for a swallowed and fine-breed belt basement. From above and from the sides, the shape is sized with wooden clamps that take the side pressure from a heavy cement mixture. Inside the formwork there are struts that adjust the inner transverse width. On the sides of the outside, the centering stakes are nourished on which the guide boards are mounted. In more detail, the installation process we describe in a separate chapter.
- Such a formwork can be collected immediately for the entire height or first pour the lower part, wait for the drying of the concrete, and then rearrange the shields higher. For a bunned ribbon foundation, first installed on two sides of the trench every 3-4 m (the distance must be multiple or width of the shield) Special beacon shields for which you can navigate with further installation. They are fixed with piping or struts. After connecting beacons, it is embarked in fixing intermediate shields with tension hooks.
- Formwork for walls is usually made from large-sized shields, setting them first on one side. After mounting the reinforcement put a shield from the second side and tighten with the first bolts. If you use a universal formwork, first collect the panel to the entire width of the wall (if possible). To move such panels, a lifting crane is needed. First, the inside is mounted, strengthening it with struts, and then outer. When building high walls more than 3.5 m, it is necessary to mount a multi-tiered formwork with a support for the lower or anchor.
- For the construction of the columns use board or steel formwork panels, as well as mixed options. The wood version is a box of shields on the planks embraced by clamps. Upstairs such a formwork often eating holes framed by wooden bars to attach beams or runs.
- For a column height from 3 m, it is better to immediately build a full-size shield to not install additional fasteners. In the case of a multi-tiered formwork, the lower tier is recommended to be opened onto a wooden frame to make it easier to disassemble. If you build a high column with frequent reinforcement or a small thickness, the shield of the upper tier should be mounted only after completing the fill with the concrete of the bottom.
- After mounting the formwork in the vertical position, it should be secured with stretch marks.
- For the construction of the beams of overlapping, a formwork is needed with side shields and a bottom. The sidewalls are attached from the bottom by the boards, and on top if the height of the beam does not exceed 45 cm, they hold them transverse screed or formwork of the plate. In higher sidewall beams require additional fixation with screeds. The bottom in this case is based on the heads of the racks installed in a step of 1.5-2 m.
Also for beams and runs are applicable aluminum formwork shields and sliding clamps, with which you can easily adjust the dimensions of the future beam.
Block opal
For this type of formwork, steel shields and clamps (hinged or detachable) are used. It can also be gathered on welding. This block is a design of shields and carrier elements. In the corners, shields are tightly connected by locks. So that removable forms are easily filmed, they are made of cone-shaped, and for the separation from the frozen concrete you need jacks.
In order to save time and strength, it is better to first collect block formwork, and then raise it into the right position. Sometimes in blocks are collected in advance and install the reinforcement "skeleton", after which they are already put in the right place.
Lifting-stopped formwork
This type of removable formwork is collected from external and internal shields, carrying rings, supporting frame and devices of the radial movement of the outer part. For design, steel panels in the form of a rectangle or trapezium are used. The latter make conical objects. The formwork shield thickness is 2 mm. All panels have standard dimensions: rectangular - 270 cm in height and 85 cm in width, trapezoidal - 270 cm in height, 85 cm wide at the bottom and 81.8 cm at the top. To fasten the shields, bolts are used that pass through the frameworks and the lining at the top of the panel. The outer formwork is equipped with closing panels through which tightening bolts also pass.
The inner part consists of 125x55 cm shields folded in 2 tiers. From the outside, the planks with brackets, in which the struts lay, are welded. The top side of the shield is attached a horizontal bar with rings for which the rope ties to move the shields. To set the upper shield to the bottom you need to block the horizontal bar side brackets. Final shields with a single bar are used to close the inner formwork.
The outer formwork panels hang on carrier rings, after which forests are installed. The mechanism helps not only move the formwork, but also change the diameter of the object. The lift is the head of the frame and the frame to which the remaining elements are attached. It works as follows: First, the framework is based on the lift and put the frame in the extreme position. When the nuts begin to rotate, the frame rises by 2.5 m, and the frame at this time remains in place. Then the lift is increased by 2.5 m and perform concreting.
Sliding opal
This type of formwork is needed for the construction of silos, multi-storey buildings and towers. Moving vertically, it does not lag behind concrete, unlike other types, and slides on it.
The dimensions of the formwork shields are in height range from 1.1 m to 1.2 m and are located outside and inside the concrete wall. To reduce friction strength during movement, shields slightly expanded the book. It also helps to avoid disruptions and concrete loans when moving formwork. Domestic frames and rods put on the perimeter of the concrete object with a step of 1.2-2 m.
Useful advice: In order for the concrete during a break, the jacks should be installed in the "step in place" mode, turning off the lower clamp.
It is extremely important to install jacks on a strictly horizontal surface and move them evenly vertically, otherwise it is not to avoid the felt of the concrete and the curvature of jackstone rods. In modern models, this problem is solved automatically by means of a built-in horizontal regulator. Such models usually have high lifting capacity, so suitable for large-scale construction. The average speed of work with a sliding formwork is 3m / day.
Horizontally moved opal
Unlike the previous species, this formwork works almost without stopping. This is achieved by constant sliding on concrete or moving them with a periodic margin. Such a formwork is necessary for the construction of extended structures like concrete walls or fences. It is a hard frame on racks, 2 trolleys and a beam connecting them. Installation of formwork shields is carried out between guide racks, which simultaneously hold them, take the load from concrete and transmit effort from the horizontal movement device to the shields. For movement, the electric conductor installed on the upper beam or the rail path from the autonomous mechanical drive is used.
With the help of such a formwork, you can build a wall to 6 m on average from 6 to 8 m² per hour, which is pretty fast.
Failure opal
Any formwork is necessary to create the form of a future object, but in the case of removable structures, this shape after filling and solving concrete is dismantled. When using a non-removable formwork, the whole design remains attached to concrete, increasing its strength, durability and other operational characteristics. Since formwork does not need to be removed, it significantly reduces construction time and labor costs.
Advantages of non-removable formwork:
- One of the main advantages of a non-removable formwork is its technological simplicity - when building a building, it is almost impossible to be mistaken. The blocks of the object are joined on the principle of the "LEGO" constructor connections of the spike groove. Even a person without professional skills will cope with such work, the main thing is to follow compliance with the proper geometry of the eared object.
- A non-removable formwork allows you to build at home almost on any soil and even in seismic zones (up to 7 floors). Strong reinforced concrete walls, surrounded by a "shirt" of formwork, are able to withstand strong pressure and avoid mechanical damage.
- Plus, the non-removable formwork protects concrete and reinforcement inside it from the effects of moisture, chemicals, keeps heat inside the house. If you use removable panels for formworking the foundation, then after dismantling it will need solid waterproofing, which is quite expensive. In the case of a non-removable formwork, it is enough to use inexpensive protective coatings to secure the base of the house from the destruction and heat loss.
- Since non-removable formwork shields have a smooth and smooth surface, then carry out the inner finish of the walls, built in a similar way, much easier and faster. In most cases, shields are made of durable polystyrene foam. He perfectly holds heat, practically does not pass water and allows the walls to "breathe." It can be easily cut to an ordinary knife, which will greatly facilitate the installation of communications and electrical wiring.
- The non-removable formwork is popular not only because of its simplicity, but also because it helps save a lot of money. So, 1 m² of brick wall without insulation and finishing will cost you 2 times more expensive than a warmed and durable concrete wall that practically does not require alignment.
Formwork do it yourself
In this chapter you will learn how to make shields for formwork with your own hands. Of course, we will not affect the complex mechanisms described above, and we will tell you how quickly and inexpensively organize a formwork for "home" construction without the use of heavy equipment.
Removable opalk
Removable formwork made by their own hands allows to significantly reduce the cost of construction. It will come in handy if you have conceived to build your own home on the plot, a garage or a small extension. It is most often used to fill the ribbon or monolithic slab foundation. But since removable shields allow you to attach almost any shape to concrete objects, then you can make even decor, interior, furniture, furniture, and everything that is enough fantasy.
To create a removable formwork, use the moistureproof pheaneru, steel or aluminum sheets, ordinary wooden boards remaining from construction.
Useful advice: If you use wood, cover it before the fill of the concrete of the waste machine oil so that the shields do not stick to the cement mixture.
Metal formwork is usually used for large-scale construction, and it is often easier to rent it than to make it yourself.
Faneru is better used to create small partitions or small-sized objects. For the foundation it is recommended to make a wooden design.
Regardless of the material selected, there are certain requirements for removable formwork:
- High rigidity and frame stability.
- Maximum dense and precisely fitted elements (without cracks).
- The ability of formwork to withstand strong pressure all over.
- Weak adhesion shields with concrete.
- Shields should not be fed or deformed from the pressure of concrete, especially if the formwork will be used several times.
Useful advice: To make a removable formwork, select the boards with a thickness of 25-50 mm of arbitrary width (the wider board, the higher the risk of cracks in it). The optimal width is 200-300 mm. Squeeze the boards into the shields of the required height, attaching them to wooden bars from the outside. Hats nails should be inside formwork. Do not leave the slots between the ends of the boards. If still there are openings at least 2-4 mm, they need to close the packs, if more wider - to drive there a rack of the corresponding thickness.
How to make a removable formwork for a ribbon foundation:
- Prepare the surface by removing the fertile layer of the soil and dug the trench for the foundation. On how to dig a trench correctly, find out in the article. "Bulk belt foundation with your own hands".
- Taking the pegs, the twine or fishing line mark the perimeter of the future formwork in accordance with the project of the house. Cheing take deep into the ground around the perimeter of the trench. Parts turned inside must be from the stretched twine on the thickness of the shield so that the concrete object turns out to be smooth. The task of the pegs is to hold the lower parts of the shields.
- There are horizontal bars between the seals.
- Attach the shields to the stoles and bars and bring them the nails (take a ride). Watch that the inner side of the formwork is smooth.
- The tops of the bars strengthen the backups. For this, the board is 1.5 times longer than the height of the future foundation. One end to improve it into the ground, and the second - in the upper part of the support bar. If the foundation is fat, then the place where the board rests on the ground, it is better to strengthen, hacking the peg. Also in this case, it is recommended to link the formwork with additional jumpers from the rod.
Failure opal
We have already told about all the advantages of a non-removable formwork, so immediately proceed to the description of the installation process.
For the manufacture of blocks, materials with low thermal conductivity are used to create a surface and insulating layer at the same time and holding the concrete. With such a task, extruded polystyrene foam and arbolit copes with such a task. Of these, special blocks are made, which are collected like a designer and poured concrete. They are inexpensive, and benefits bring invaluable.
How to make a non-removable formwork:
- Place the polystyrene blocks in the manner corresponding to the project of concrete structure.
- Connect blocks with special locks "Schip-groove".
- For better concrete and the murdration of the solution, put blocks into several rows, reinforce and pour the cement-sandy mixture. Insert the valves into the grooves specifically provided for this and the voids of the blocks.
- After compaction and tamping assembly proceed to the next rows.
Important: Failure formwork is ideal for the construction of walls in low-rise buildings, but it is better not to use it for the foundation, since the blocks will not be able to withstand a serious load.